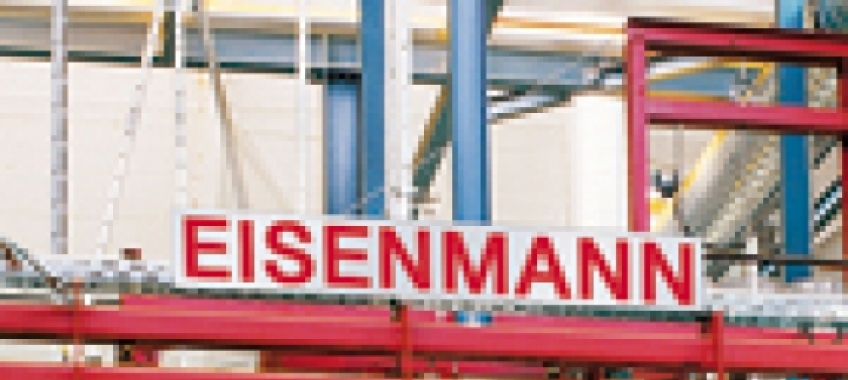
Lakierowanie proszkowe zoptymalizowane kosztowo
Rosnące ceny energii i wzrastająca presja konkurencyjności wymagają rozwiązań, które zmniejszają koszty lakierowania proszkowego. Firma Eisenmann przedstawia sposoby osiągnięcia tej szybko wzrastającej efektywności energetycznej urządzeń i dzięki temu znacznie obniżającej koszty eksploatacji lakierni.
Suszarki zaliczają się do największych odbiorników energii w procesie lakierowania. Zużycie większej część energii kojarzone jest jednak z podgrzewaniem wanien kąpieli agregatu do obróbki wstępnej i/lub zasilaniem central klimatyzacyjnych – w zależności od typu lakierni. Takie sposoby jak optymalizacja parametrów procesu, zastosowanie energooszczędnych komponentów czy inteligentnych systemów zarządzania energią, pozwalają na znaczące oszczędności.
Analiza poszczególnych etapów procesu
Często, nawet tylko przegląd różnych etapów procesu i uwzględnienie energooszczędnych alternatyw, prowadzi do ujawnienia małych, podstawowych możliwości oszczędzania. Dla przykładu, obniżenie temperatury kąpieli do obróbki wstępnej o 5 stopni C skutkuje oszczędnością aż do 15% energii cieplnej przyłączonej do agregatu obróbki wstępnej. A gdyby inaczej podejść do samego procesu obróbki wstępnej? Np. natryskowa obróbka wstępna składa się z operacji odtłuszczania, płukania, fosforanowania żelazowego, płukania i ponownego płukania. Sama zmiana na proces nanotechnologii umożliwia zmniejszenie ilości wymaganych operacji z 5 na 4, a także potrzebnej energii oraz obniża koszty inwestycji i zmniejsza potrzebną powierzchnię hali dla lakierni. Zastosowanie tzw. farb proszkowych niskotemperaturowych powoduje również obniżenie kosztów. Obniżenie temperatury wygrzewania proszków o 20 st. C pozwala na 15% oszczędność energii. Wartą zachodu może być też zmiana przestrzeni lakierowanej (tzw. okna lakierowania) ze względu na temperaturę i wilgotność w kabinie lakierniczej. Na przykład: jeśli wymagana jest temperatura 23 st. C a wilgotność 50%, to parametry te mogą być generalnie zmienione na 27 st. C i 65% wilgotności względnej – bez obniżenia jakości. Wskutek tego doprowadzamy mniej energii dla utrzymywania stałych warunków klimatycznych w przestrzeni kabiny. Oszczędności uzyskujemy też w przypadku suszarki wody (po obróbce wstępnej) zaprojektowanej jako system kondensacyjny.