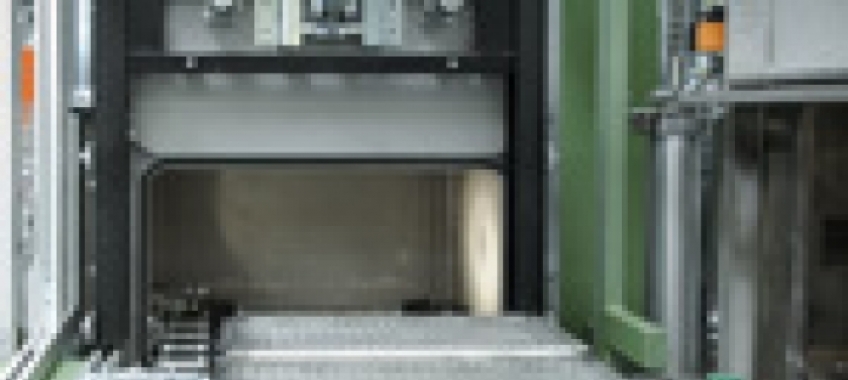
Ze względu na fakt, iż nadmiar materiału jest usuwany podczas maszynowego tworzenia odlewu, zanieczyszczenia nigdy nie mogą być w całości usunięte. Na ilość i rodzaj zanieczyszczeń pozostających na detalu wpływ mają ponadto jakość chłodziw używanych podczas obróbki oraz rodzaj innych płynów używanych w maszynach produkcyjnych. Odpowiednie oczyszczenie/filtracja zapewnia, iż usunięte z powierzchni detali cząstki nie wracają ponownie do systemu przygotowania powierzchni. Dodatkową operacją pozwalającą na uzyskanie jeszcze lepszej jakości powierzchni jest odpowiednio dobrany proces płukania. Szczególnie jest on wydajny, jeśli zasilimy go z osobnego zbiornika ze środkiem płuczącym. Na pierwszy rzut oka powyższe operacje wiążą się z dodatkowymi nakładami pieniędzy. Nic bardziej mylnego. Zainwestowane wcześniej środki zwracają się w późniejszych etapach produkcji dzięki krótszemu czasowi oczyszczania lub/oraz dłuższej żywotności kąpieli myjących, jak również finalnie poprzez wyższą jakość produktu końcowego. Usunięte w pierwszym etapie obróbki powierzchni kontaminanty w procesie wstępnego oczyszczania poprzez wibracje, otrząsanie, spłukiwanie czy też odsysanie są usuwane i nie zanieczyszczają dalszych kąpieli myjących.
W przypadku wieloetapowego procesu produkcji i obrabiania części metalowych wdrożenie międzyprocesowych etapów oczyszczania powierzchni pozwala na uniknięcie gromadzenia się zanieczyszczeń, jak również odkładania się środków chemicznych na powierzchni.
Idealnie skomponowany proces oczyszczania powierzchni
Nowoczesne linie oczyszczania powierzchni są w stanie sprostać nawet najbardziej wymagającym standardom jakości. Jest to możliwe dzięki idealnemu dopasowaniu procesu do rodzaju zanieczyszczeń jakie mają być usuwane, kształtu detalu oraz wymagań co do klasy czystości jaka ma być uzyskana. Założenia co do limitu ilości cząstek mniejszych niż 1000 µm wewnątrz jednostek napędowych oraz skrzyń biegów mogą być jedynie spełnione w przypadku, kiedy etap czyszczenia został indywidualnie dopasowany do każdej z części. Obecnie, używając podejścia wieloetapowości procesu, możliwe staje się spełnienie wyżej postawionych założeń. Zazwyczaj pierwszy etap polega na mechanicznym usunięciu zanieczyszczeń, podczas którego pozbywamy się płynów używanych podczas formowania kształtu detalu. Etap drugi związany jest z procesem zanurzeniowego przygotowania powierzchni. Do wanny poniżej poziomu zalania wtłaczana jest woda pod ciśnieniem od 10 do 15 barów. W efekcie wirująca woda wymywa wszelkie zanieczyszczenia i odłamki z całej powierzchni detalu, nawet z trudno dostępnych miejsc, jak np. ślepe otwory. System dysz wodnych ma za zadanie całkowite oczyszczenie oraz dotarcie do trudno dostępnych miejsc, co pozwala na osiągnięcie zadowalających wyników w bardzo krótkim czasie. Na efekt ten składają się wysokie ciśnienie myjącej wody oraz jej właściwości ścierne. Po etapie płukania następuje proces suszenia.