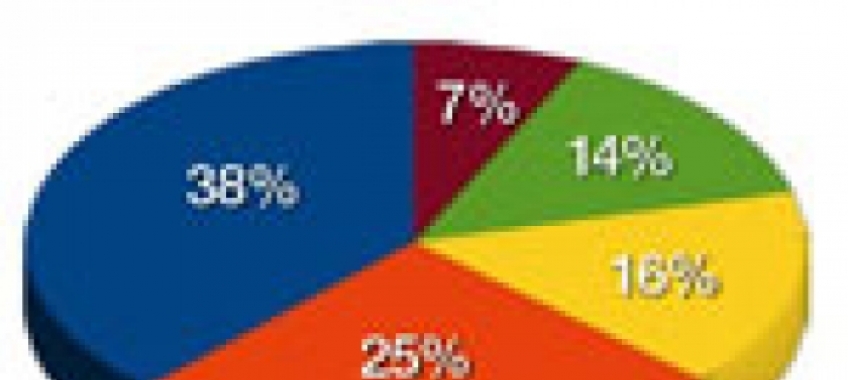
Jedna z pierwszych dobrze dopracowanych technik rozwinęła się w Wielkiej Brytanii 16 lat temu i wciąż jest stosowana [7]. Proces składał się z kilku etapów. Wyrób poddano wpierw anodowaniu w roztworze kwasu siarkowego, a następnie przeniesiono do innej wanny i poddano anodowaniu w kwasie fosforowym. Później, po opłukaniu, zastosowano barwienie elektrolityczne (por. tablica 4) z użyciem związków niklu. W wyniku całego procesu otrzymano powierzchnię szaroniebieską, podczas gdy barwienie elektrolityczne niklem, bez zmiany geometrii porów, dawało kolor złoty.
Współcześnie, dzięki stosowaniu różnorodnych technik można nadać wyrobom anodowanym niemal dowolny kolor, na razie jeszcze poza mlecznobiałym. Na fotografii 2 pokazano przykład różnorodności takich barw, która wydaje się, że powinna zaspokoić oczekiwania większości inwestorów. Warto jeszcze raz podkreślić, że są to zabarwienia całkowicie odporne na UV.
Fot. 1. Typowa wanna do anodowania w trakcie pracy.
Tablica 3. Przedstawienie sposobów barwienia powłoki anodowej na aluminium.
Podsumowanie
Jeśli można powiedzieć o jakimś metalu, że jest antykorozyjnie samowystarczalny, to jest nim z pewnością aluminium. Korozji ulega w niewielkim stopniu, a powłokę ochronną, o ile potrzebna, wytworzyć można na bazie jego tlenku, w procesie anodowania elektrolitycznego. Powłoka ta jest strukturalnie związana z podłożem, więc nie może ani popękać, ani złuszczyć się. Proces utrwalenia, czyli uszczelnianie, prowadzi do zamknięcia porów uwodnionym tlenkiem glinu, czyli tym samym, z grubsza, materiałem, który przez swój nieorganiczny charakter nie ulegnie degradacji pod wpływem promieniowania słonecznego, jak organiczne powłoki malarskie.
Ta unikalna metoda zabezpieczenia antykorozyjnego znakomicie dopełnia zalety lekkich wytrzymałych konstrukcyjnie stopów aluminium.
Znamienne jest, że do pozyskiwania tego materiału, jego przetwórstwa, antykorozji i barwienia potrzeba prądu. Przemysłowo aluminium uzyskuje się przez elektrolizę stopionego boksytu. W Polsce jedynie założona w 1966 r. Huta Konin produkowała aluminium w ilości ok. 50 tys. ton rocznie. Niestety, w lutym 2009 r. zakończyła przerabianie boksytu z powodu wysokiej ceny prądu i niechęci rządu do częściowego zniesienia akcyzy, chociaż na okres 2-3 lat [8]. Zapotrzebowanie na prąd było duże i sięgało 0,7-0,8% energii produkowanej w kraju i pewnie dlatego huta zlokalizowana była w pobliżu zespołu trzech elektrowni PAK (Pątnów-Adamów-Konin), które wytwarzają energię z taniego węgla brunatnego.