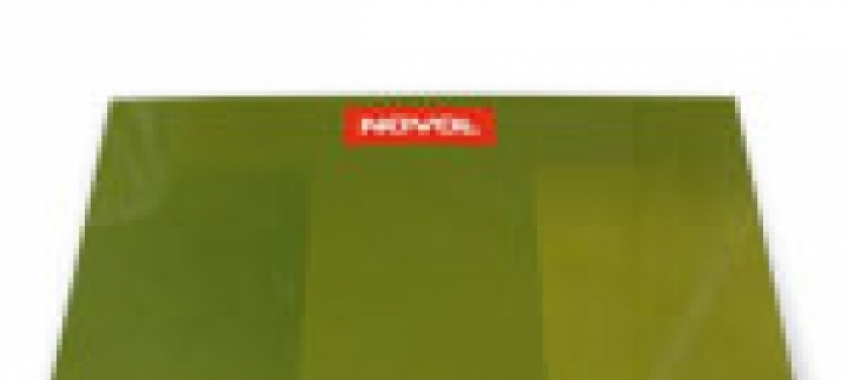
1. Właściwości izolacyjnych żywicy i jej ilości w podkładzie
2. Ilości i jakości pigmentów antykorozyjnych
3. Grubości warstwy.
Rys. 2. Średnia średnica ziaren dk50 dla różnych gradacji papieru.
W praktyce do zastosowań przemysłowych najczęściej mamy do wyboru podkłady na bazie żywic epoksydowych, poliuretanowych, akrylowych, poliwinylowych lub alkidowych. Najlepszą ochroną ze względu na bardzo dobre właściwości barierowe i silne usieciowanie (ochrona przed penetracją wilgoci) uzyskujemy dla podkładów na bazie żywicy epoksydowej. Dobrze wypadają podkłady akrylowe
i poliuretanowe o wysokim stopniu usieciowania, zaś najsłabiej wypadają 1-komponetowe żywice alkidowe, w których utwardzenie polega na odparowaniu rozcieńczalnika przy znikomym sieciowaniu. Ilości i jakości pigmentów antykorozyjnych w podkładzie nie można ocenić „gołym okiem”, dopiero badania w komorze solnej (standardowo 35ºC, 5% roztwór wodny soli) pozwalają ocenić czy podkład je zawiera, czy nie. Bardziej drastycznym dowodem ich braku są ślady korozji pojawiające się np. po roku od wymalowania.
Rys. 3. Różnice w kolorze w kolorze farby nawierzchniowej w zależności od koloru podkładu.
Grubość warstwy podkładu jest już parametrem mierzalnym. Można oceniać zarówno grubość warstwy mokrej, jak i warstwy suchej. Dolną granicę, przy której możemy mówić o odporności antykorozyjnej to min. 50 µm, przy takiej grubości podkład epoksydowy, akrylowy powinny wytrzymać w komorze solnej powyżej 450 h. Przy wymalowaniach przemysłowych (autobusy, tramwaje, cysterny) przy krótkim okresie ochrony (2-5 lat) i umiarkowanym obciążeniu antykorozyjnym (kategoria C3) zaleca się, żeby grubość warstwy podkładu wynosiła min. 70-100 µm suchej warstwy. Całkowita grubość powłoki lakierniczej dla takich zastosowań (podkład z warstwą wierzchnią) to przedział min. 120-150 µm. Nie bez powodu pierwsze oznaki korozji pojawiają się na krawędziach elementów. Wynika to z procesu technologicznego, jeżeli krawędź nie została właściwie odtłuszczona, lakiernik nie położył wystarczająco grubej warstwy lub przeszlifował podkład wypełniający do czystej blachy, a potem położył warstwę wierzchnią na „goły metal” korozja gwarantowana. Warstwa wierzchnia (np. farba akrylowa) nie chroni w 100% przed penetracją wilgoci i w miejscach, gdzie woda długo zostaje na powierzchni (listwy, załamania, zakamarki) korozja rozpoczyna się najszybciej. Nic więc dziwnego, że nawet na minibusie (renomowanej zresztą firmy), na którym całkowita grubość pokrycia wynosiła od 65 do maks. 90 µm, po 1,5 roku widać już ogniska korozji.