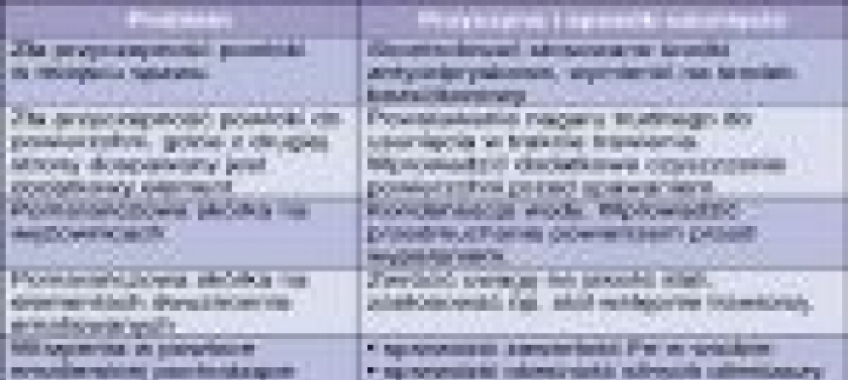
Tablica 1
II etap – emaliowanie oczyszczonych zbiorników odbywa się na maszynach emalierskich poprzez napełnienie wnętrza zbiorników masą emalierską i równomierne jej rozłożenie na powierzchni w trakcie “wykręcania”. Stosowana emalia przygotowywana jest z komponentów poprzez mielenie z wodą w młynach kulowych do uzyskania odpowiedniego stopnia zmielenia (w naszym przypadku o parametrze granulacji 14-16°Bayera – sitko 160 oczek). W trakcie emaliowania konieczna jest bieżąca kontrola parametrów emalii: ciężar płyty 800-1100g/m2, gęstość właściwa 1,87-1,95 kg/m3.
III etap – suszenie emalii Naniesiona warstwa emalii przed wypaleniem poddana zostaje procesowi suszenia w temperaturze do 50°C. Ważne jest, aby wysuszenie przeprowadzone zostało bardzo dokładnie.
IV etap – czyszczenie zbiorników Przed wypaleniem należy usunąć emalię z wszystkich niezbędnych miejsc, np. gwintów, za pomocą drucianych szczotek itp.V etap – wypalanie prowadzone jest w piecu w temperaturze 860°C przez ok. 10 minut przy szybkości przesuwu v= ok. 0,7m/min
VI etap – kontroli wizualnej powłoki emalierskiej poddawane jest 100% wyrobów. Dodatkowo, wyrywkowo sprawdzana jest jej grubość oraz przeprowadzana próba na prąd ochronny wg normy DIN 4753 część 3. Dla emalii bezpośredniej wartość prądu ochronnego powinna wynosić ≤ 22,5 mA/m2.
Powłoki lakiernicze na obudowach bojlerów
Aby uzyskać dobrej jakości powłoki ochronne i jednocześnie ozdobne na obudowie (osłonie) bojlera do wody gorącej do niedawna stosowano farby cieczowe, obecnie przechodzi się na technologie proszkowe. Szczególnie ważne jest zachowanie szczelności i trwałości powłoki na zewnątrz np. obudowy cylindrycznej. W masowej produkcji proces lakierniczy zwykle jest oparty na technologii elektrostatycznej. Linia lakiernicza cieczowa niezawodnie pracuje ponad 30 lat (w firmie NIBE-BIAWAR). Dla uzyskania dobrej faktury powłoki, jednolitości barwy, braku defektów w powłoce należy zachować kilka wymagań. Są to: dobre mieszanie farby z dodatkami, przygotowanie warstwy fosforanowej na stali, eliminowanie ostrz na obrzeżach, zachowanie wyjątkowej czystości w strefie malowania i komorze suszarniczej, stosowanie się do zaleceń co do parametrów elektrofizycznych pracy generatorów w.n., używanej farby, temperatury i czasu utwardzania itd. Z uwagi na zagrożenia wybuchowe od iskier w kabinach nie należy dopuszczać do pojawienia się tzw. efektu “suszenia” aerozolu w polu K [kV/cm] oraz rozseparowania składników w tej strefie silnego pola (tuż przy ostrzach tzw. atomizerów w.n.). Szczególnie rygorystycznie należy dopilnować, by w procesie atomizacji strugi farby była utrzymana optymalna lepkość cieczy i napięcie U. Obniżka napięcia U na ogół wynika ze zbyt dużego obciążenia prądowego generatorów w.n. Ten efekt pochodzi zwykle od zbyt niskiej wartości rezystywności farby r [W * m]. Ta wartość powinna leżeć w granicach 5x106 – 5x107 W x cm.