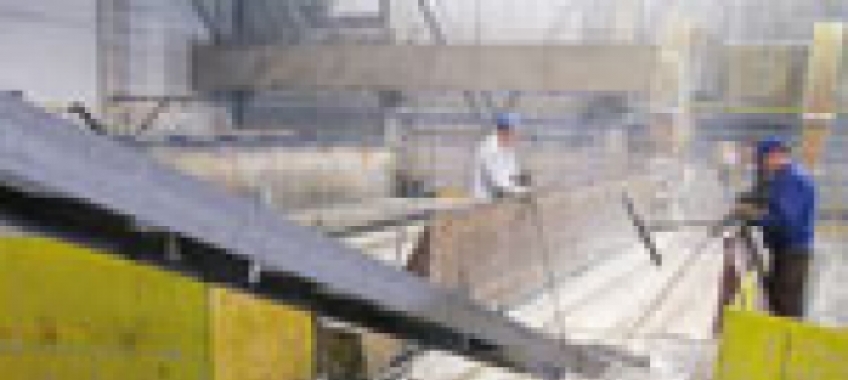
Struktura powłok cynkowych otrzymanych metodą jednostkową i ciągłą
Dużą różnicę pomiędzy opisanymi powyżej metodami cynkowania można zaobserwować w budowie powłoki ochronnej. Mikrostrukturę klasycznej powłoki cynkowej uzyskanej metodą jednostkowego zanurzania przedstawiono na rys. 5. Posiada ona budowę warstwową: bezpośrednio na powierzchni stali widoczna jest cienka warstwa faz Γ/Γ1 następnie znajduje się zwarta warstwa δ1 oraz strefowa i niejednorodna ζ. Nad warstwą przejściową występuje zewnętrzna warstwa cynku h. Dla porównania, mikrostrukturę powłoki cynkowej wytworzonej metodą ciągłą według procesu Sędzimira przedstawiono na rys. 6. Powłoka w tym przypadku składa się praktycznie z warstwy cynku z dodatkami żelaza i aluminium. W obu przypadkach powłoki są ciągłe i pozbawione pęknięć oraz posiadają odpowiednią dla warstw dyfuzyjnych adhezję do podłoża. Na podstawie badań można stwierdzić, że najbardziej istotną różnicę pomiędzy powłokami cynkowymi otrzymanymi metodą jednostkowego i ciągłego zanurzania stanowi całkowita grubość powłoki oraz udział w niej warstwy przejściowej (zbudowanej z faz międzymetalicznych Fe-Zn). W przypadku metody jednostkowej uzyskano powłoki o grubości średniej 80-85 μm, gdy w metodzie ciągłej grubość powłoki wynosi ok. 20-25 μm. Mniejsza grubość powłoki nie jest korzystna ze względu na niższą odporność korozyjną, jednak pozwala na trwałe łączenie blach, np. poprzez zgrzewanie. W powłoce wytwarzanej metodą ciągłą jest również dużo mniejszy udział twardej i kruchej warstwy przejściowej, której grubość wynosi zaledwie 1-2 μm. Ma to znaczenie dla przeróbki plastycznej blach z powłoką, co często jest wykorzystywane w różnych aplikacjach. Przy wysokiej zawartości aluminium w kąpieli oraz dużej prędkości metalizacji, warstwa przejściowa może być jeszcze cieńsza, wręcz niewidoczna na obrazie mikroskopowym. Powiększenie 10 000× uzyskane przy zastosowaniu mikroskopu skaningowego Hitachi S-3400 wyposażonego w spektrometr rentgenowski z dyspersją energii pozwoliło na zaobserwowanie 1μm warstwy przejściowej, choć sam obraz nie jest ostry (rys. 6).
Podsumowanie
Cynkowanie zanurzeniowe zarówno metodą ciągłą, jak i jednostkowego zanurzania jest stosowane od wielu lat. Obie odmiany technologii uzupełniają się ze względu na możliwość stosowania ich do zabezpieczania korozyjnego bardzo szerokiego asortymentu różnorodnych półwyrobów i wyrobów stalowych. W wyniku cynkowania wytwarzana jest powłoka ochronna o bardzo korzystnym stosunku trwałości do kosztów wytwarzania. Powłoki cynkowe otrzymane w obu procesach stanowią podłoże do malowania o podobnej charakterystyce. Różne metody aplikacji powłoki lakierowej wynikają bardziej z kształtu wyrobów, na których wytwarzane są systemy duplex, aniżeli z właściwości powierzchniowych powłoki cynkowej. Blacha ocynkowana metodą ciągłą jest często malowana na walcach. Urządzenia do powlekania na walcach tworzą linię technologiczną o długości średnio 150-200 m, przy długości wstęgi blachy równej ok. 300 m. Linia składa się z wielu elementów (głównie mechanicznych) służących do prowadzenia procesu: w początkowej części linii występuje wielostopniowy agregat do wstępnej obróbki powierzchniowej (odtłuszczanie, płukanie, chemiczne przygotowanie przez nałożenie międzywarstwy konwersyjnej). Dalsze operacje są zależnie od rodzaju stosowanych materiałów powłokowych i metody powlekania. Obejmują one nakładanie farby podkładowej na walcach, suszenie, nakładanie właściwego powłoki lakierowej lub laminowanie blachy folią organiczną oraz ponowne suszenie lub żelowanie powłoki. W końcowej części linii prowadzi się obróbkę wykańczającą (nadruk lub tłoczenie deseniowe, nakładanie usuwalnej warstwy ochronnej). Linię kończy urządzenie do cięcia i profilowania.