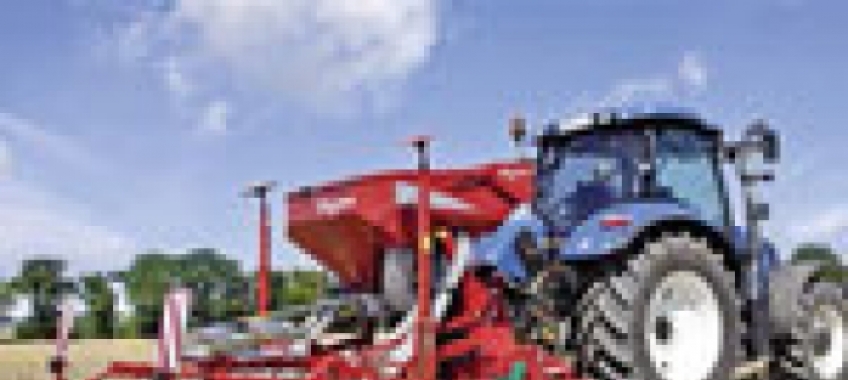
Należało również uwzględnić malowanie w specjalnych odcieniach na oddzielnej linii proszkowej. Do projektu włączono także przelotową oraz ręczną instalację śrutowniczą do odrdzewiania i przygotowania powierzchni przed lakierowaniem.
Profil wymogów stawianych lakierowaniu był bardzo podzielony i nadano mu następujące istotne kryteria:
- ochrona przed korozją do około 1000 godz. w komorze solnej
- zoptymalizowanie powierzchni pod względem stopnia połysku, trwałości chemicznej i mechanicznej, twardości powierzchni i lepszej przyczepności
- zredukowanie emisji rozpuszczalnika
- zwiększenie możliwości produkcyjnych
- równomierne powlekanie wysokiej jakości, także w trudno dostępnych miejscach
- zwiększenie produktywności i wartości dodanej
- wydajność energii, dobre wykorzystanie przestrzeni i umiejętne zintegrowanie opisanych procesów
Indywidualne dopasowanie procesów produkcyjnych
W oddziale w Soest grupa Kverneland produkuje z wykorzystaniem systemu Kanban. Jest on sposobem sterowania procesem produkcji. Procedura ta opiera się jedynie na rzeczywistym zużyciu materiałów na zestawiania i miejscu konsumpcji. - Produkujemy tylko na zlecenie klienta i to wyłącznie maszyny siewne dla rolnictwa - wyjaśnia Andreas Grafe i wskazuje na zależne od branży i sezonu szczyty produkcyjne: - W pierwszych czterech miesiącach wiosny zarabiamy już więcej niż wynosi nasz półroczny obrót.
Równolegle do projektowania instalacji i przetargu przetestowano różnych oferentów chemii do obróbki wstępnej, farby KTL i proszkowej. Konieczne były szczegółowe kontrole w celu ustalenia bezpiecznego przebiegu postępowania. Stwierdzono przy tym znaczne różnice jakości.
Test różnych urządzeń śrutowniczych miał szczególne znaczenie. Jak się jednoznacznie okazało, głębokość nierówności śrutowania powierzchni wpływa na wyniki w teście w komorze solnej. Przy łącznej grubości warstw od 50 do 55 ?m katodowego lakierowania natryskowego, głębokość nierówności nie powinna znacznie przekroczyć 30 ?m (zjawiska strukturalne).