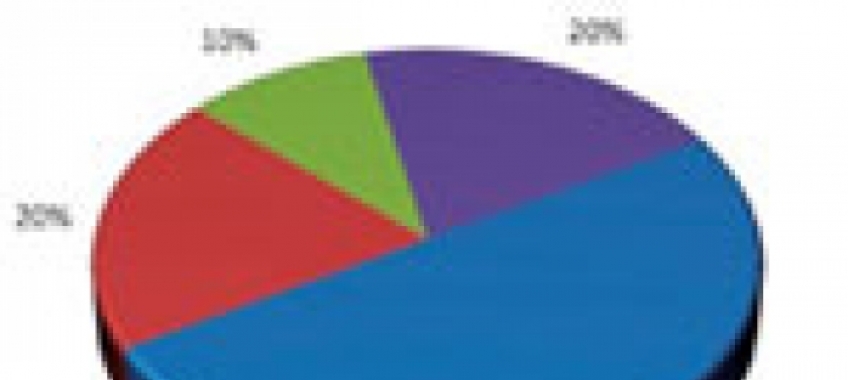
Koszty wytwarzania systemów ochronnych
Rachunek porównawczy kosztów jest zasadny, gdy nie ma wątpliwości, że inwestycja powinna być podjęta i rozpatrywane alternatywy są na tyle podobne, że przy ich porównaniu można ograniczyć się do wielkości związanych z nimi kosztów. W przypadku zastosowania systemów ochronnych wytwarzanych różnymi technologiami istnieje takie podobieństwo struktury kosztów wytwarzania, co przedstawiono na rys. 1. Koszty aplikacji oraz ich strukturę dla cynkowania zanurzeniowego, natrysku cieplnego oraz malowania uzyskano od wytwórców zastrzegających swoją anonimowość w ramach wykonanej dyplomowej pracy magisterskiej. [1] Podstawowe koszty wytwarzania systemów ochronnych wynikają z kosztów materiałów i energii, amortyzacji urządzeń, kosztów osobowych itp. i są ponoszone podczas wykonania zabezpieczenia antykorozyjnego. Przybliżone koszty uzyskania 1 m2 powierzchni powłok cynkowych otrzymanych różnymi metodami przedstawiono na rys. 2. Najtańsze pod względem wykonawstwa są 1-powłokowe systemy malarskie oraz zanurzeniowe powłoki cynkowe. Cena wytworzenia powłok duplex w układzie zanurzeniowa powłoka cynkowa/powłoka organiczna ma wartość pośrednią, zaś najdroższe jest wytwarzanie powłok cynkowych technologią natrysku cieplnego i dodatkowo uszczelniane materiałami organicznymi.
Eksploatacja systemów ochronnych
Oprócz kosztów aplikacji, podstawowym czynnikiem wpływającym na optymalny wybór systemu ochronnego jest trwałość podczas eksploatacji w warunkach korozyjnych, a tym samym jego zdolność do zabezpieczania wyrobu przed zniszczeniem na skutek korozji. W praktyce stosowania cynkowych systemów ochronnych najczęściej spotykanym środowiskiem korozyjnym jest średnio agresywna atmosfera o kategorii korozyjności C3 zgodnie z PN-EN ISO 12944-2 [2]. Warunki tego typu występują w atmosferze miejskiej i przemysłowej, średnio zanieczyszczonej dwutlenkiem siarki oraz na obszarach przybrzeżnych o małym zasoleniu. Występują również wewnątrz pomieszczeń produkcyjnych o dużej wilgotności i zanieczyszczeniu powietrza, np. w halach zakładów spożywczych, pralni, browarów, czy mleczarni. Roczny ubytek grubości stali niskowęglowej w przemysłowym środowisku korozyjnym wynosi w przybliżeniu 25-50 μm, zaś cynku 0,7-2,1 μm [2]. Systemy ochronne zawierające cynk wytwarzane różnymi metodami posiadają różną grubość i różne właściwości. W opisanym powyżej środowisku korozyjnym będą więc miały różną długość zakładanego okresu użytkowania (Service Life). Jako okres użytkowania powłoki przyjmuje się czas do wystąpienia na jej powierzchni obszarów 5-10% śladów korozji stali. Przewidywany czas skutecznej ochrony antykorozyjnej systemów ochronnych zawierających cynk wytworzonych za pomocą różnych technologii w środowisku przemysłowym o klasie korozyjnej C3 przedstawiono w tab. 1. Najkrótszy zakładany okres użytkowania przewidziany jest dla systemów malarskich, pośredni dla metalizacji zanurzeniowej i natryskowej, zaś zdecydowanie największą trwałość wykazują powłoki duplex. Połączenie właściwości powłoki cynkowej oraz powłoki lakierowej pozwala na znaczne wydłużenie okresu eksploatacji. Dzięki dodatkowemu zastosowaniu powłok organicznych na ocynkowanych powierzchniach blach i konstrukcjach stalowych następuje radykalne zmniejszenie szybkości degradacji powłok cynkowych w środowisku korozyjnym. Powłoki duplex traktowane sumarycznie są 1,5 od 2,3 razy trwalsze niż powłoki cynkowe i lakierowe występujące osobno w danych warunkach korozyjnych [4]. Przykładowo, jeżeli w warunkach przemysłowego środowiska korozyjnego powłoka cynkowa będzie zabezpieczać podłoże stali przez 33 lata, poliuretanowa powłoka lakierowa 17 lat, to zastosowanie systemu kompleksowej ochrony pozwoli na użytkowanie pokrycia przez ok. 70 lat bez konserwacji, min. 1,5 raza dłużej niż podczas stosowania systemów ochronnych osobno.