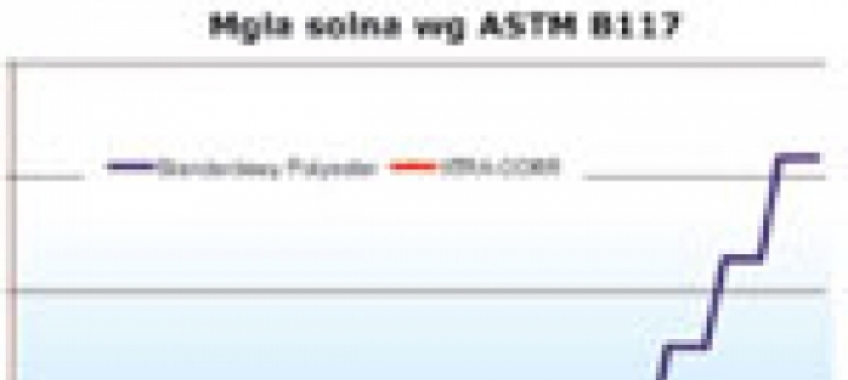
XTRA-CORR™ - nowa klasa odpornych na korozję poliestrowych powłok proszkowych
Korozja podłoży metalowych jest źródłem ogromnych kosztów dla społeczeństwa - nie tylko w ujęciu pieniężnym, ale również z punktu widzenia bezpieczeństwa. Według szacunków organizacji WCO (World Corrosion Organization), światowe koszty korozji wynoszą 1,3–1,4 biliona euro, czyli równowartość 3,1–3,5 proc. rocznego produktu krajowego brutto poszczególnych państw.
Liczby te ilustrują jedynie bezpośrednie koszty korozji, takie jak materiały, urządzenia i robocizna niezbędne do naprawy, konserwacji i wymiany. Nie uwzględniają szkód środowiskowych, marnotrawstwa zasobów, strat produkcyjnych ani obrażeń ciała spowodowanych korozją. Specjaliści zajmujący się korozją oceniają, że 20–25 proc. wspomnianych rocznych kosztów można by zaoszczędzić dzięki stosowaniu dostępnych technik ochrony antykorozyjnej. [1] Tragiczne zawalenie się mostu I-35W w amerykańskim stanie Minnesota w 2007 roku, gdzie zginęło 13 osób, a 145 odniosło rany, mogło być przynajmniej częściowo spowodowane korozją i niewłaściwą konserwacją. Członkowie komisji badającej przyczyny wypadku stwierdzili znaczną korozję płyt węzłowych i innych elementów mostu, która ich zdaniem mogła przyczynić się do zawalenia konstrukcji. [2]
Ochrona antykorozyjna przy użyciu powłok proszkowych to praktyka dobrze udokumentowana i ciesząca się dużym uznaniem. [3] Powłoki proszkowe stosuje się do ochrony przed korozją tak różnych elementów, jak rury wodociągowe, rurociągi, meble ogrodowe, koła samochodowe oraz wykończenia architektoniczne i fasady budynków. Jednak zarówno w tych, jak i wielu innych zastosowaniach obserwuje się potrzebę zwiększenia odporności na korozję. Wychodząc naprzeciw temu zapotrzebowaniu, firma Dow Powder Coatings opracowała nową generację odpornych na korozję powłok proszkowych o standardowej trwałości na bazie poliestrów z przeznaczeniem do podłoży aluminiowych. W nowych powłokach wykorzystano specjalne żywice syntetyczne opracowane w naszych laboratoriach, które obecnie oczekują na przyznanie patentu. Nowe powłoki są produktami niezawierającymi TGIC, które pod względem trwałości zewnętrznej nie ustępują systemom dostępnym obecnie na rynku.Ilustracja 1.
Ochrona antykorozyjna
Ilustracja 1 przedstawia dane z badań w mgle solnej według normy ASTM B117 dotyczące dwóch powłok proszkowych: w jednej wykorzystano zwykły, powszechnie dostępny poliestr, a w drugiej – poliestr opracowany przez naszą firmę (pod nazwą XTRA-CORR™). W badaniu tym jako podłoże wykorzystano aluminium z powłoką Alodine [4], a czas trwania ustalono na 7000 godzin. Odporność na korozję wraz z upływem czasu oceniano przez pomiar podpełzania powłoki od znacznika X wyrytego na płytach na początku badania. Na ilustracji wyraźnie widać wyższość systemu XTRA-CORR™ nad ogólnodostępną powłoką antykorozyjną na płycie testowej poddanej odpowiedniej obróbce wstępnej.