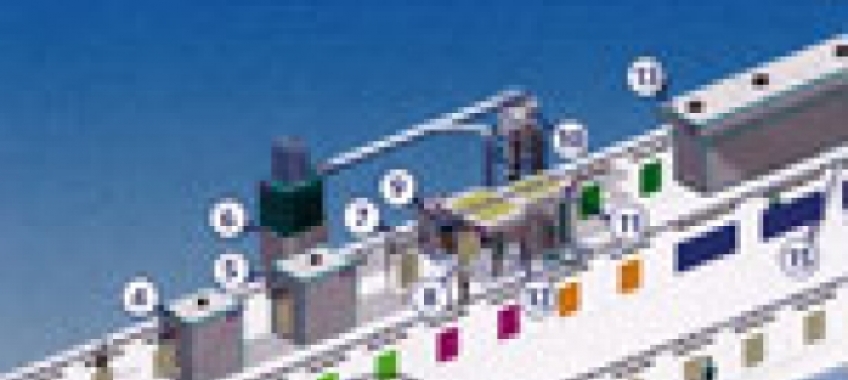
Strefa załadowczo-rozładowcza: Pierwszym krokiem w procesie produkcji jest zawieszanie elementów na trawersach. Przy dużych ilościach, jest możliwość zautomatyzowania tego etapu. Prędkość przenośnika wynosi ok. 3 m/min, może być ona jednak dostosowana do sugestii i wymogów klienta. Przy większych prędkościach przenośnika wydłużana jest jednocześnie strefa wygrzewania w piecu.
Stacja szlifowania i odpylania (opcjonalnie): Tutaj elementy mogą zostać odkurzone oraz ponownie przeszlifowane.
Strefa buforowa: Jej wielkość zależy od rodzaju powlekania, wielkości elementów, liczby sztuk oraz ilości zmian koloru.
Stacja czyszczenia automatycznego (opcjonalnie): Elementy mogą być tutaj ponownie automatycznie oczyszczone (odpylone).
Piec do wygrzewania wstępnego: Tutaj elementy są wstępnie kondycjonowane przed procesem powlekania. Materiał jest podgrzewany powierzchniowo, tak aby przez cały czas utrzymywać stałą temperaturę powierzchni. Jednocześnie poprawia się (zwiększa) przy tym przewodność materiału.
Rozpoznawanie elementów: System steruje pistoletami oraz uruchamia odpowiedni program powlekania i suszenia.
Miejsce lakierowania wstępnego: Tutaj elementy o skomplikowanej geometrii są wstępnie lakierowane. Powlekane mogą być też detale, próbki lub elementy wymagające poprawek. Jest tu miejsce dla dwóch pracowników. Strefa ta jest przez cały czas utrzymywana w czystości poprzez odsysanie podłogowe, co ma zapobiec rozprzestrzenianiu się farby.
Centrum proszkowe ("kuchnia"): Kuchnia proszkowa wyposażona jest w następujące urządzenia: stół wibracyjny z wagą, pompę dozującą świeży proszek, sito ultradźwiękowe, zasobnik na proszek, odkurzacz, ekran dotykowy oraz szafę sterowniczą do kontroli całej instalacji. Z szafy sterowniczej mogą być zasilane maksymalnie 24 pistolety.
Strefa automatyczna: Dzięki krótkiej strefie automatycznej czas czyszczenia kabiny skraca się niemal o połowę. Podczas czyszczenia otwiera się pokrywa wyciągu a zamykają tylne drzwi kabiny. W ten sposób strefa automatyczna bez trudu oczyszcza się od przodu. Kabina w tym czasie pozostaje pusta. Czas czyszczenia przy tym systemie kabin wynosi ok. 6-12 min.
Czynna przeciwelektroda (odbierająca nadmiar ładunku): Zapewnia ona równomierną grubość powłoki zarówno na powierzchniach płaskich, jak i na krawędziach. W ten sposób wykluczony jest efekt ramy obrazu, a także możliwe jest lakierowanie ostrych krawędzi oraz bardzo skomplikowanych konturów. Dzięki temu możliwe jest również bezproblemowe lakierowanie mniejszych elementów zawieszonych jeden pod drugim. W ten sposób można optymalnie wykorzystać obłożenie trawersy i zwiększyć przepustowość linii.