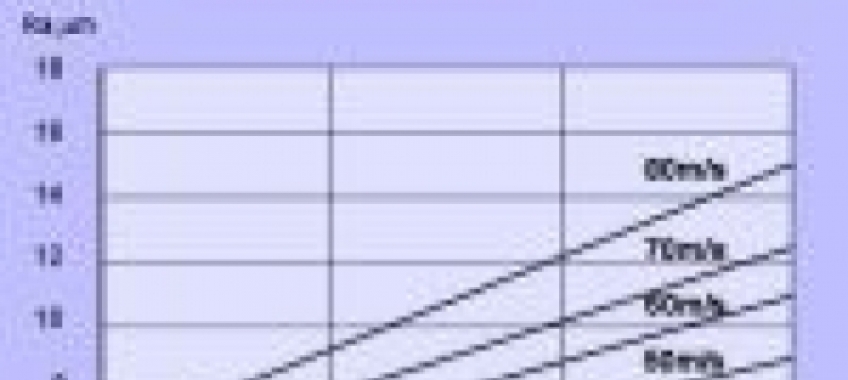
Śrut stalowy cięty z blachy
Śrut ten wykonywany jest z reguły z blachy niskowęglowej o wytrzymałości na rozciąganie 600÷1000 MPa. Twardość śrutu wynosi od 180 do 280 HV. Śrut ten cechuje się niską skrawalnością oraz niską agresywnością w stosunku do części roboczych wirnika rzutowego.
Zasady doboru śrutu
Dokonując doboru gatunku, rodzaju i granulacji śrutu, należy brać pod uwagę następujące czynniki:
• rodzaj i kształt przedmiotu (w tym - podatność na deformację)
• rodzaj i wielkość zanieczyszczenia przedmiotu
• wymagany stopień czystości powierzchni po oczyszczeniu
• wymaganą chropowatość powierzchni po oczyszczeniu
• wymagany profil chropowatości
• wymaganą wydajność oczyszczania
• wpływ użytego śrutu na koszty oczyszczania.
Najczęściej doboru rodzaju i granulacji śrutu dokonuje się na zasadzie kompromisu (np. wybierając pomiędzy energią śrutu i związaną z nią wydajnością, a chropowatością powierzchni):
Dokonując doboru i rodzaju i granulacji śrutu należy brać pod uwagę również wielkość oczyszczarki.
Rys. 2. Zależność prędkości ziarna śrutu od jego rodzaju i granulacji oraz przebytej drogi
Dokonując wyboru rodzaju i granulacji śrutu należy również pamiętać, że:
• śrut o dobrych własnościach skrawających - decydujących o dużej wydajności i skuteczności oczyszczania - jest jednocześnie bardzo agresywny w stosunku do oczyszczarki (szczególnie do części roboczych wirnika rzutowego)
• śrut o dobrych własnościach skrawających posiada niniejszą trwałość, wyrażoną ilością przejść przez wirnik rzutowy oczyszczarki
• kształt ziarna śrutu decyduje o profilu chropowatości oczyszczonej powierzchni (śrut kulisty powoduje powstawanie czasz, natomiast śrut łamany tworzy powierzchnię o ostrych zębach często podciętych).
Jedną z wielkości charakteryzujących oczyszczarkę jest wielkość zużycia śrutu. Wielkość ta zależy od rodzaju i granulacji śrutu oraz od wielkości i ilości wirników rzutowych. Przykładowe zużycie śrutu przez jeden wirnik rzutowy przestawia tabela 1 (sporządzona dla śrutu staliwnego niskowęglowego kulistego o granulacji 0,8÷1,4 mm).Odpylanie oczyszczarek wirnikowych
Istotnym zagadnieniem dotyczącym procesu oczyszczania wirnikowego strumieniowo-ściernego jest odpylanie odciąganego powietrza. Oczyszczarka wymaga odciągu powietrza z kabiny roboczej oraz z separatora.
Odciąganie powietrza z kabiny roboczej ma za zadanie wytworzenie wewnątrz kabiny odpowiedniego podciśnienia w celu wyeliminowania emisji pyłów na zewnątrz oczyszczarki oraz zapobieganiu osadzaniu się pyłów na powierzchniach oczyszczanych przedmiotów. Separator natomiast dla swojego działania potrzebuje odpowiedniego strumienia powietrza wytwarzanego poprzez jego odciąganie.