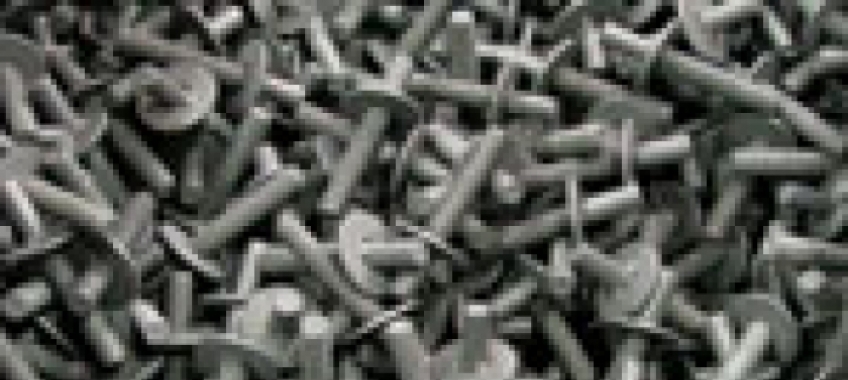
- równomierna i jednorodna na całej powierzchni oraz powtarzalna grubość warstwy cynkowej (również na powierzchniach wewnętrznych) w zakresie od 20 do 120 µm,
- całkowity brak toksycznych odpadów (proces bezchromowy).
Przebieg procesu obróbkowego jest zgodny z następującymi normami:
- ASTM A 1059A/ 1059M - 08
- EN 13811:2003
- Russian standard GOST R 9.316-2006
- Israeli standard 4271
Zalety technologii DISTEK
Przedstawione powyżej cechy charakterystyczne technologii cynkowania termodyfuzyjnego DISTEK decydują o zaletach tej technologii. Do nich należą m.in.:
- prowadzenie procesu pasywacji przy zastosowaniu nietoksycznych środków;
- całkowity brak toksycznych odpadów poprocesowych, co powoduje, że technologia DISTEK jest absolutnie przyjazna dla środowiska;
- uproszczenie procesu technologicznego dzięki możliwości rezygnacji z kosztownej i czasochłonnej obróbki wstępnej (części lekko zaolejone lub skorodowane nie wymagają poddawania ich specjalnej obróbce przed procesem cynkowania);
- uzyskiwanie bardzo wysokiej odporności antykorozyjnej (nawet do 1500 godzin w komorze solnej);
- uzyskiwanie twardej powierzchni zapewniającej dobrą odporność na ścieranie;
- uzyskiwanie powtarzalnej warstwy cynku o grubości od 20 do 120 µm, o wysokiej jednorodności struktury, równomiernej na całej powierzchni;
- brak narostów cynkowych na krawędziach (bardzo ważne w przypadku połączeń gwintowych);
- uzyskiwanie doskonałej przyczepności powierzchni w odniesieniu do nakładanych powłok lakierniczych i wulkanizacyjnych;
- zachowanie właściwości mechanicznych cynkowanych części z uwagi na stosunkowo niską temperaturę prowadzenia procesu (możliwość pokrywania części specjalnych, takich jak np. śruby i niektóre sprężyny);
Ograniczenia technologii DISTEK
Omawiając liczne zalety technologii cynkowania termodyfuzyjnego należy też wspomnieć o jej ograniczeniach. Wymiary obrabianych przedmiotów warunkowane są wymiarami pojemników roboczych, proces cynkowania termodyfuzyjnego jest procesem ekonomicznym głównie w odniesieniu do części małych i średnich. Maksymalne ich wymiary wynosić mogą 400 mm, mierząc po przekątnej bryły geometrycznej. Możliwa jest również obróbka długich przedmiotów (rury, pręty) nawet do długości 12.000 mm, jednak odbywa się ona przy zastosowaniu specjalnych linii obróbkowych lub kosztem wydajności linii standardowych.