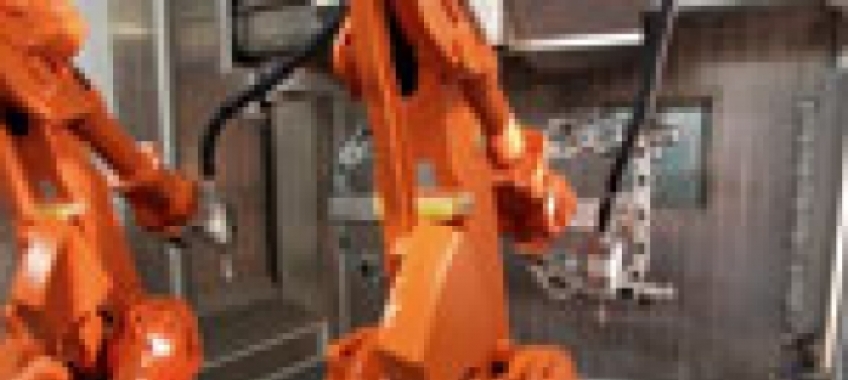
Podniesienie jakości oczyszczania powierzchni możliwe jest również dzięki zastosowaniu kombinacji użycia modułu destylacji czystej oraz destylacji kąpieli zużytej. Środek myjący jest w sposób nieprzerwany destylowany we wspomnianych modułach, zaś zebrane frakcje oleiste są natychmiast wyprowadzane poza układ. Cząstki stałe są wychwytywane przez układ filtracyjny, przez który to kąpiel myjąca jest przepompowywana przed wydostaniem się w strefę natrysku. Pierścienie synchronizatorów o średnicy od 67,5 do 172 mm są transportowane przez ten sam układ zawiesi. Każdy z koszy, do których wkładane są pierścienie, może być zapakowany na wiele sposobów, dzięki czemu można w nich umieścić różne wymiary detali. Wymiary koszy to 670x480x300 mm.
Oszczędności związane z upakowaniem detali
Rezultat końcowy, czas trwania procesu oraz koszty operacji oczyszczania pakietów detali zależą od umiejscowienia detali wewnątrz koszy transportowych. Ma to również wpływ na proces utylizacji kąpieli, jak i zużycie środka myjącego. Wykonanie kosza z drutu o owalnych kształtach sprawia, iż myty detal ma kontakt z kąpielą z każdej strony, zmyte frakcje zanieczyszczeń są natychmiast usuwane, a co najważniejsze, do całego procesu zużywana jest znacznie mniejsza ilość środków chemicznych. To wszystko prowadzi do jeszcze lepszych wyników oczyszczania w krótszym okresie, co z kolei przekłada się na większą wydajność całej linii oraz dłuższy okres działania kąpieli. Obok poprawy działania środków myjących oraz technologii procesu, to właśnie odpowiednie zaprojektowanie kosza myjącego daje ten właściwy ostateczny rezultat. Jego kształt powinien zapewniać taki rodzaj upakowania, przy którym wymagana jest minimalna ilość operacji ręcznych. Zmniejsza to w znaczny sposób ryzyko uszkodzenia detali podczas całego procesu technologicznego i ponownie wpływa na zmniejszenie kosztów produkcji. Właściwe umiejscowienie detali jest również kluczowe dla wielu producentów części samochodowych. Jeden z przedsiębiorców produkujący dwa rodzaje komponentów musi za jednym razem poddać obróbce pakiety elementów kolejno po 96 i 46 sztuk. Komponent A jest zewnętrzną częścią w stosunku do komponentu B. Dla w pełni zautomatyzowanego procesu montażu 48 sztuk komponentu A i B musi być umieszczone na odpowiedniej zawieszce tak, aby całość została poddana obróbce chemicznej. To właśnie dzięki specjalnemu projektowi przenośnika elementy mogą być w łatwy sposób umyte i zdjęte do dalszego procesu przetwarzania. Dla zminimalizowania operacji przekładania detali został zamontowany specjalny mechanizm odwracający przenośnik z załadowanymi detalami. Dzieje się tak zarówno z upakowanym modułem 96 elementów A, który na potrzeby modułu obracającego jest dzielony na dwie części, jak i 48 elementami komponentu B. Połowa ładunku elementów A oraz cała ilość elementu B jest pakowana na ramkę, która następnie obracana jest do góry nogami w przenośniku. Dzięki temu pomysłowemu rozwiązaniu do załadowania przenośników wystarcza jedynie 5 manualnych czynności (obrócenie komponentu A i B w adapterze, podzielenie ilości komponentu A na pół, umieszczenie adapterów w ramkach oraz przekręcenie ich o 180 st. w przenośniku). Rozwiązanie to pozwoliło na redukcję nakładów pracy na tym odcinku produkcji o 75 proc.