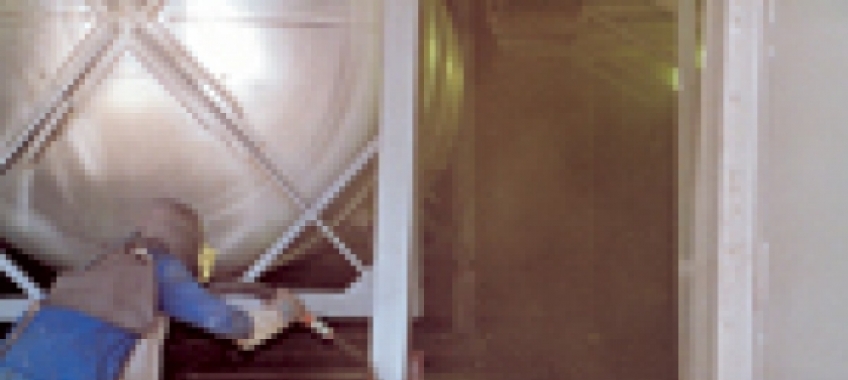
Wysoka trwałość ścierniwa, mniejsze zużycie elementów maszyny
porównaniu do ścierniwa mineralnego, śrut ze stali nierdzewnej ulega znacznie mniejszemu zużyciu. Jego zastosowanie powoduje wyraźny spadek zapylenia, co pociąga za sobą mniejsze koszty utylizacji. Ścierniwo nierdzewne wywiera także pozytywny wpływ na zużywanie się części urządzenia śrutującego.
Ścierniwo mineralne jest najwyższym stopniu kruche łamie się podczas każdego wyrzutu na obrabiany element. Jego przeciwieństwem jest ostrokrawędziowy śrut ze stali nierdzewnej Grittal firmy Vulkan Inox, który jest bardzo wytrzymały rozłamuje się dopiero po wielu cyklach. Dzięki temu można uzyskać znacznie mniejsze zużycie ścierniwa.
Dobrym tego przykładem okazała się obróbka strumieniowa kontenerów, gdzie przy jednakowych parametrach pracy udało się zredukować zużycie medium 900 ton korundu do 30 ton śrutu nierdzewnego ciągu roku. Odpowiada to czynnikowi zużycia ścierniwa stosunku 30:1.
Poprawa stabilności procesu
Kruchość oraz szybkie rozdrabnianie się ścierniwa mineralnego powoduje gwałtowne zmniejszenie się wielkości ziaren. następstwie zużyte ziarna są błyskawicznie eliminowane procesu. Natomiast przypadku ziaren śrutu nierdzewnego zachowują one swój kształt oraz wielkość na bardzo długi czas. Ścieranie się pojedynczych ziaren następuje jedynie stopniowo. Stąd też rozkład ziaren roboczej mieszance ścierniwa jest bardzo trwały, sam proces śrutowania daje się łatwiej kontrolować. Wydajność oraz wynik śrutowania są całkowicie stabilne, co objawia się na przykład uzyskiwaniu stałych wartości chropowatości oraz jednorodnego wyglądu śrutowanych powierzchni.
Znikome zapylenie podczas śrutowania
Wysoka trwałość śrutu nierdzewnego prowadzi do bezpośredniego zredukowania zapylenia podczas śrutowania. Każde ścierniwo staje się ostatecznie pyłem. Jednak porównaniu do ścierniwa mineralnego wydłużona 30-krotnie żywotność powoduje, że powstająca ilość pyłu zmniejsza się jednakowym stopniu. To odpowiada redukcji zapylenia wynoszącej do poziomu 3% początkowej ilości pyłu. Te niemal bezpyłowe warunki pracy skutkują lepszą widocznością kabinie śrutowniczej, tym samym krótszymi czasami obróbki strumieniowej. Już podczas śrutowania można dokonać oceny czystości obrabianej powierzchni detalu. Dodatkowa kontrola oraz doczyszczanie ograniczają się do minimum. Pył ze ścierniwa mineralnego jest najwyższym stopniu abrazyjny prowadzi do znacznego zużycia maszyny, szczególności dysz oraz węży śrutowniczych. Wskutek tak niezwykle niskiego zapylenia, podczas śrutowania użyciem śrutu nierdzewnego żywotność dysz oraz węży zwiększa się niemal trzykrotnie.