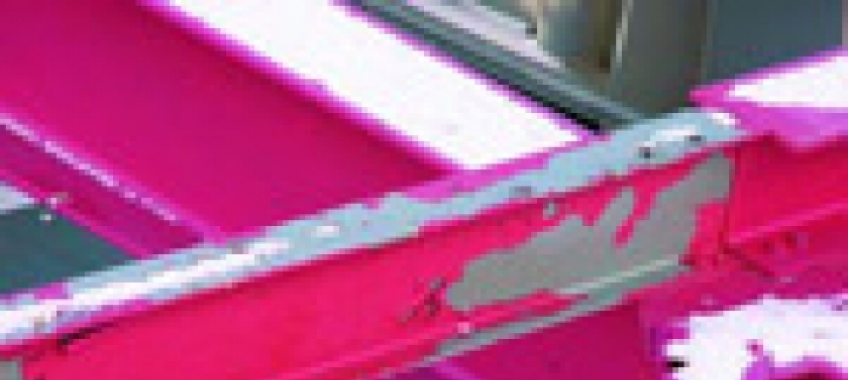
O trwałości powłokowego zabezpieczenia przed korozją w równym stopniu decyduje dokładne usunięcie wszystkich zanieczyszczeń z podłoża i wytworzenie na powierzchni prawidłowej struktury geometrycznej, jak i nałożenie farby z zachowaniem zasady dobrej praktyki malarskiej.
Dowolnie dodany rozpuszczalnik może powodować:
- rozpuszczanie składników wcześniej nałożonej powłoki
- pęcznienie - w przypadku nieaktywnych rozcieńczalników, w odniesieniu do powłok termoplastycznych i chemoutwardzalnych, może nastąpić pęcznienie. Wytworzone wówczas silne naprężenia wewnętrzne mogą spowodować pękanie, poprzedzone miejscowym spęcherzeniem bądź też może wystąpić delaminacja poprzedzona silnymi zmarszczeniami
- przenikanie międzywarstwowe (krwawienie) - jest to zjawisko dyfuzji z powierzchni wcześniej nałożonej powłoki koloryzujących składników do powłoki nawierzchniowej, powodujące zmianę jej barwy.
Wady wynikające z nieprzestrzegania technologii zalecanej przez producenta
Nieprzestrzeganie wymaganych technologią czasów pomiędzy nakładaniem poszczególnych warstw, przy niektórych wyrobach, niesie za sobą dalekosiężne skutki. Skrócenie wymaganego czasu jest niekorzystne dla wszystkich wyrobów lakierowych. Dawniej, kiedy nie było farb grubopowłokowych, istniała zasada, że natryskiem można malować „mokro na mokre”. Powłoki miały grubość 15-25 mm i taka technologia była możliwa do zastosowania. Obecnie, kiedy większość wyrobów jest grubopowłokowa, nie należy skracać czasu pomiędzy nakładaniem powłok, gdyż utrudnia to odparowanie rozpuszczalnika z dolnych warstw. Mogą również tworzyć się naprężenia powodujące zmarszczenie powłok farb schnących oksydacyjnie z uwagi na utrudniony dostęp tlenu do dolnych warstw. Jeżeli skrócenie czasu nałożenia kolejnej warstwy zbiegnie się z niską temperaturą powietrza i dużą jego wilgotnością, powłoka może bardzo długo pozostać „mokrą” lub, w najlepszym razie, miękką. Wyroby schnące w wyniku procesów chemicznych, w tym również schnące oksydacyjnie, mają ograniczony najdłuższy okres do przemalowania powłoki. Przekroczenie dopuszczalnego czasu powoduje znaczne osłabienie bądź nawet brak przyczepności drugiej z nakładanych powłok (po jej wyschnięciu). W pierwszej połowie obecnego wieku, wychodząc naprzeciw stosowanym technologiom montażu dużych konstrukcji, szereg producentów farb epoksydowych, bez pogłębionych badań, zezwoliło na długi okres do przemalowania, w niektórych przypadkach – nawet nieograniczony. Efektem tej lekkomyślności było i jest szereg konstrukcji, w tym głównie mosty, z których po roku eksploatacji „spada” powłoka nawierzchniowa z epoksydowej międzywarstwy, jak to np. pokazano na rys. 6. Oczywiście, odium spadło na wykonawców. Ale firmy wykonawcze nie są instytucją charytatywną – jeżeli w specyfikacji inwestora wymagano jedynie umycia nałożonej powłoki (mimo że okres od jej nałożenia wynosił ponad rok), to na własny koszt nie będą dodawały kolejnego procesu technologicznego. Były to ewidentne wady powłok wynikające ze złej specyfikacji a nie wady aplikacyjne. Podkreślenia wymaga fakt, że specyfikacje opracowywano w oparciu o informacje producenta farb. Dopiero badania prowadzone m.in. w Polsce [3,4,5] wykazały, że skredowana powłoka epoksydowa wymaga drastyczniejszego potraktowania przed nałożeniem kolejnej warstwy, nie wystarcza samo umycie.