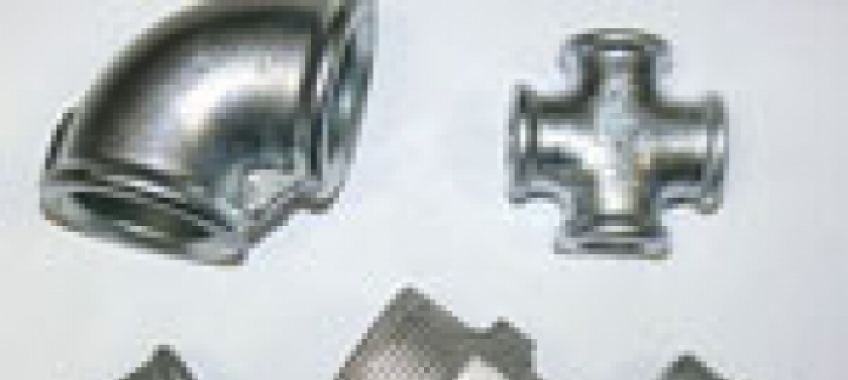
Rys. 1. Model powłok cynkowych wytwarzanych metodą klasyczną i wysokotemperaturową.
Wyroby przeznaczone do cynkowania pokrywa się warstwą topnika przede wszystkim w celu poprawienia zwilżalności podłoża przez ciekły cynk i umożliwienia reakcji na powierzchni wyrobu. Topnik zabezpiecza też oczyszczony wyrób, nie dopuszczając do utlenienia powierzchni, aż do momentu zanurzenia w kąpieli cynkowej. Topnikami są najczęściej roztwory elektrolitów, z których na powierzchni cynkowanego wyrobu wytrącają się jony metalu pokrycia, co ułatwia powstawanie powłoki cynkowej. Stosuje się mieszaninę soli chlorku cynku i chlorku amonu z różnymi dodatkami. Zanurzanie wyrobu w kąpieli odbywa się w temperaturze 530-560 st. C w czasie zazwyczaj od kilku do kilkunastu minut, zależnie od wielkości cynkowanych elementów. Podstawową różnicą w porównaniu z cynkowaniem w temperaturze 440-450 st. C jest konstrukcja wanny i sposób jej ogrzewania. Stosowane są wanny ceramiczne, a ponieważ tego typu materiały charakteryzują się niskim współczynnikiem przewodnictwa cieplnego, są ograniczone możliwości ogrzewania kąpieli przez ściany wanny za pomocą palników gazowych. Wykorzystuje się w tym celu inne metody o mniejszej sprawności. Trzecim etapem procesu technologicznego jest kontrola jakości otrzymanych powłok. Dotyczy ona przede wszystkim wyglądu zewnętrznego powłoki oraz jej grubości. Powłoka cynkowa musi odpowiadać warunkom technicznym podanym w normie PN-EN ISO 1461. Średnia grubość powłoki na wyrobach cynkowanych metodą indywidualnego zanurzania powinna wynosić od 45 do 85 m i zależy od gabarytów pokrywanych elementów. Powłoka nie może wykazywać wad lokalnych, zgrubień oraz miejsc nie pokrytych cynkiem. Suma obszarów bez powłoki nie może przekroczyć 0,5 proc. łącznej powierzchni elementu. Pojedynczy obszar bez powłoki nie może przekroczyć 10 cm2. Nie pokryte miejsca powodują lokalne obniżenie odporności na korozję, więc powinny być usunięte w sposób zapewniający odpowiednią jakość pokrycia [8]. W praktyce do naprawy wad stosuje się lakiery z wysoką zawartością proszku cynku.
Zastosowanie przemysłowe
Cynkowanie wysokotemperaturowe, przy podobnej odporności korozyjnej jak w przypadku klasycznego cynkowania, pozwala na wytwarzanie powłok cieńszych o nawet 60 proc. Zastosowanie wyższej temperatury kąpieli pozwala wyeliminować wpływ dodatków stopowych występujących w stali na wzrost powłoki, jak również ułatwia cynkowanie wysokowęglowych, głównie odlewniczych stopów żelaza. Można również ograniczyć niekorzystny wzrost powłoki spowodowany oddziaływaniem krzemu w stalach reaktywnych. W temperaturze 540 st. C grubość powłoki otrzymanej na stalach sandelinowskich, jak i wysokokrzemowych jest zbliżona do grubości powłoki otrzymanej na stali o niskiej zawartości krzemu (poniżej 0,03 proc.). Technologia ta doskonale nadaje się do zabezpieczania powierzchni elementów żeliwnych armatury przemysłowej oraz drobnych wyrobów stalowych, takich jak: śruby, nakrętki czy odkuwki. Wśród odlewniczych stopów żelaza cynkowaniu praktycznie poddawano najczęściej wyroby z żeliwa ciągliwego, które obecnie coraz częściej, ze względu na energochłonność procesu wytwarzania, jest zastępowane żeliwem sferoidalnym. Rys. 3 przedstawia przykłady wyrobów pokrywanych wysokotemperaturowymi powłokami cynkowymi. Powłoki wytworzone w procesie HT-HDG składające się jedynie z warstwy faz międzymetalicznych (warstwy dyfuzyjnej) mają mniejszy metaliczny połysk w porównaniu z powłokami cynkowanymi tradycyjnie. Jeżeli jednak po wyciągnięciu z kąpieli wyroby nie są odwirowane i chłodzone są w wodzie, na powierzchni wyrobów uzyskiwana jest, oprócz warstwy dyfuzyjnej, również warstwa cynku. W takim przypadku występuje klasyczny metaliczny połysk wymagany czasami przez odbiorców. Dodatkowo istnieje możliwość powlekania wyrobów lakierami pozwalającymi na przedłużenie trwałości zabezpieczenia oraz podniesienia walorów estetycznych powierzchni.