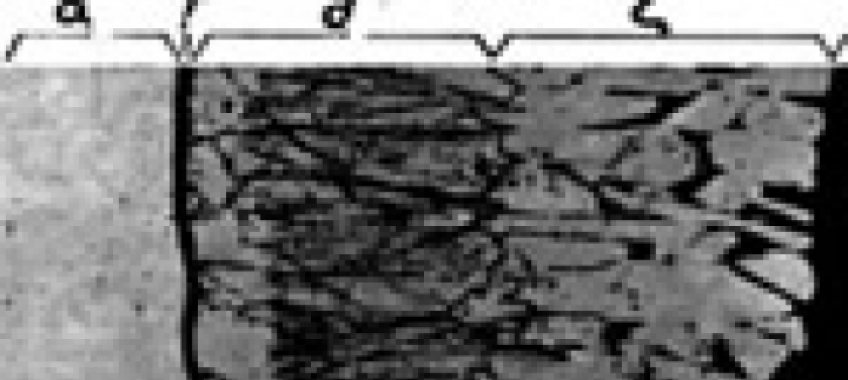
W pneumatycznej metodzie „omiatania” dla osłabienia energii kinetycznej zaleca się najczęściej stosowanie następujących parametrów obróbki omiatającej:
a - wielkość ziarna ściernego: 0,2 do 0,5 cm,
b - ciśnienie sprężonego powietrza wylatującego wraz z wylatującym ścierniwem z końcówki dyszy: 0,2 do 0,4 MPa (2-4 barów),
c - kąta nachylenia strumienia ściernego do powierzchni ocynkowanej: 30 do 60o,
d - długość strumienia ściernego: 0,4 do 0,5 m (odległość dyszy od powierzchni),
e - szybkie przesuwanie dyszy po powierzchni obrabianej, czyli krótki czas obróbki [2],
f - najczęściej proponuje się stosowanie dyszy typu Venturiego [2,3,4,5], a więc powodującej wzrost prędkości ziaren ściernych prawie dwukrotny w stosunku do dysz prostych i trzykrotny w stosunku do śrutowania wirnikowego z powodu większego uporządkowania śladów uderzeń ścierniwa w powierzchnię oczyszczaną, to jest nieskupianie ich w osi strumienia ściernego oraz zwiększenia pola rażenia przy tej samej średnicy dyszy [9]. Wielkości dyszy nie podaję, gdyż zależy ona od zastosowanej wielkości ziarna ściernego (minimum 5 razy większa od największego ziarna) [9]. W opisach zaleceń procesu omiatania ani w pracach badawczych nikt nie rozważał wpływu ciężaru właściwego na energię cząstki ścierniwa. Śruty posiadają ciężar właściwy (7,4 do 7,8 g/cm3), a więc prawie dwukrotnie wyższy od najcięższego ścierniwa niemetalowego (elektrokorund i garnet po ~ 4 g/cm3, żużel pomiedziowy ~3,3 g/cm3).
Ek = m ∙ v2/2
oraz pędu ścierniwa
P = m ∙ v
Wynika z powyższego, że wielkość ziarna ściernego i jego ciężar właściwy mają bezpośredni wpływ na siłę uderzenia ziarna ścierniwa w obrabianą powierzchnię ocynkowaną. Należy spodziewać się najmniej dwukrotnie większej wartości energii kinetycznej i wartości pędu śrutów niż elektrokorundu lub granatu almandynowego (garnetu), a kulek szklanych, żużli odpadowych i piasku jeszcze o wiele mniejszej (patrz na tablicę 1). Śrut staliwny ma naturalnie wyraźnie mniejszą wielkość ziaren niż ścierniwa mineralne. Wielkość ziaren śrutu zmienia się przy omiataniu niewiele, dlatego śrut staliwny nadaje się jako ścierniwo wielokrotnego użytku. Mniejsze cząstki powodują jednak mniejszą chropowatość powierzchni. Większa zawartość ziarna grubego w elektrokorundzie i jego większa skrawalność powodują większą głębokość szorstkości i wymaga ostrożniejszego jego stosowania (należy zastosować mniejsze ziarno, zmniejszać ciśnienie i szybciej omiatać) [1]. Słabo jest też podkreślana sprawa kształtu ziaren ściernych oraz posiadanie lub nie ostrych krawędzi i naroży tnących powiązanych z ich trwałością, jak też właściwości niestępiania się ich oraz tendencji do powstawania nowych ostrych krawędzi i naroży ziaren rozbitych. Ostre krawędzie i naroża powodują znacznie większe rozwinięcie powierzchni cynku, a więc i znacznie powiększają powierzchnie styku lakierów ciekłych i proszkowych oraz ułatwiają mechaniczne zakotwienie się ich, przyczyniając się do wzrostu siły przyczepności powłoki lakierowej do podłoża, a zatem i trwałości systemu duplex [10].