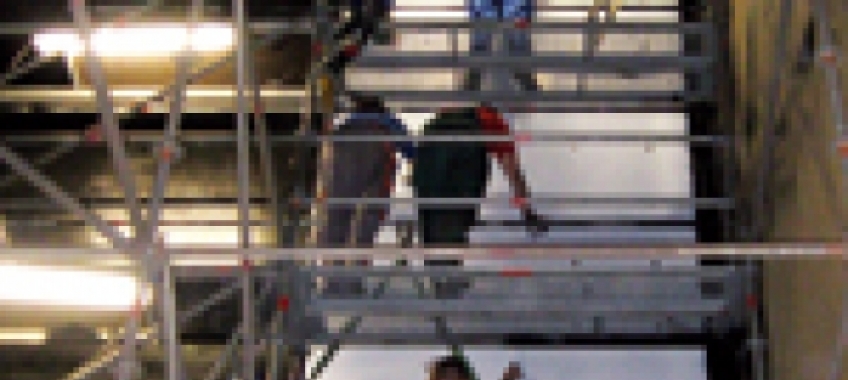
Warunkiem ekspansji krajowych antykorozyjnych wykładzin gumowych jest bezwzględna potrzeba inwestycyjna polegająca na zamianie technologii „kalandrowania” na „wytłaczanie szczelinowe z odgazowaniem próżniowym”, co z równoczesną potrzebą wdrożenia produkcji samowulkanizujących gum bromobutylowych praktycznie oznacza przymus skoku technologicznego z XIX do XXI wieku i towarzyszące mu milionowe nakłady inwestycyjne z zakupami licencyjnymi u konkurencyjnych firm światowych włącznie. I bez złudzeń – jakikolwiek rachunek ekonomiczny pokazuje nierealność takiego przedsięwzięcia, w związku z czym na przyszłej mapie krajowych producentów gum antykorozyjnych można umieścić dwa-trzy punkty z przypisaniem im tendencji wygasającej. Podobnie wygląda sprawa z produkcją materiałów żywicznych i wykładzin polimerowych. Trudno przewidywać, by któryś z krajowych wytwórców zaoferował komponenty do powłokowania natryskowego na bazie własnych winyloestrów z napełniaczami płatkowymi w klasie jakościowej akceptowanej przez podstawowego odbiorcę, czyli energetykę zawodową. Powiązania kapitałowe i relacje „producent – odbiorca” przesądziły także o tym, że produkcja wykładzin polimerowych, w tym zaawansowanych technicznie (np. typu teflonowego z podłożem kaszerowanym), jest ulokowana poza krajem i nie zanosi się na to, by rodzimi producenci tworzyw mogli w przewidywalnym okresie przedstawić równorzędne oferty materiałowe.