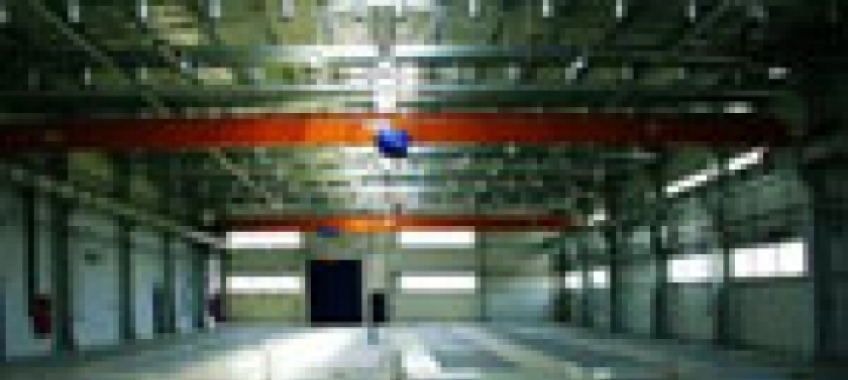
Znaczące zmiany w materiałach aplikacyjnych wymusiły oczywiście zmiany w technologii ich nakładania. Główna zmiana dotyczy wyeliminowania nakładania farb metodą natrysku pneumatycznego na rzecz natrysku hydrodynamicznego. W efekcie wielokrotnie zwiększono wydajność malowania i znacznie zmniejszono ilość odpadów, głównie w postaci rozpuszczalników wyrzucanych do atmosfery.
W najbliższej przyszłości natomiast należy spodziewać się powszechnego wykorzystania techniki malowania hydrodynamicznego z zastosowaniem maszyn do malowania farbami dwuskładnikowymi. Podstawowa różnica między typowymi maszynami malarskimi a dwuskładnikowymi typu 2K sprowadza się do sposobu mieszania składników farb. W pierwszym przypadku składniki farby miesza się przed rozpoczęciem, a w drugim w trakcie malowania. W maszynie typu 2K składniki farby są pobierane przez niezależne pompy, z których pod ciśnieniem trafiają do urządzenia mieszającego i na koniec do pistoletu natryskowego. W ten sposób mieszanie składników odbywa się bezpośrednio przed malowaniem. Sieciowanie farby odbywa się natomiast dopiero po jej naniesieniu na malowaną powierzchnię. Pozwala to na utrzymanie odpowiedniej lepkości farby, a zatem na prawidłowy natrysk i formowanie się powłoki. Obecnie produkuje się bardzo szeroką gamę maszyn do nakładania farb dwuskładnikowych. Najogólniej dzieli się je na maszyny ze stałym lub ze zmiennym stosunkiem mieszania. W pierwszym przypadku maszyna jest zwykle zbudowana z jednego silnika pneumatycznego poruszającego równocześnie zestawem trzech pomp materiałowych. Jedna, środkowa pompa, zasysa jeden ze składników, a dwie pozostałe drugi. Zamontowany zestaw pomp materiałowych jest tak dobrany, aby zachowane były proporcje pomiędzy składnikami farb. Maszyny o zmiennym stosunku mieszania dzielą się na takie, w których zmiany dokonywane są w sposób mechaniczny lub elektroniczny.
Hala do malowania wyrobów wielkogabarytowych w systemie gniazdowym.
