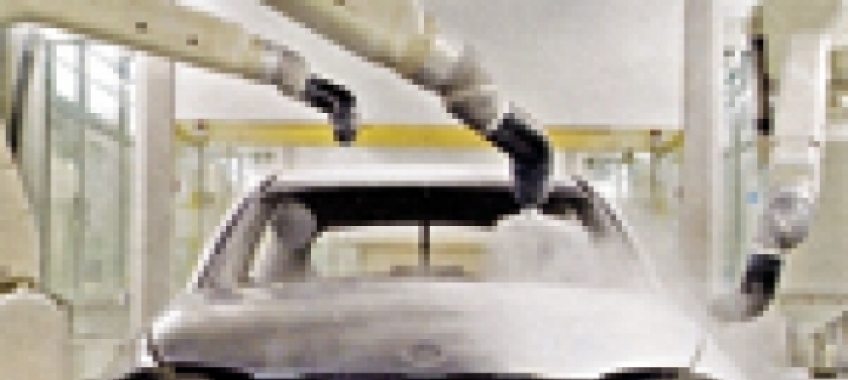
Szybka komunikacja
Kolejnym czynnikiem mogącym powodować opóźnienia jest obciążenie sterownika PLC innymi procesami komunikacyjnymi. Pomysł jaki mieli Manfred Bachhuber, planista struktury lakierni, oraz jego koledzy, to przekazywanie zmieniających się danych, natychmiast do wizualizacji. Zwiększyło to wielokrotnie szybkość aktualizacji. Jednocześnie przesyłana jest mniejsza ilość danych odciążając tym samym cały system. W tym celu sterownik PLC oraz oprogramowanie do wizualizacji komunikują się poprzez uzgodniony blok danych. Do komunikacji nie jest konieczna konfiguracja połączenia przez procesor komunikacyjny. Ponieważ dane przesyłane są asynchronicznie do cyklu pracy sterownika PLC, do koordynacji kazdorazowo używany jest tzw. bit „handshake”. Podczas tworzenia wizualizacji sterownik urządzenia przekazuje do sterownika PLC informację jakie zmienne są wymagane, a jakie już nie, a PLC zarządza listą wszystkich aktualnie zarejestrowanych zmiennych. Przy rejestracji zmiennej przekazywana jest również informacja o tym czy jest to blok danych, flaga, wejście lub wyjście, a także informacja o adresie oraz wielkości danych. Czas aktualizacji wizualizacji procesu obróbki powierzchni jaki osiągnięto w BMW Ratyzbona mieści się w przedziale od 100 do 200 milisekund przy ponad 20 000 zmiennych. – Firma Copa-Data była bardzo otwarta na nasze pomysły i nasza koncepcja została przyjęta z wielkim zainteresowaniem – dodaje Manfred Bachhuber, który w zakresie planowania struktury lakierni w fabryce BMW w Ratyzbonie odpowiedzialny jest głównie za systemy sterowania. – Dzięki intensywnym dyskusjom mogliśmy stworzyć system, w którym wszystkie elementy doskonale ze sobą współpracują.
Tłumaczenie z „Besser Lackieren!”
Michał Bedyk
nr 1/2011, str. 10-11