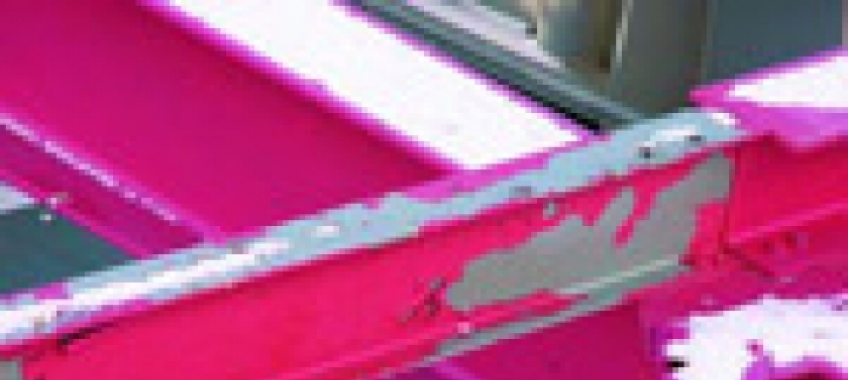
Warunki, w jakich przewidywane jest nakładanie farby, również wpływają na dobór parametrów aplikacji. Lepkość i gęstość każdego wyrobu lakierowego wzrastają wraz z obniżeniem temperatury otaczającego powietrza. Duża lepkość farby powoduje trudności w zassaniu jej przez pompę oraz jest przyczyną zwiększonych oporów przepływu zarówno przez pompę, jak i przez wszystkie węże wysokociśnieniowe między pistoletem natryskowym a pompą. Ponieważ jakość rozpylania zależy od ciśnienia na dyszy, a nie na wyjściu z pompy, należy przy doborze sprzętu i jego parametrów uwzględnić spadki ciśnienia spowodowane oporami przepływu.
Lepkość farby można zmniejszyć przez jej podgrzanie. Dla tego celu stosuje się odpowiednie podgrzewacze przepływowe, wchodzące w skład zestawu aplikacyjnego, które pozwalają podnieść temperaturę farby do 50-80 st. C, co jest równoznaczne z istotnym spadkiem lepkości. Kształt konstrukcji w decydującym stopniu wpływa na dobór kąta rozpylenia dyszy. Każda dysza do natrysku bezpowietrznego charakteryzowana jest dwoma parametrami: wielkością otworu i szerokością rozpylanego strumienia farby, czyli tzw. kątem rozpylenia. Ten ostatni parametr opisywany jest zwykle pierwszą cyfrą w symbolu dyszy; np. 619 oznacza dyszę o wielkości otworu 0,019 cala i kącie natrysku 60 st. Do konstrukcji szkieletowych i kratowych wybiera się dysze o małym kącie natrysku, tym mniejszym, im mniejsza jest szerokość kształtowników przeznaczonych do malowania. Jeżeli zostanie użyta dysza o zbyt dużym kącie, to część farby, zamiast na malowany obiekt, poleci w powietrze bądź też na niższe fragmenty konstrukcji, powodując nierównomierną i nadmierną grubość pokrycia w tych rejonach. Ponadto, takie postępowanie zwiększa zużycie wyrobu, zawyżając niepotrzebnie koszty procesu. Do dużych powierzchni płaskich zalecane są dysze o kątach natrysku 70 st. i więcej.
Wady powłok wynikające ze złego przygotowania podłoża
Za źle przygotowaną powierzchnię uważa się taką, z której zanieczyszczenia nie zostały usunięte w stopniu wymaganym dla danej farby oraz nie wytworzono odpowiedniej dla niej struktury geometrycznej. Zanieczyszczenia powierzchni to przede wszystkim zgorzelina, rdza oraz osadzone zanieczyszczenia mechaniczne o różnym charakterze oraz osadzone z atmosfery, czy też z procesów technologicznych, zanieczyszczenia jonowe.
Malowanie na zgorzelinę i rdzę
Pozostawienie zgorzeliny czy rdzy na podłożu powoduje przyśpieszenie destrukcji powłok w wyniku korozji podpowłokowej a ponadto nasila procesy osmozy i obniża przyczepność. Dodatkowo, pokrycia położone na zgorzelinę mogą w bardzo krótkim czasie odpadać, łącznie ze zgorzeliną, od podłoża z uwagi na różnice we współczynnikach rozszerzalności cieplnej stali i zgorzeliny. Typowy przykład braku przyczepności pokrycia na zardzewiałej powierzchni pokazano na rys. 3.