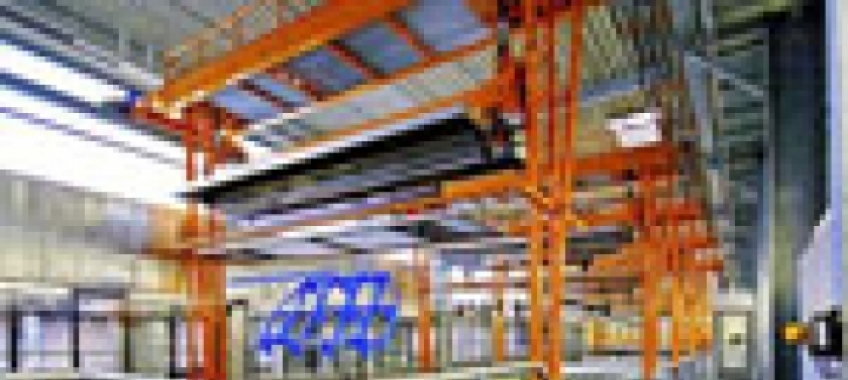
Dr Thomas Barmbold: My również widzimy znaczące oszczędności w porównaniu do dotychczas przeprowadzanego procesu dzięki zastosowaniu powlekania kataforezą. Z jednej strony wynika to z wydatnie poprawionej logistyki przebiegu procesu produkcyjnego, większej niezawodności malowania i związanej
z tym poprawy jakości, a z drugiej strony, również z opisanych już metod odzyskiwania energii.
Bezpośrednio po obróbce wstępnej prowadzone jest malowanie kataforetyczne elementów w wannie z tworzywa sztucznego o pojemności ok. 60 m³. W skład całego układu instalacji KTL wchodzi wanna do kataforetycznego malowania zanurzeniowego z urządzeniem do cyrkulacji farby, zespołem dializ, a ponadto prostownik i instalacja chłodząca lakier, instalacja ultrafiltrująca i dozownik lakieru oraz awaryjny zespół prądotwórczy. Wanna wyposażona jest w zespół anod b+m, a stosunek anod do katod wynosi 1:4. Instalacja daje możliwość ustawienia różnych programów powlekania. Zadana grubość powłoki wynosi średnio 40 do 45 µm.
Szczegółowe zdjęcie obszaru zbiornika na poziomie zerowym z centralną częścią orurowania.
Lakierowanie kataforetyczne elementów do 5 ton
Do transportu elementów na całym obszarze wanien wykorzystywanych jest pięć przesuwnic o obciążeniu maksymalnym do 5 ton każda. Ze względu na dużą wysokość podnoszenia (5 m), dla zwiększenia sztywności - a dzięki temu również dokładności pozycjonowania - zastosowano elementy naprowadzające w konstrukcji kratownicy. Szybkość podnoszenia można regulować bezstopniowo w zakresie 0-20 m/min przy pomocy przetwornicy częstotliwości.
Nośniki elementów przekazywane są w obszarze kąpieli przez przenośniki Power+Free na pokrywę ze zintegrowaną szyną jezdną. Pokrywa ta transportowana jest przez przesuwnicę do każdego z obszarów i ustawiana nad kąpielą bądź w obrębie wanny. Zawieszone na nośnikach elementy zanurzane są przy tym w odpowiedniej kapieli bądź natryskiwane odpowiednim „medium” przez pierścienie natryskowe. Po przejściu całego ciągu procesu nośnik przekazywany jest ponownie na przenośnik P+F i transportowany do suszarki. Suszarka wykonana została według typu konstrukcji A. Obie śluzy na wlocie i wylocie zapewniają zatem odpowiednią izolację cieplną w tunelu suszarki. Całkowita długość suszarki wynosi 40 m, natomiast szerokość aż 8,4 m. Suszenie odbywa się przy pomocy powietrza obiegowego o maksymalnej temperaturze 210°C. Czas suszenia wynosi 120 minut lub 18 taktów. Do czyszczenia (obróbki końcowej) powietrza wywiewanego wykorzystywana jest termiczna instalacja dopalająca (TNV) o przepustowości 4000 m³/h. Po wyjściu z tunelu suszarki elementy przechodzą przez strefę chłodzenia, a następnie w jednej z trzech stref załadowczo-odbiorczych wychodzą z systemu i przekazywane są do dalszej obróbki na montaż.