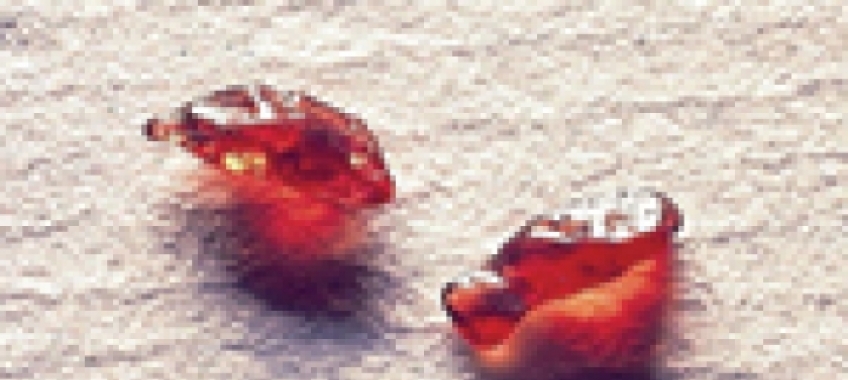
Tablica 1. Ścierniwa powszechnie używane w obróbce strumieniowo–ściernej do przygotowania podłoża stalowego pod powłoki ochronne.
a - Wzorzec do oceny profilu powierzchni wg PN ISO 8503-2.
b - Typ ścierniwa (śruty) zmieniający swój kształt z G i C na S.
1 - Żużel wielkopiecowy - krzemian wapnia
2 - Żużel pomiedziowy - krzemian żelaza
3 - Żużel poniklowy - krzemian żelaza
4 - Żużel paleniskowy - Krzemian glinu
S - Śrut kulisty – okrągły
G - Śrut ostrokątny – ( łamany)
C - Cylindryczny – (częściowo ostrokątny)
Co decyduje o przydatności ścierniwa w obróbce strumieniowo-ściernej
Efekt oczyszczenia i chropowacenia powierzchni zależy w pierwszym rzędzie od:
- rodzaju obrabianego materiału i jego twardości. Ścierniwo musi być twardsze od obrabianego materiału oraz nie może posiadać zanieczyszczeń reagujących z podłożem. Dlatego śrutu staliwnego, stalowego ani żeliwnego, jak też żużli odpadowych nie stosuje się do obróbki stali nierdzewnej i kwasoodpornej, metali lekkich i kolorowych ani ich stopów.
- twardości ziaren ściernych. Twardsze ścierniwa posiadają większą zdolność do chropowacenia powierzchni, co ma bezpośredni wpływ na większą wydajność obróbki powierzchni oraz potrzebują mniejszą ilość ścierniwa na oczyszczenie 1 mkw. powierzchni obrabianej strumieniowo-ściernie. Uwaga ta dotyczy zarówno obróbki powierzchni na sucho, jak i na mokro. Przy obróbce strumieniowo-ściernej na mokro obserwuje się dodatkowy wzrost wydajności oczyszczania i zmniejszenie ilości zużytego ścierniwa dopiero podczas zastosowania ciśnienia wody powyżej 700 barów lub zastosowania silnego wspomagania sprężonym powietrzem, strumienia wody zasysającego suche ścierniwo lub zawiesiny wodnej ścierniwa. Następuje wtedy wyraźny wzrost prędkości wylotu ziaren ściernych opuszczających dyszę czyszczącą. Strumień samej wody pod ciśnieniem około 3000 barów jest najlepszy do usuwania starych powłok z bardzo dużych powierzchni, bo wtedy można zastosować urządzenia z wieloma dyszami a urządzenia te umożliwiają odsysanie zdjętej powłoki i skierowanie jej do filtra (brak zanieczyszczonego ścierniwa). Najczęściej w ścierniwie zanieczyszczonym farbą jest jej około 1-3 proc.- ciężaru właściwego stosowanego ścierniwa. Ma on wpływ w fazie początkowej na czas jego przebywania wewnątrz dyszy, a pośrednio na prędkości ziarna wylatującego z dyszy zgodnie z II prawem Newtona, mówiącym o równości popędu i pędu punktu materialnego. Obserwuje się też pośrednio wpływ długości dyszy i wielkości jej przekroju wewnętrznego oraz kształtu wewnętrznego dyszy (najkorzystniejsze długie dysze Venturiego). Nabyta prędkość ziarna ściernego w dyszy na skutek przejęcia energii od sprężonego powietrza, strumienia wody, mieszaniny wody i powietrza, pary, lub na skutek oddziaływania siły odśrodkowej koła rzutowego, ma największy wpływ na energię ziarna ściernego. Stosunkowo mniejszy wpływ ma natomiast masa samego ziarna. Zagadnienie to jest jednak bardziej skomplikowane, gdyż wpływ ma też kształt oraz objętość ziarna, które wpływają na siłę przeciwstawiania się oporowi powietrza, stawianego strumieniowi ziaren ściernych wylatujących z dyszy lub z koła rzucającego ścierniwo. Dlatego śrutuje się, przy obróbce pneumatycznej, utrzymując długość strumienia ściernego na poziomie 70 cm a używając elektrokorundu ~ 20 cm. 1-1. Prędkość ziarna ściernego opuszczającego długą dyszę typu Venturiego ma wartość do 200 m/s, natomiast śrut opuszczający nawet największy i najszybciej obracający się wirnik nie przekracza 100 m/s.