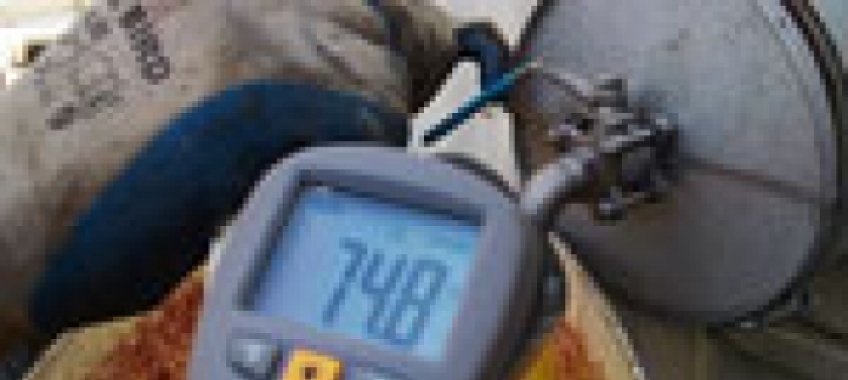
Przypadek II - klimatyzowana hala
W hali, o której mowa, była zaplanowana specjalistyczna, w znacznym stopniu zautomatyzowana produkcja, dlatego środowisko wewnątrz hali musiało mieć zapewnioną stałą temperaturę około 22°C i stabilną wilgotność na poziomie 50 do 65% wilgotności względnej. Takie środowisko to C1 w świetle normy PN-EN ISO 12944 cz. 2. Projektant obiektu przyjął w projekcie środowisko C2 i zalecił malowanie konstrukcji przygotowanej do stopnia Sa 2?, zgodnie z PN-EN ISO 8501-1, farbami epoksydowymi na grubość 80 ?m. Z formalnego punktu widzenia można dyskutować czy założenie środowiska C2 zamiast C1 było błędem. Moim zdaniem nie, gdyż norma PN-EN ISO 12944 cz. 5 nie stawia żadnych wymagań co do zabezpieczeń dla kategorii korozyjności C1, zaleca jedynie zastosowanie zestawu farb przewidzianego dla tzw. okresu krótkiego dla kategorii korozyjności C2. Dobrane zabezpieczenie z merytorycznego punktu widzenia było więc jak najbardziej prawidłowe. W tym miejscu warto przypomnieć, że środowisko C1 w przypadku nowo budowanych obiektów nie istnieje. Konstrukcja przez okres budowy będzie narażona na środowisko co najmniej C2 i projektant powinien uwzględniać nie tylko środowisko założonej eksploatacji, ale również wszystkie narażenia w procesie wytwarzania, transportu i montażu konstrukcji, aż do momentu uzyskania warunków docelowych. Konstrukcja była wytwarzana i malowana w dość typowej, na polskie warunki, wytwórni. W nieogrzewanych halach malowano w okresie późnojesiennym farbami epoksydowymi, które powinny być aplikowane w temperaturach nie niższych niż +10°C. Z malowania sporządzona była nawet dokumentacja, w której odnotowywano, że malowano w temperaturze +7°C przy wilgotności względnej ponad 80%. Odnotowano też grubości, które wynosiły od 45 do 150 ?m. Były to wyniki pomiarów odczytywane bezpośrednio z przyrządu bez uwzględnienia poprawki na chropowatość. Nie wiem po co była sporządzana ta dokumentacja, skoro kontrola jakości z niej nie korzystała i wypuszczała tak pomalowane elementy na budowę.
Wszystkie braki dały o sobie znać w dwóch etapach. Pierwsze skutki złego wykonawstwa pojawiły się po okresie transportu i składowaniu na placu budowy, kiedy przystąpiono do montażu konstrukcji. Była to lokalna korozja w miejscach przecienień oraz żółknięcie powłok w wyniku utwardzania w nieodpowiednich warunkach (niskie temperatury i wysoka wilgotność). Kiedy pierwszy raz oglądałem tę konstrukcję, część powłok można było łatwo zetrzeć metyloetyloketonem (MEK), chociaż były to epoksydy (fot. 2). Po ujawnieniu tych wad wykonano szybko i dość niestarannie poprawki (fot. 3). Jako drugi etap można uznać usterki, które pojawiły się już po obudowaniu konstrukcji, w okresie dużej kondensacji wilgoci podczas wylewania posadzek. Wtedy przeważająca część konstrukcji pokryła się produktami korozji (fot. 4) i trzeba ją było oczyścić i ponownie pomalować. Jakie wnioski można wyciągnąć z tej reklamacji? Zawsze namawiam wykonawców do sporządzania rzetelnej dokumentacji z prowadzonych prac, bo taka dokumentacja jest mocnym argumentem potwierdzającym jakość. Niestety, jeżeli jakość prac jest marna, sama dokumentacja sprawy nie załatwi. Wspomniany wykonawca był na tyle uczciwy, że odnotował w dokumentacji generowane przez siebie błędy, ale nie o to przecież chodzi. To kontrola jakości widząc, że malowanie odbywa się w niewłaściwych warunkach powinna zareagować.