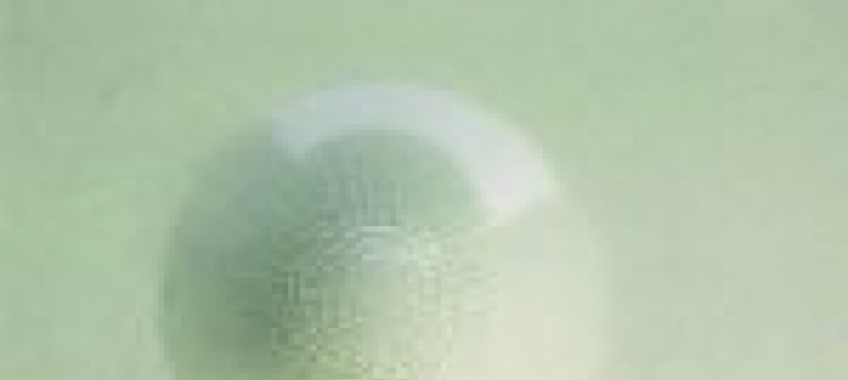
Żółknięcie
Kolejnym defektem powłok proszkowych jest żółknięcie. Jest ono spowodowane bezpośrednim działaniem gazów piecowych (głównie tlenków azotu), zbyt długim przebywaniem w piecu w stosunku do zalecanego czasu lub też zbyt wysoką temperaturą w stosunku do zalecanej oraz zastosowanie nieodpowiedniej farby (brak odporności na warunki atmosferyczne bądź temperaturowe). Używanie farby odpowiednio przygotowanej dla pieców gazowych o bezpośrednim działaniu gazów piecowych zdecydowanie zapobiega żółknięciu farby. Tak samo ważne jest przestrzeganie reżimów temperatury i czasu zalecanych przez producenta jako odpowiednie do utwardzenia powłoki danej farby. Inną ważną rzeczą jest nieużywanie systemów epoksydowych i hybrydowych do malowania detali narażonych na działanie czynników atmosferycznych i promieni słonecznych.
Różnice w połysku
Odkąd potrafimy sterować połyskiem powłok, zwracamy szczególną uwagę, aby tenże był jednakowy na całej powierzchni oraz taki, jaki sobie życzymy. Dlatego wszelkie różnice w połysku zwracają naszą uwagę. Taki defekt powłoki może być spowodowany poprzez różnego rodzaju zanieczyszczenia (zazwyczaj biały lub szary nalot, mogący się pojawiać w szczególnych warunkach jako pochodna użytych wosków bądź żywic). Innymi przyczynami różnic w połysku mogą być niedostateczne utwardzenie farby, skórka pomarańczy, niekompatybilność z innym proszkiem, różnice w grubościach oraz niedostateczna rozlewność farby spowodowana złym przechowywaniem (zbyt wysoka temperatura lub zbyt długi czas). Aby uniknąć niechcianych różnic w połysku, należy dokładnie stosować się do zaleceń producenta dotyczących składowania i transportu proszku oraz czasu i temperatury jego utwardzania. Ważna jest też stabilność i powtarzalność warunków procesu technologicznego oraz informowanie producenta o wszystkich wymaganiach dotyczących jakości i wyglądu powłoki.
Niewłaściwa adhezja
Słabe właściwości mechaniczne i chemiczne oraz niewystarczająca adhezja powłoki do detalu są defektami trudnymi do zauważenia zaraz po wykonaniu powłoki. Jednak przyczyny ich powstawania są podobne dla obu tych przypadków. Głównym powodem tych defektów są bądź nieodpowiednie przygotowanie powłoki pod malowanie, poprzez zanieczyszczoną powierzchnię (silikony, oleje, tłuszcze, woski, rdza, pozostałości po szlifowaniu), bądź nieodpowiedni lub niewystarczający podkład lub powłoka konwersyjna (przygotowanie powierzchni). Innym powodem złych właściwości odpornościowych powłoki oraz słabej adhezji są złe przygotowanie kąpieli czyszcząco-myjącej lub złe warunki sieciowania proszku. W celu pozbycia się zmartwień dotyczących złej adhezji oraz właściwości powłoki musimy dbać, by używana przez nas technologia była „czysta” podczas całego procesu. Przede wszystkim dużą uwagę należy zwrócić na przygotowywanie kąpieli myjących oraz używanie do mycia naprawdę czystej wody. Dobrze jest też badać czystość używanej wody poprzez badanie przewodności (powinna być poniżej 30 mS). Używane przez nas podkłady lub powłoki konwersyjne powinny być dobrze dobrane i prawidłowo przygotowane, zgodnie z zaleceniami producentów. Zbyt duża grubość farby, nieodpowiednie warunki utwardzania proszku (zbyt szybkie nagrzewanie, zbyt duży detal i temperatura pieca) oraz zbyt niska lepkość farby po stopieniu mogą być przyczynami ściekania farby z detalu i tworzenia tzw. sopli.