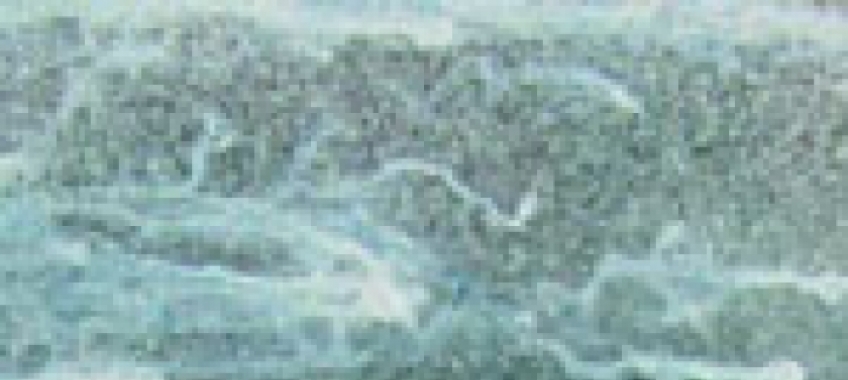
W tabeli 1 przedstawiono porównanie odporności korozyjnej powłok duplex o stałej grubości podpowłoki cynkowej (ok. 80 μm), w zależności od rodzaju zastosowanego materiału organicznego warstwy zewnętrznej oraz warunków użytkowania. W zestawieniu występują również farby chlorokauczukowe oraz alkidowe, które obecnie nie są zalecane. Produkty degradacji wyrobów chlorokauczukowych mogą niszczyć powierzchnie powłoki cynkowej, zaś farby alkidowe reagując z cynkiem zmydlają się, co zmniejsza przyleganie warstwy do podłoża cynkowego podczas nanoszenia. W środowisku korozyjnym wszystkie przedstawione grupy farb posiadają doskonałą trwałość. Jedynie pokrycia wytwarzane na bazie żywic alkidowych i akrylowych mają nieznacznie gorszą odporność korozyjną. Zauważalne są również gorsze właściwości korozyjne emulsji wodnych w porównaniu z farbami na bazie rozpuszczalników organicznych.
Rys.2. Wygląd powierzchni powłoki B po badaniu korozyjnym przyspieszonym w obojętnej mgle solnej, odpowiednio po 360 i 500 godzinach trwania testu. [9]
Wszystkie przedstawione systemy duplex zapewniają długi czas ochrony w środowiskach agresywnych, takich jak atmosfera przemysłowa czy morska. W obecności kwasów gorszą odporność korozyjną wykazują farby na bazie żywic alkidowych oraz akrylowych, natomiast większość tworzyw: epoksydowych, winylowych i poliuretanowych wykazuje bardzo dobrą trwałość. Nieco gorzej wygląda odporność korozyjna powłok duplex w obecności związków alkalicznych. W przypadku stosowania farb alkidowych i akrylowych jako warstwy zewnętrznej ma ona niewystarczające właściwości antykorozyjne, co skutkuje przyspieszoną degradacją pokrycia. Mniejsza trwałość powłok duplex w środowisku zasadowym może być również wynikiem znanego zjawiska przyspieszonej korozji elektrochemicznej cynku w środowisku
o charakterze zasadowym pH > 12,5.Rys. 3. Wygląd powierzchni powłoki cynkowej po 72 godzinach trwania testu korozyjnego w obojętnej mgle solnej.
Badania odporności korozyjnej powłok duplex w warunkach laboratoryjnych
Do określenia właściwości antykorozyjnych metalicznych i niemetalicznych powłok ochronnych wykonuje się najbardziej reprezentatywne badania długotrwałe, prowadzone w naturalnej atmosferze korozyjnej, w warunkach użytkowania czy magazynowania, a także badania elektrochemiczne (potencjostatyczne i potencjodynamiczne) oraz badania przyspieszone w warunkach laboratoryjnych. Ostatnia grupa badań jest przydatna ze względu na możliwość porównawczej oceny odporności korozyjnej materiałów w stosunkowo krótkim czasie. Szczególnie trudne warunki korozyjne (wilgotność względna na poziomie prawie 100%, odpowiednia temperatura oraz oddziaływanie różnych związków chemicznych i par ich roztworów np. NaCl, SO2) są wytwarzane w komorze w sposób syntetyczny. Dodatkowo w przypadku powłok lakierniczych do przyspieszenia degradacji pokrycia używane są lampy promieniowania ultrafioletowego. Badania te mają ponadto charakter badań rozjemczych.