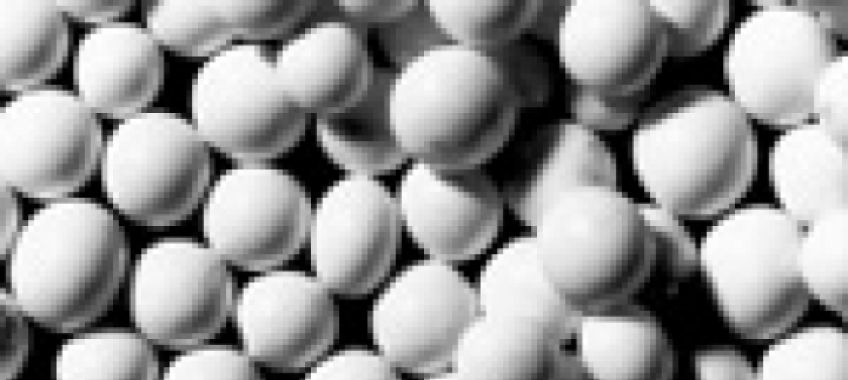
Tłumaczy się to wyższym poziomem naprężeń ściskających na powierzchni, w połączeniu z gładszą powierzchnią i niską intensywnością koncentracji uderzeń ścierniwa (pokrycia). Lewy obszar poniżej 0,15 mm nie został rozpoznany. To był punkt wyjścia dla dalszych prac badawczych [4]. Mając na celu optymalizację wydajności w miejscu zmęczenia korzenia zęba koła zębatego, kilkakrotnie nawęglanego i kulowanego z użyciem śrutu staliwnego lub ceramicznego na płaskich próbkach badanych na zmęczenie poprzez zginanie. Mierzono w tym celu szybkość przemiany austenitu, mikrotwardość i pozostały profil naprężeń wewnętrznych. Maksymalny efekt osiąga się po podwójnym kulowaniu stali hartowanej Ck 45 o twardości 665 HV 10 śrutem staliwnym okrągłym, a następnie kulkami ceramicznymi [4]. Najwyższą odporność zmęczeniową i poprawę wytrzymałości uzyskuje się przez jednokrotne nagniatanie stali 16MnCr5 o twardości 1030 HV 0,2 kulkami ceramicznymi. Zastosowano kulowanie nawęglanych przekładni w 1999 r. [4]
Parametry kulkowania:
- śrut staliwny S 300 μm, F25 intensywność Almena - 30, wskaźnik pokrycia 150%
- śrut staliwny S 800μm, F55 intensywność Almena - 60, wskaźnik pokrycia 150%
- kulki ceramiczne Z150, intensywność Almena F10 – 15 N, wskaźnik pokrycia 400%
Kulki ceramiczne Z150 poprawiają w tym eksperymencie wytrzymałość zmęczeniową o 76%, w porównaniu z 45% przez śrut stalowy #300 i 42% przez śrut # 800 [4].
Kulki ceramiczne stosowane są w szczególności do:
- usuwania przebarwień i zgorzeliny spawalniczej, zwłaszcza ze stali kwasoodpornej;
- czyszczenia powierzchni metalowych form, kokili, rdzeni i narzędzi;
- czyszczenia instrumentów medycznych
i protez tytanowych;
- czyszczenia wyrobów cienkościennych,
w tym też tworzyw sztucznych i okularów;
- oczyszczenia z nagarów głowic cylindrów silników;
- zmniejszania naprężeń powierzchniowych po spawaniu i obróbce plastycznej metali (na przykład sprężyn);
- nadawania połysku powierzchniom zbyt chropowatym (stali nierdzewnej
i powierzchni felg aluminiowych).
Wnioski
Stosowanie ceramicznych kulek do poprawy wysokiej wytrzymałości stali posiada wysoką wydajność wygładzania powierzchni i wprowadzenia wysokiego poziomu naprężeń ściskających na powierzchni, unikając powstawania i wzrostu pęknięć na powierzchni kulowanej, rozwiązując większość problemów zmęczeniowych. W przypadku kulowania dwukrotnego, najpierw śrutem staliwnym, a następnie kulkami ceramicznymi, pozwala zrekompensować efekt głębokiego usuwania naprężeń rozciągających bez utraty warstwy wierzchniej. W niektórych przypadkach przemysłowych jedno kulkowanie kulkami ceramicznymi może dawać te same, a nawet lepsze wyniki, w porównaniu z podwójnym kulowaniem za pomocą śrutu staliwnego. Pasywacja chemiczna usuwa wprawdzie powierzchniowe przebarwienia i hamuje korozję międzykrystaliczną, lecz nie usuwa naprężeń rozciągających oraz nie podwyższa wytrzymałości zmęczeniowej. Jest to metoda kłopotliwa w stosowaniu i wysoce szkodliwa dla pracowników, gdyż wymaga specjalnych stanowisk pracy oraz neutralizacji powstających ścieków. Wyższej o 50 do 60% wydajności kulek ceramicznych względem kulek szklanych podczas czyszczenia i utwardzania powierzchni towarzyszy dodatkowo to, że nie uszkadzają one kształtu powierzchni oczyszczanej, to jest krawędzi ani oznakowań na powierzchni. Dzięki temu kulki ceramiczne są bardziej predysponowane od kulek szklanych do czyszczenia metalowych form używanych w różnych przemysłach (gumowym, tworzyw sztucznych, szklarskim i innych) oraz metalowych kokili odlewniczych. Niska stosunkowo gęstość kulek ceramicznych i ich optymalna skuteczność czyszczenia pozwalają, żeby podczas obróbki pneumatycznej stosować obniżone ciśnienie sprężonego powietrza z 6 do 4 barów. Daje to znaczącą oszczędność zużycia energii na wytworzenie sprężonego powietrza, bo około 33 % oraz mniejsze pylenie kulek ceramicznych i polepszenie widoczności w kabinie czy komorze. Pozwala to na dodatkowe obniżenie kosztów eksploatacyjnych filtrowania powietrza i separacji zanieczyszczeń.