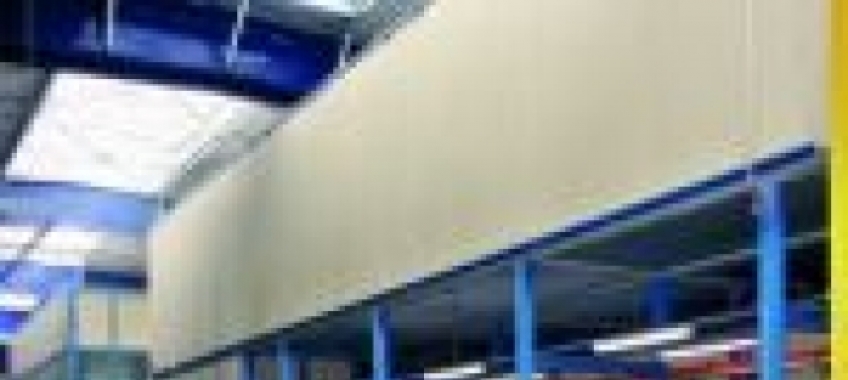
Zwiedzając Fabrykę Lodówek w spółce Amica Wronki SA można się wyzbyć kompleksów na temat opłakanego stanu polskiej gospodarki i produkcji. Powstały w 1996 roku, nowoczesny zakład produkcyjny spółki, czwarty po Fabryce Kuchni, Armatury i Pralek, z w pełni zautomatyzowaną linią przygotowania powierzchni i malowania proszkowego, dzisiaj jest perłą rozwoju technologicznego wśród europejskich producentów AGD.
W lutym bieżącego roku w Fabryce Lodówek spółki ruszyła nanoceramika, bezfosforanowa technologia przygotowania powierzchni. – Przechodziliśmy na nową technologię ze względu na ekologię i zmieniające się wymagania jakościowe powierzchni w malowaniu proszkowym – mówi Zbigniew Mikołajczak, główny emaliernik Amiki. – Lodówki to produkt, który pracuje w trudnych warunkach korozyjnych (skraplanie się wody), więc zależało nam na podniesieniu odporności korozyjnej produktu do min. 600 godzin w teście komory solnej dla detali wykonanych z różnych metali.
Elementy lodówek po nałożeniu nanoceramiki
Przed wdrożeniem nanoceramiki przygotowanie powierzchni na chemii dostarczanej przez Henkla składało się z odtłuszczania alkalicznego, płukania, fosforanowania, płukania, pasywacji cyrkonowej (Amica nigdy nie stosowała pasywacji chromowej ze względu na ekologię) i płukania wodą demi. – Zmieniliśmy technologię przygotowania powierzchni na tej samej linii, nie zmieniając jej gabarytów. Wybraliśmy technologię, w której fosforanowanie i pasywacja zostały zastąpione jedną operacją – nanoceramiką, uzyskując jednocześnie podwyższenie odporności korozyjnej”.
Postawili na jakość i ekologię
Od początku swojego istnienia Amica musiała opowiedzieć się po stronie ekologii. Zakład został zbudowany w szczerym polu, daleko od centrum i komunalnej oczyszczalni ścieków. Ta naturalna bariera wymagała rozwiązania problemu ścieków na terenie samego zakładu. Zainwestowano więc w najnowszą, pewnie do dzisiaj jedyną w kraju, oczyszczalnię ścieków z tzw. technologią wyparkową (po destylacji czysta woda zawracana jest do procesów oczyszczania powierzchni i żadne ścieki nie są odprowadzane z zakładu na zewnątrz). Produktem odpadowym oczyszczalni wyparkowej jest osad pakowany w zgrzewane worki foliowe i odbierany przez specjalistyczne firmy utylizacyjne.
Od lewej: Zbigniew Mikołajczak, główny emaliernik Amiki oraz Romuald Nowak z firmy Henkel
– Wybraliśmy najlepsze rozwiązanie dla środowiska i dla nas. Zyskaliśmy oszczędność wody (co ma coraz większe znaczenie szczególnie w Wielkopolsce, gdzie od lat odczuwalny jest jej coraz większy deficyt), ale i poczucie bezpieczeństwa – wyjaśnia Zbigniew Mikołajczak. – Inne zakłady stoją przed koniecznością modernizacji procesów przygotowania powierzchni w najbliższym czasie, w związku z unijnymi wymaganiami dotyczącymi dopuszczalnych ładunków zanieczyszczeń w ściekach oraz tzw. ChZT-ów. Stosując w przygotowaniu powierzchni detergenty i kąpiele alkaliczne staną wobec nowych problemów...