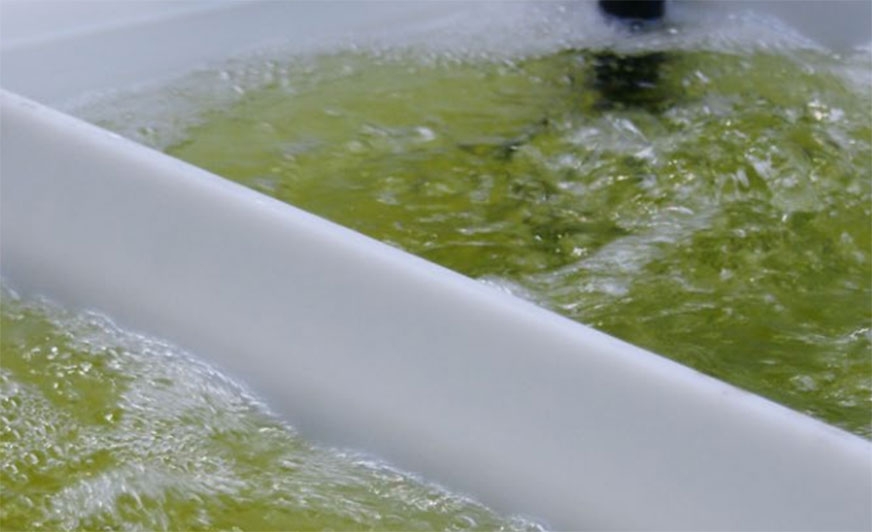
"Zaplecze" linii galwanicznej.
"Uczulanie" powierzchni detali z plastiku
Tworzywa PC/ABS i ABS to materiały nieprzewodzące prądu elektrycznego. Aby pokryć je powłokami galwanicznymi, konieczne staje się stworzenie na ich powierzchni warstwy przewodzącej elektryczność. Pierwszym zabiegiem niezbędnym do ukształtowania takiej warstwy jest wytrawianie powierzchni detali. - Trawienie bowiem powoduje wytworzenie chropowatej powierzchni, która umożliwia adhezję mechaniczną warstwy metalicznej do powierzchni materiału polimerowego - mówi L. Michalski.
Następnie detale umieszcza się w kąpieli w roztworze zawierającym cynę i pallad. Zapewnia to niezwykle silne przyleganie powłok niklu chemicznego w trakcie dalszej obróbki tworzyw. W ten sposób przygotowana wytrawiona powierzchnia, pokryta koloidem cynowym i palladowym, zapewnia przyczepność mechaniczną powłoki galwanicznej. Ten proces aktywacji sprzyja chemicznemu osadzeniu cienkiej podwarstwy przewodzącej metalu. Po pokryciu powierzchni detali roztworem cyny i palladu konieczne jest usunięcie jonów cyny, aby pozostały pallad mógł reagować z niklem, nakładanym na elementy w kolejnym etapie procesu wytwórczego.
"Uczulanie" powierzchni detali z plastiku
Bezprądowe powlekanie niklem
Bezprądowe powlekanie niklem jest reakcją wykorzystywaną do osadzania powłok niklu na określonym podłożu. Jest to proces niewymagający przepuszczania prądu elektrycznego przez roztwór. W tym etapie na detale nanoszona jest cienka warstwa niklu (chemicznego), który stanowi pierwszą powłokę galwaniczną. Warto zaznaczyć, iż bezprądowe powlekanie ma kilka przewag nad klasycznymi galwanicznymi metodami powlekania. Nie potrzeba wykorzystywać w niej źródła prądu, można osadzać na powierzchni bez względu na jej kształt oraz można osadzać na nieprzewodzących powierzchniach.
