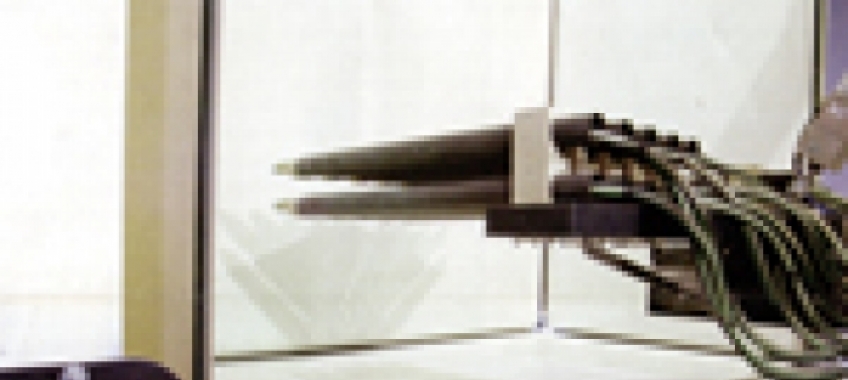
Centralnym punktem instalacji jest aplikacja proszku, która razem z "kuchnią proszkową" oraz workami z farbą (big-bagi) z czterema głównymi kolorami umieszczona jest w jednej oddzielnej kabinie. Jest ona wyposażona we własny system doprowadzający powietrze, który przez cały czas utrzymuje nadciśnienie wewnątrz kabiny, zapobiegając w ten sposób dostawaniu się pyłu do środka.
Sama komora lakiernicza składa się z trzech taśm pionowych oraz jednej taśmy poziomej biegnącej pod spodem. Zaprojektowana została przez firmę MS Oberflächentechnik specjalnie do powlekania pionowego oraz szybkiej zmiany farby. Podczas aplikacji przetrysk transportowany jest przez przesuwające się okrężnie taśmy pionowe do położonego na dole odciągu, a następnie prowadzony jest do jednego z dwóch cyklonów oraz do filtrów. Prędkość przesuwu przenośnika łańcuchowego w kabinie wynosi 1,5 m/min. Wiszące na nim profile transportowane są wzdłuż pistoletów po krzywej sinusoidalnej obracając się o 90° bądź 180°. Aplikacja elektrostatyczna prowadzona jest przez 20 automatycznych pistoletów, które podnoszone na wysokość ok. 7 m przemieszczają się wzdłuż profili.
Kluczowym elementem planowania instalacji oraz całego budynku było pionowe powlekanie 6-metrowych profili. Na pierwszym planie widoczna jest strefa odbiorcza, z tyłu po lewej paternoster z proszkiem oraz strefa podawcza. Na prawo od dźwigu znajduje się kabina lakiernicza, a przed nią 9-etapowa obróbka wstępna. Przenośnik łańcuchowy ma długość 500 m i posiada 2500 miejsc do zawieszania elementów.
Cztery główne kolory są w stałym połączeniu z instalacją podawania proszku, natomiast pozostałe farby pobierane są w razie potrzeby z 10-metrowego transportera okrężnego z proszkiem (paternoster). Aby zapewnić płynne podawanie proszku, a przez to jego jednostajne napylanie, w kuchni farb proszek jest w sposób ciągły przesiewany przez sito ultradźwiękowe.
Żelowanie i sieciowanie proszku następuje w piecu z ogrzewaniem pośrednim, z powietrzem obiegowym przy ok. 185°C i trwa ok. 45 minut. Następnie profile transportowane są przez strefę schładzania (odzysk ciepła wykorzystywany jest do ogrzewania hali) do stacji odbiorczej. Tutaj następuje podział: profile poniżej 3,50 m długości transportowane są pionowo do dołu i tam odbierane. Dla dłuższych elementów jest specjalne urządzenie, które odkłada profile poziomo na wózki. Przejście całego procesu od stacji podawczej do stacji odbiorczej trwa ok. 4,5 godziny. Po lakierowaniu elementy transportowane są do dalszej obróbki na produkcji.