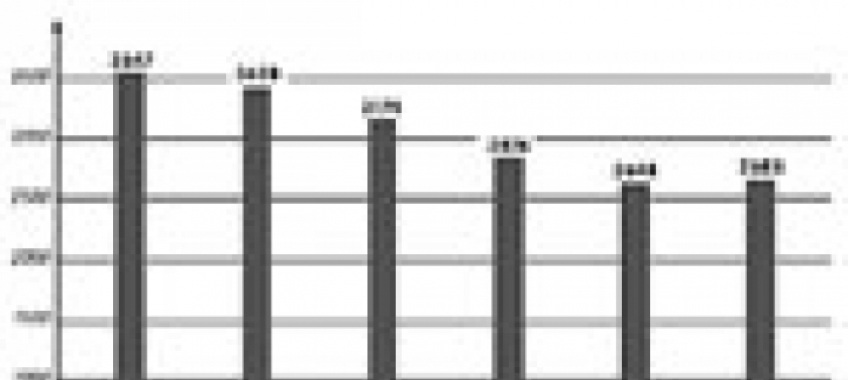
- Wpływ ciężaru właściwego śrutów
Należy pamiętać, że ciężar właściwy ma wprost proporcjonalny wpływ na siłę uderzenia śrutu w powierzchnię obrabianą strumieniowo-ściernie.
- Wpływ wielkości ziarna śrutu na jego trwałość
Wielkość ziarna ściernego ma decydujący wpływ na energię ziarna ściernego. Wyniki doświadczalne pokazują, że zmniejszenie rozmiaru ziarna śrutu powoduje wyraźne przedłużenie czasu życia ścierniwa w cyklu Ervina.
- Prędkość uderzenia śrutu w powierzchnię obrabianą
Głównym parametrem kinematycznym rozdrabniania jest, obok wielkości ziarna, prędkość uderzenia w powierzchnię obrabianą. Cząstka śrutu uderzając w stałą powierzchnię generuje naprężenia nie tylko na powierzchni docelowej, ale również cząstki ściernej. Istnieje prawdopodobieństwo, że ziarna uderzającego śrutu mogą ulec złamaniu w czasie tego zderzenia. Prawdopodobieństwo złamania ziarna w dużej mierze zależy od prędkości zderzenia, kąta uderzenia i średnicy cząstki śrutu. Prawdopodobieństwo pęknięcia zwiększa się ze wzrostem szybkości uderzenia oraz zwiększeniem kąta uderzenia. Można zauważyć, że prędkość progowa była dość niska w przypadku materiałów docelowych o wysokiej twardości. Wpływ twardości docelowej na wpływ oddziaływania śrutu badał G. Calboreanu. Porównawcze badanie degradacji śrutu okrągłego S-460 ze względu na twardość celu przeprowadzono wpływ na uderzenie w płytkę białego i szarego żeliwa w maszynie do badania laboratoryjnego w maszynie produkcji WTB6. Twardość płytki białego żeliwa wynosiła 65 HRC, natomiast szarego 22 HRC. Wykonano łącznie 500 uderzeń (cykli) w ciągu trzech eksperymentów i badano próbki co ??50 uderzeń. Uszkodzenia śrutu analizowano poprzez pomiar degradacji wielkości ziaren ściernych i ich kształtu. Przy prędkości VP = 70 m/s następuje zmiana kształtu śrutu z ciętego drutu stalowego do kształtu prawie kulistego po około 150 cyklach oddziaływania, a przy 200 m/s dużo szybciej. Cleaver i Ghadiri sugerują zmniejszony wpływ na fragmentację cząstek o mniejszej twardości, mniejszej gęstości, większej odporności na pękanie i dolnej średnicy cząstek.
W przypadku twardej powierzchni docelowej zauważa się wzrost odkształcania cząstek śrutu, a głównym mechanizmem podziału jest poprzez rozszerzanie wewnętrznych pęknięć rdzenia śrutu. Natomiast wpływ miękkiej powierzchni docelowej daje małe peryferyjne pęknięcia promieniowe (50-100 µm długości). Śrut wpływa na bardziej miękką powierzchnię wtedy, gdy ma większą ilość ostrych krawędzi i naroży. W tym szczególnym przypadku erozji śrutów, twardość materiału ściernego oraz kształt cząstek najbardziej wpływa na proces erozji śrutu. Przy twardszych materiałach podłoża i twardości śrutów były dominującym czynnikiem degradacji śrutów; podczas gdy przy obróbce miękkich materiałów kształt ostrokrawędziowy cząstki śrutu był najważniejszy.