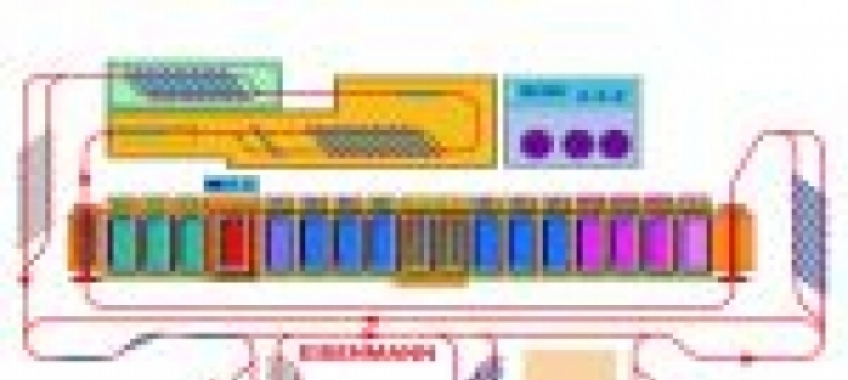
Zastosowany system transportowy oparty na zawieszkach, oprócz kompaktowej budowy systemu, co jest niewątpliwie jego zaletą, nadaje się również do transportu ciężkich elementów o wadze do 500 kg. Strefa buforowa, sortownik i funkcja rozdziału elementów są zarządzane przez łatwą w obsłudze technikę sterowania transportem. Nowa linia została powiązana poprzez system Power&Free z robotami spawalniczymi i linią montażową. W stacjach załadowczych elementy są zawieszane na system transportowy i kierowane do lakierni. Cały cykl lakierowania zanurzeniowego w taktowym trybie pracy odbywa się w sposób automatyczny, tylko przy załadunku i rozładunku potrzebny jest jeszcze udział pracowników. Są konieczni, ponieważ elementy i podzespoły do polakierowania różnią się tak bardzo miedzy sobą pod względem wyglądu, geometrii, wymiarów i wagi, że zaleca się ręczny załadunek i rozładunek zawieszek systemu Power&Free. Z tych powodów rozwiązanie manualne okazało się ekonomiczniejsze. Przy transporcie elementów bardziej ujednoliconych i o większych seriach produkcyjnych, jak np. przy produkcji felg samochodowych, załadunek elementów do lakierowania do 95 sztuk na jednej zawieszce systemu Power&Free został zlecony robotom z ramieniem przegubowym. Różnorodność produkowanych elementów zmusiła ponadto konstruktora urządzenia do opracowania specjalnych transporterów, które pozwalają na dowolne i elastyczne rozplanowanie umieszczenia wyrobów. Długie na 300 cm, szerokie na 60 oraz wysokie na 150 cm transportery mogą przemieszczać podzespoły bardzo zróżnicowane pod względem formy, jak: osie, podłużnice oraz całe ramy samochodowe.
<42-210_Witte_P+F5Ret.jpg>
Fot. 2. Ekonomiczne rozmieszczenia elementów na zawieszkach
Fot. 3. W stacji przekazywania: elementy metalowe wędrują z przenośnika Power&Free do automatów załadowczych
Przy załadunku pracownik obsługujący zadaje dla każdego losowo następującego po sobie wymiaru odpowiedni program. Dzięki tej informacji system sterujący może jednoznacznie rozpoznać, zlokalizować i śledzić element w trakcie dalszej produkcji.
Pracownik wybiera pomiędzy różnymi stacjami odbioru i grubościami powłoki lakierniczej. Są to parametry, które są w sposób automatyczny dobierane dla strefy przygotowania powierzchni i kataforezy. Gdy na automacie załadunkowym pojawia się nowy transporter, jednostka skanująca odczytuje jego dane i przekazuje je między innymi do prostownika napięcia, który posyła odpowiednie napięcie do wanny KTL, stosownie do zadanego programu lakierniczego. W ten sposób elementy w każdym transporterze otrzymują wcześniej zadaną grubość powłoki lakierniczej. W obszarze KTL czas jednego taktu wynosi 6 minut, transport na odcinku Power&Free dokonuje się jednak w rytmie 3-minutowym. Aby wyrównać tę różnicę, transportery posyłane są parami do wanien przygotowania powierzchni i KTL. Tzw. pamięć sterowania przepływu pilnuje tego procesu w ten sposób, aby zawsze zawieszki z tym samym rodzajem towaru i programem lakierniczym były posyłane parami. Tylko wtedy, gdy pracownicy bezpośrednio po sobie załadują dwa, cztery, sześć itd. zestawów transporterów identycznymi elementami, bezpośrednim celem zestawu jest magazyn elementów surowych. Jeżeli obsługa lakierni załaduje tylko pojedyncze transportery elementami, to Power & Free kieruje taki transporter do osobnego magazynku. Będzie on oczekiwał na „symetryczny” transporter, załadowany takimi samymi elementami. Dopiero wówczas ruszy program lakierniczy, gdy będzie para transporterów. Długi na 60 metrów magazynek dla takich elementów wynika z szczególnego sposobu prowadzenia łańcucha. Pozwala on na wygodny objazd wanien zanurzeniowych, wtedy gdy ekipy serwisowe prowadzą prace remontowo-konserwacyjne. Drugim ważnym zadaniem objazdu KTL jest sortowanie i łączenie w pary transporterów.