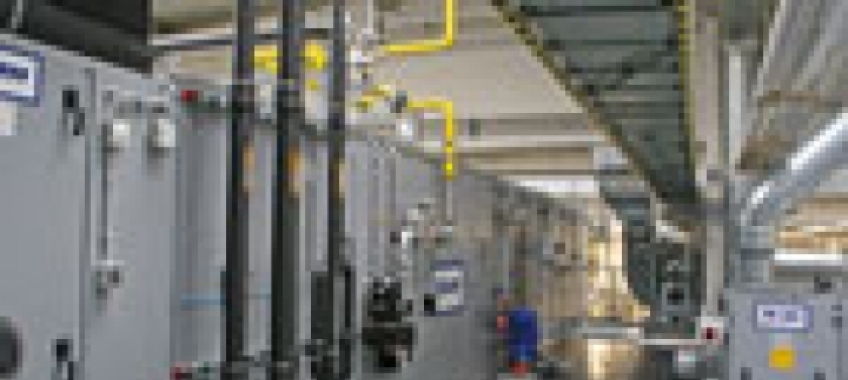
Różnorodność elementów szczególnym wyzwaniem
Szczególnym wyzwaniem przy projektowaniu instalacji były ogromne różnice w wielkości poszczególnych elementów. Najmniejszy silnik waży około kilograma i ma długość około 200 mm, natomiast największy silnik, przy długości obudowy jednego metra, waży 150 kg. Dla takiego spektrum lakierowanych elementów musiała zostać opracowana koncepcja niezawodnego systemu przenośników, która mogłaby spełniać wymagania dotyczące zarówno zdolności produkcyjnej, jak i niezbędnej elastyczności. Na wszystkie przenośniki można obecnie załadować 1, 2, 3 lub 4 silniki, w zależności od modelu i wielkości. Na przenośniku znajdują się odpowiednie miejsca do zamocowania z charakterystycznymi dla każdego typu silnika elementami stabilizującymi. Mocują one wał silnika i utrzymują silnik w stabilnej pozycji. Jednocześnie powierzchnia stykowa podnośników ukształtowana jest w taki sposób, że nie jest konieczne oddzielne maskowanie stopy. Niewykorzystane miejsca na przenośniku zakrywane są zatyczkami. W ten sposób lakier nie przedostaje się do prowadnic. System sprawdził się już bardzo dobrze w dotychczasowej produkcji. Po załadowaniu system przenośników transportuje elementy do jednej z dwóch kabin lakierniczych - w zależności od wersji do malowania ręcznego lub automatycznego. Obie kabiny wyposażone są w systemy filtracji suchej z filtrami papierowymi (rys. 4). Do malowania przy pomocy robota, programy lakiernicze opracowywane są odpowiednio do geometrii elementu i stopnia załadowania przenośnika. Po wprowadzeniu do kabiny silniki lakierowane są z przodu. Następnie w środku kabiny przenośniki są odwracane i w kolejnej strefie silniki lakierowane są od tyłu. Przy programowaniu robotów szczególne wyzwania stanowią mnogość wariantów silników oraz umiejscowienie połączeń elektrycznych. Ustawienie wejść elektrycznych może różnić się również w tym samym wariancie. To musi być wzięte pod uwagę podczas przygotowywania programów lakierniczych, gdyż także obszary za wtyczką muszą być pomalowane według specyfikacji.
Adapter mieszający w przegubie robota
Malowanie w automatycznej kabinie lakierniczej odbywa się przy pomocy robota (b+m T1) wyposażonego w automatyczny pistolet natryskowy rozpylający (b+m, typ LZ-2008). Za doprowadzanie materiałów malarskich odpowiedzialne są 2-komponentowe (2K) systemy dozujące. Końcowe mieszanie obu składników następuje w mikserze zamontowanym bezpośrednio na przegubie robota. Dzięki krótkiej odległości pomiędzy mikserem a pistoletem natryskowym, w układzie doprowadzającym farbę do pistoletu znajduje się jedynie 15 cm3 wymieszanego materiału. W ten sposób uniknięto bądź zminimalizowano zakłócenia oraz stratę materiału podczas płukania. Ze względu na małe odległości, bardzo krótkie są także czasy zmiany farby wynoszące poniżej 10 sekund. Do instalacji należy również urządzenie czyszczące dysze powietrza, które poprzez obrotowe szczotki umożliwia automatyczne czyszczenie. Do malowania używa się czterech lakierów wodorozcieńczalnych jako kolory standardowe, jak również jednego lakieru na bazie wody jako kolor specjalny. W manualnej kabinie stosuje się dodatkowo lakier rozpuszczalnikowy. Do płukania stosowane są trzy środki: woda demineralizowana z dodatkami, czysta woda demineralizowana oraz detergent na bazie rozpuszczalnika. Środki czyszczące automatycznie przyporządkowywane są do używanego materiału. Zainstalowane są dwa urządzenia dozujące 2K. Oba ustawione są blisko kabin natryskowych, aby przewody doprowadzające farbę nie były zbyt długie.