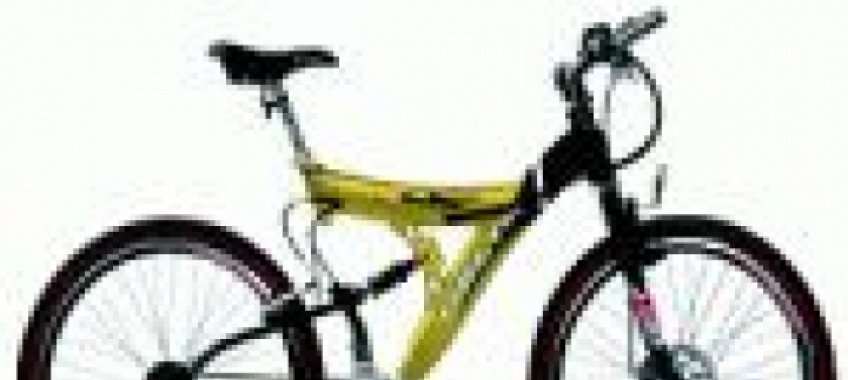
Ze względu na różnorodność asortymentu w branży rowerowej oraz wymagania klientów w lakierni używane są farby różnych producentów, w tym między innymi Pulverlak, ECO POLIFIX (ECOLINE), Pulverit, Wörwag, IGP. Zużycie farby przekracza kilka ton miesięcznie.
Powierzchnia jest przygotowywana metodą śrutowania - za pomocą oczyszczarki strumieniowo-ściernej.
W skład automatycznej części lakierni wchodzi również podwójny piec nawrotowy. Odpowiednia budowa i charakterystyka termiczna pieca pozwoliły zaoszczędzić powierzchnię hali. Niskie straty ciepła zmniejszają zużycie mediów zasilających.
Całość lakierni łączy przenośnik o pracy ciągłej. Prędkość grupy napędowej jest regulowana w zakresie 0-3 m/min w zależności od stopnia skomplikowania detali i wymagań produkcyjnych. Przenośnik wyposażony w grupę czyszczenia i oliwienia pozwala na sprawną i bezawaryjną pracę lakierni.
Dodatkowo zastosowano system pozwalający na pracę kabin zarówno w linii, jak i poza nią. W obu przypadkach cyklony nie zostają odłączone, co zapewnia ciągły odzysk farby. Ponieważ jest to system pracy ciągłej, a malowanie efektów specjalnych odbywa się w sposób ręczny, prędkość pracy przenośnika ustawiana jest na ok. 1 m/min. Dla ułatwienia pracy operatorom w kabinach ręcznych zastosowano system zawiesi obrotowych.
Ze względu na potrzebę utrzymania produkcji ram rowerowych w firmie Arkus, inwestycja została podzielona na dwa etapy. W pierwszym etapie zainstalowano część automatyczną na wydzielonej części hali, a następnie po uruchomieniu tej części i przeniesieniu produkcji na tę część zlikwidowano poprzednią lakiernię ręczną i w jej miejsce zainstalowano nową część manualną. Całość inwestycji od podpisania kontraktu do chwili uruchomienia trwała 2 miesiące.