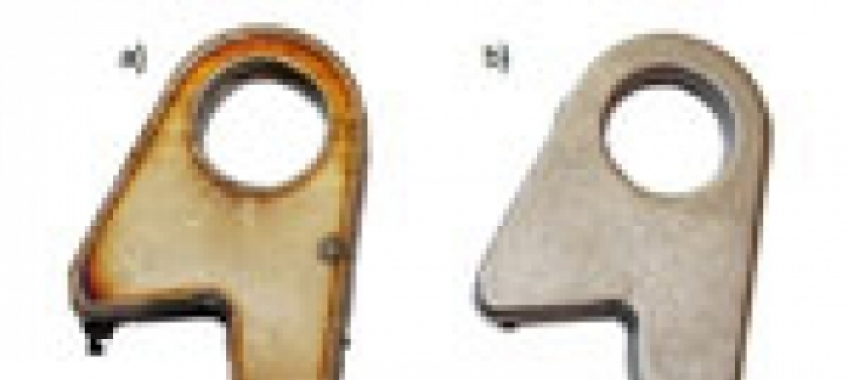
Nastąpiło zatem stosunkowo dobre ujednorodnienie powierzchni pod względem chropowatości. Jest to gwarancja dobrej i jednakowej na całej powierzchni detalu przyczepności powłoki malarskiej.
Przykład innego odlewu aluminiowego po obróbce wibracyjnej i po malowaniu przedstawiono na rys. 8. Profilogram powierzchni tego odlewu po obróbce przy użyciu kształtek poliestrowych K30 AXK przedstawiono na rys. 9. Powierzchnia odlewu ma zatem wystarczająco rozwiniętą powierzchnię dla dobrej przyczepności powłoki malarskiej.
W przypadku drobnych detali o skomplikowanym kształcie, ważne jest, aby kształtki ścierne docierały możliwie wszędzie i zapewniały jednakową przyczepność lakieru. Na rys. 10 pokazane są odlewy znalowe głównej części zamka błyskawicznego, który będzie poddany lakierowaniu.
W przypadku pojemnikowej obróbki detali stalowych, najważniejsze jest załamanie ostrych krawędzi, odtłuszczenie i oczyszczenie powierzchni, które będą poddane lakierowaniu. W przemyśle motoryzacyjnym bardzo często stosuje się kataforezę, czyli nanoszenie specjalnych lakierów poliuretanowych z wykorzystaniem przepływu prądów nisko- i średnionapięciowych.
Obróbka pojemnikowa zapewnia idealne przygotowanie powierzchni pod kataforezę. Bardzo istotna jest masowość tej obróbki, dzięki czemu w danym procesie przygotowywane są setki, a czasami tysiące detali jednocześnie. Przedmioty po obróbce pojemnikowej pokrywają się równomiernie lakierem, dzięki czemu powłoka jest bardzo odporna na uszkodzenia i warunki atmosferyczne.
Rys. 8. Klamka aluminiowa po obróbce wibrościernej (a) i po malowaniu (b).
Obróbce pojemnikowej poddawane są różnorodne przedmioty z tworzyw sztucznych przed nakładaniem na ich powierzchnię powłok malarskich (rys. 12). Do ich obróbki stosuje się kształtki żywiczne poliestrowe o wysokiej skrawności (AXC, AX). Do obróbki obcasów z ABS stosuje się duże kształtki K30 lub K40. Na powierzchni obcasów podczas obróbki pojemnikowej następuje zaokrąglenie ostrych krawędzi (ograniczenie odpryskiwania lakieru), usunięcie warstewki silikonu oraz zwiększenie chropowatości powierzchni tworzywa. Poprawia to przyczepność lakieru, zaś usunięcie tworzywa z miejsc jego wtrysku umożliwia zmniejszenie grubości nakładanego lakieru z 50 do 30 µm [9]. Umocnienie powierzchni obcasów podczas obróbki w kształtkach wpływa dodatkowo korzystnie na zmniejszenie śladów obić podczas użytkowania obuwia. Producenci obcasów potwierdzili, że w przypadku obcasów, które były poddane obróbce wibrościernej ilość warstw lakieru zmniejszyła się z 4 do 2. Można powiedzieć, że zastosowanie obróbki w wygładzarkach pojemnikowych spowodowało 50% oszczędności w zużyciu lakieru.