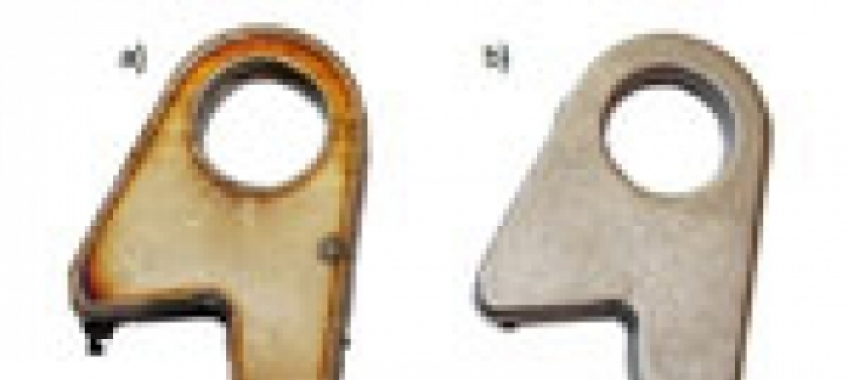
Wielkość dozowania płynu jest bardzo ważna, szczególnie w procesach, gdzie następuje usuwanie dużych naddatków z powierzchni detali. Szybkie odprowadzanie z pojemnika wygładzarki produktów ścierania jest warunkiem wysokiej sprawności procesu i czystości detali po obróbce. Ma to miejsce wtedy, kiedy wsad roboczy jest w sposób ciągły zraszany świeżymi porcjami roztworów wspomagających. Brak możliwości ciągłego zraszania wsadu i jednoczesnego odprowadzania produktów ścierania jest główną przyczyną tego, że do obróbki np. odlewów cynkalowych nie znalazły szerszego zastosowania wygładzarki rotacyjno-bębnowe.
Rodzaje detali obrabianych w wygładzarkach pojemnikowych pod powłoki malarskie
W wygładzarkach pojemnikowych poddawane obróbce są różnorodne detale techniczne oraz przedmioty codziennego użytku, które następnie są pokrywane powłokami malarskimi. Dominującą pozycję stanowią różnorodne odlewy detali technicznych i przedmiotów codziennego użytku, głównie ze znalu, aluminium i stopów magnezu. Wśród odlewów znalowych są to głównie uchwyty meblowe, klamki drzwiowe, elementy karniszy, galanteria obuwnicza i odzieżowa. Z aluminium i jego różnych stopów wytwarza się klamki okienne i drzwiowe, szyldy, ale głównie różnorodne odlewy techniczne (elektrotechniczne, obudowy urządzeń itp.). Są one standardowo obrabiane przed malowaniem w wygładzarkach pojemnikowych. Możliwości jakie stwarza stosowanie wibrościernej obróbki pojemnikowej dobrze pokazuje przykład ciśnieniowych odlewów aluminiowych przedstawionych na rys. 7.
Tablica 3. Chropowatość w µm powierzchni w różnych miejscach odlewu aluminiowego przed obróbką wibrościerną.
Rys. 9. Profilogram odlewu klamki przedstawionego na rys. 8a: Ra = 0,90 µm, Rmax = 5,92, Rz = 5,32 µm, Rt = 6,33 µm.
Taka powierzchnia wymaga ujednolicenia i doprowadzenia do większej jednorodności pod względem chropowatości, aby stworzyć warunki do dobrej i jednakowej przyczepności powłoki malarskiej na całej powierzchni odlewu.
Detale poddane obróbce w wygładzarce wibracyjnej przy użyciu kształtek żywicznych poliestrowych o charakterystyce K30 AXK uzyskały powierzchnię, którą można opisać następującymi parametrami chropowatości powierzchni: Ra = 0,46 - 0,58 µm, Rmax = 4,75 - 6,17 µm, Rz = 3,43 - 4,55 µm, Rt = 5,12 - 6,28 µm