W pierwszym przypadku maszyna składa się z silnika pneumatycznego, który za pomocą specjalnej dźwigni porusza dwiema pompami materiałowymi. Proporcje pomiędzy składnikami farby zmienia się poprzez zmianę położenia dźwigni, co wywołuje zmianę skoku pomp, a tym samym zmianę ich wydajności. Maszyny z elektronicznym systemem zmiany proporcji są najbardziej rozbudowane. Zwykle składają się one z dwóch niezależnych pomp, których wydajnością steruje mikroprocesor. Z opisanych powyżej pomp w wytwórniach konstrukcji stalowych najczęściej stosowane są pompy ze stałym stosunkiem mieszania. Są one najprostsze w budowie, a zatem najtańsze. Potrzeba produkcji maszyn do farb dwuskładnikowych pojawiła się z chwilą rozpoczęcia produkcji farb, których czas żelowania po zmieszaniu składników był za krótki, aby można je było nakładać tradycyjnymi metodami. Powstawały farby, szczególnie poliuretanowe, których składniki należało mieszać bezpośrednio przed natryskiem. Obecnie maszyny typu 2K zdobywają coraz większą popularność również w przypadku zużywania dużych ilości farb dwuskładnikowych jednego rodzaju, nawet jeśli czas żelowania takiej farby jest wystarczająco długi, aby ją nakładać zwykłą maszyną. Ciągłe i masowe zużywanie dużych ilości farb wymaga zaangażowania dużej liczby personelu do jej ważenia, mieszania i przelewania. Zastosowanie pomp 2K umożliwia pełną automatyzację procesu mieszania. Znika potrzeba ważenia, mieszania i przelewania, co eliminuje niebezpieczeństwo pomyłki (zmieszania składników w złych proporcjach) i znacznie ogranicza ilość odpadów. Ogromną zaletą stosowania maszyn typu 2K jest również możliwość dostarczania farb w dużych zwrotnych pojemnikach. Przy zużywaniu dużych ilości farb ma to fundamentalne znaczenie. Znaczący postęp notuje się także w wyposażeniu malarni. Tutaj główne działania zmierzają do dostosowania systemów wentylacji do rosnących wymagań ochrony środowiska. Rozporządzenie Ministra Ochrony Środowiska (z dnia 29.12.2005 r.) narzuca firmom normy jakim musi odpowiadać brudne powietrze wydalane z malarni do atmosfery - dopuszczalne stężenia rozpuszczalników są ściśle określone. Większość firm dostosowuje się do wymagań rozporządzenia, instalując systemy wentylacji o takiej wydajności, aby stężenie rozpuszczalników w wydalanym powietrzu nie przekraczało norm. Na razie nieliczne zakłady, głównie położone w rejonach, w których lokalne władze narzucają ostrzejsze wymagania, instalują urządzenia do prawie całkowitego eliminowania rozpuszczalników z wyrzucanego powietrza. Rozpuszczalniki z powietrza usuwa się obecnie głównie poprzez spalanie lub adsorpcję. Najprostszym urządzeniem jest adsorber węglowy. Zwykle ma on postać prostej kolumny adsorpcyjnej wypełnionej węglem aktywnym. Zaletą takiego rozwiązania jest niski koszt inwestycji, wadą natomiast wysoki koszt eksploatacji. Złoże węgla aktywnego ulega szybkiemu zapełnieniu rozpuszczalnikiem i wymaga częstej wymiany. Natomiast do spalania rozpuszczalników stosuje się katalityczne dopalacze. Są to urządzenia drogie. Z tego powodu rzadko stosuje się je do oczyszczania dużych ilości powietrza. Są one również kosztowne w eksploatacji, szczególnie jeśli w powietrzu znajduje się niewielka ilość rozpuszczalników. Połączeniem zalet obu metod, spalania i adsorpcji, jest metoda adsorpcyjno-katalityczna. W tej metodzie całe powietrze jest przepuszczane przez kolumnę adsorpcyjną. Po jej napełnieniu rozpuszczalnik desorbuje się małą ilością gorącego powietrza i kieruje na niewielki katalityczny dopalacz. W ten sposób unika się kosztownej i częstej wymiany węgla aktywnego. Również mały dopalacz jest znacznie tańszy zarówno przy zakupie, jak i podczas eksploatacji. Ze względu na wysokie i stale rosnące koszty ogrzewania malarnie uzbraja się w urządzenia do odzysku ciepła z powietrza wyrzucanego do atmosfery. Wyposażenie tego typu zwykle zapewnia oszczędność energii powyżej 50%. W Polsce montaż takich urządzeń jest nakazany Rozporządzeniem Ministra Infrastruktury (z dnia 15.06.2002 r.) w przypadku, gdy wydajność wentylacji jest większa niż 10 000 m3 na godzinę. Mimo to większość starych i dużo nowo budowanych malarni nie posiada jeszcze wyposażenia tego typu.