Następnie, standardowy schemat galwanizowania przewidywałby pokrywanie detali powłoką z miedzi. Zaprojektowany dla KLG proces wytwarzania zawiera dodatkowe etapy produkcyjne i rozwiązania technologiczne, pozwalające na wyjęcie elementów z linii po ich bezprądowym powlekaniu niklem, poddanie ich wytrawianiu laserowemu, a następnie ponowne włączenie detali do procesu galwanizowania (patrz ramka na poprzedniej stronie).
Pierwsza warstwa niklowa powstała w efekcie powlekania bezprądowego jest bardzo cienka i podatna na uszkodzenia. Dlatego też, w zależności od kształtu detalu, wdrożony proces technologiczny zapewnia możliwość położenia drugiej, grubszej niklowej warstwy ochronnej. Zapewnienie odpowiedniej grubości niklowej warstwy ochronnej jest szczególne istotne w uwagi na kolejny etap powlekania elektrolitycznego, jakim jest nakładanie powłoki miedziowej. Powlekanie miedzią to szczególnie intensywna reakcja elektrochemiczna, która mogłaby uszkodzić wytrawioną powierzchnię materiału tworzywa sztucznego. Powłoka miedziowa tworzy grubą, plastyczną i przewodzącą prąd elektryczny warstwę na powierzchni niklowej. Kolejne nakładane powłoki metaliczne cechują się zdecydowanie większą sztywnością. Powłoki niklowe zapewniają połysk gotowych elementów. Zaprojektowano trzy różne rodzaje zbiorników do powlekania niklem: o efekcie półmatowym, błyszczącym oraz satynowym. W zależności od preferencji klienta, na daną partię elementów nakładana jest powłoka niklu o pożądanym efekcie.
Ostatnim etapem w procesie produkcyjnym jest powlekanie detali chromem, czyli tzw. chromowanie. Na powierzchni zanurzonych w zbiorniku do chromowania detali tworzy się cienka warstwa powłoki z chromu. Chroni ona elementy przed zarysowaniem, tworząc bardzo twardą powierzchnię.
Elementy innowacyjności
Linia do powlekania elektrolitycznego zawiera nowatorskie rozwiązania technologiczne, w tym:
- każdy zbiornik, etap produkcyjny, proces wytwarzania danego rodzaju produktu oraz całościowy przebieg procesu produkcji jest sterowany komputerowo. Ma to na celu optymalne wykorzystanie wszystkich zbiorników w linii produkcyjnej
- przenośniki odpowiedzialne za transport wieszaków galwanizerskich wykorzystują pozycjonowanie laserowe oraz komunikują się z centralną jednostką sterującą za pomocą wi-fi
- płukanie detali dokonywane pomiędzy poszczególnymi podprocesami powlekania elektrolitycznego jest prowadzone metodą kaskadową lub kaskadową z natryskiem. Dzięki tego typu rozwiązaniu możliwe jest ograniczenie zużycia wody nawet do 90% w porównaniu ze standardowym procesem płukania
- napięcie w zbiornikach do powlekania miedzią jest zwiększane stopniowo wraz z grubością tworzącej się warstwy miedziowej. Powłoka niklowa osadzona bezprądowo na powierzchni ABS lub PC/ABS jest bardzo cienka. Zbyt wysokie napięcie w zbiorniku do miedziowania mogłoby ją uszkodzić, co w konsekwencji spowodowałoby zniszczenie powlekanego detalu. Jednakże, wraz ze wzrostem grubości osadzanej warstwy miedzi, napięcie w zbiorniku do miedziowania może być coraz wyższe.
Zastosowane rozwiązania prowadzą do ograniczenia ilości braków produkcyjnych (niewłaściwie powleczonych elementów), ograniczenia zużycia ilości drogich surowców (metali) oraz substancji chemicznych. Uruchomiony proces wytwarzania jest zatem optymalny nie tylko z punktu widzenia efektywności technologicznej, organizacyjnej i czasowej, lecz również bardziej przyjazny dla środowiska.
Opracował Grzegorz Petka
Fot. Grzegorz Petka