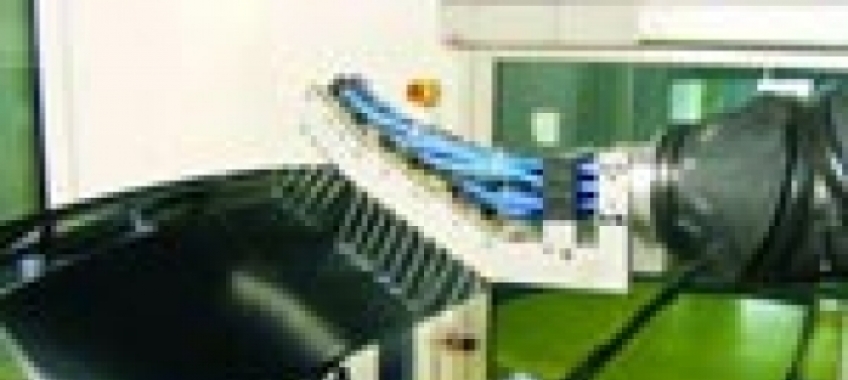
Robot z trzema głowicami dysz
Aby dopasować proces mycia do szerokiego spektrum elementów, jakie miały być poddane obróbce, zamontowano ramię robota z trzema głowicami, po pięć dysz każda. Zależnie od tego jaki element poddajemy obróbce, robot włącza i wyłącza poszczególne głowice. Działanie takie sprawia, iż system jest bardziej wydajny ekonomicznie. Wolne od frakcji oleistych powietrze oraz płynny dwutlenek węgla są poddawane ze zbiorników poprzez układ dozujący zlokalizowany w ramieniu robota. W pierwszym etapie instalacji system został dopasowany do rozmiarów linii lakierniczej (wielkość komory malowania). Zamontowano go pomiędzy strefą ciekłego mycia chemicznego a komorą suszarki. Ponieważ wciąż czekano na wyniki testów, oba rozwiązania przygotowania powierzchni przez pewien czas działały równolegle. - Ze względu na fakt, iż poszczególne elementy wykonane są z wielu rodzajów tworzyw, jak również z powodu różnic geometrii kształtu, były one badane każde z osobna przed zatwierdzeniem stosowania nowej metody - opowiada Markus Reimann. - Porównywano nowy system z dotychczasowym pod względem ilości pozostawionych osadów, przyczepności powłoki lakierniczej, jak i wizualnego efektu końcowego. Dzięki otrzymanym wynikom pracownicy departamentu części plastikowych byli w stanie również sami wprowadzić poprawki do programów sterujących pracą poszczególnych robotów.
Bezproblemowa technologia z mnóstwem zalet
Nowa technologia czyszczenia CO2 została zintegrowana na początku 2009 r. z linią lakierniczą BMW pracującą w systemie dwuzmianowym. Jest tu lakierowanych kilka tysięcy komponentów dziennie. Na specjalne zawieszki w strefie załadunku i odbioru zakładane są nowe detale. Największy procent malowanych detali stanowią zderzaki, które wymagają szczególnej uwagi w czasie trwania całego procesu nakładania powłok. W momencie, kiedy zderzak zostaje wprowadzony do kabiny, robot przy pomocy oprogramowania oczyszcza frontową część elementu a następnie całość zawieszki jest automatycznie przekręcana tak, aby ramię mogło zająć się drugą stroną. Całkowity czas potrzebny na oczyszczenie kompletnej zawieszki elementów nie zajmuje więcej niż 2 minuty. Po nałożeniu powłoki lakierniczej oraz wysuszeniu, system transportowy przenosi detale do stanowiska rozładunku. - Posiadając nową technologię CO2 wdrożoną przez ACP jesteśmy w stanie osiągnąć o wiele lepsze wyniki przygotowania powierzchni, inwestując mniejsze nakłady pracy - wyjaśnia menedżer projektu. - Usuwając stację myjącą zdobyliśmy dodatkową przestrzeń dla składowania części oraz na zadania montażu. Ponadto, zespół projektantów zyskał możliwość bardziej kreatywnej pracy nieskrępowanej parametrami linii. Przestaliśmy się martwić tym, iż element będzie posiadał delikatne opływowe kształty z dużą liczbą drobnych szczegółów, które do tej pory mogły być uszkodzone w mokrym procesie oczyszczania powierzchni. Zyskanie dodatkowej przestrzeni w hali produkcyjnej było również możliwe dzięki wyeliminowaniu kosztownej oraz konsumującej wiele energii stacji suszenia. Zmiany te były milowym krokiem dla rozwoju produkcji w fabryce BMW w Landshut.
Kolejny system czyszczenia CO2 w ramach głównej linii produkcyjnej
Po tym, jak BMW wprowadziło nowy system w Landshut, firma planuje już kolejny projekt z ACP. Dzięki bardzo dobrym rezultatom przygotowania powierzchni, oszczędności oraz powtarzalności, jak również wielu innym czynnikom, Grupa BMW postanowiła wdrożyć system przygotowania powierzchni suchym lodem na kolejnych liniach lakierniczych.
Doris Schulz