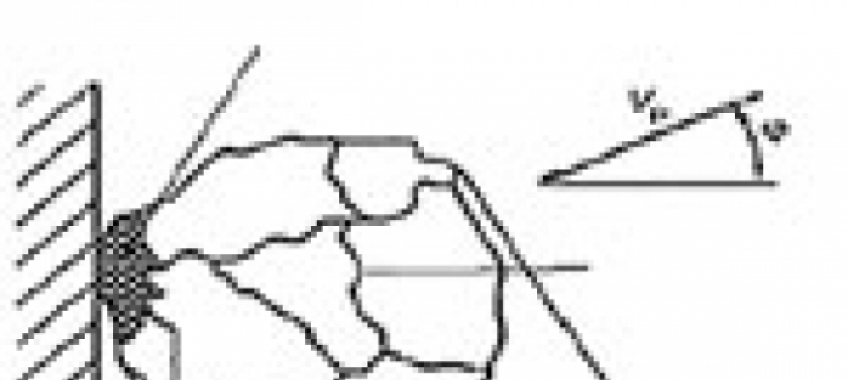
Struktura i właściwości mechaniczne materiału podłoża wpływają na proces formowania jego topografii. Wpływ ten przedstawia np. tabela 1, w której można zauważyć, że walcowana na gorąco stal uzyskuje większą chropowatość w porównaniu ze stalą walcowaną na zimno.
Zbadano trzy chropowatości podłoża metalowego oczyszczone różnymi ścierniwami i ustalono, że chropowatość jest zawsze najwyższa dla zwykłej stali budowlanej, a następnie stopu aluminium i stali chromowo-niklowej. Ustalono natomiast niemal odwrotne relacje liniowe pomiędzy średnią chropowatością powierzchni metalowych oczyszczonych i wartością modułu Younga: wyższy moduł Younga, to niższe wartości chropowatości. Efekt ten obserwowali również ci, którzy obrabiali strumieniowo inne podłoża metalowe cząsteczkami tlenku glinu (elektrokorundu).
Jeżeli stosunek twardości ziaren ściernych przekraczał wartość Hp/Hu = 3, występowało dalsze zwiększanie chropowatości podłoża. Przeprowadzone testy obróbki strumieniowo-ściernej próbek ze stali za pomocą cząstek elektrokorundu wykazały, że niższa twardość podłoża promuje wyższe wartości chropowatości (Ra).
Śrutowanie żeliwnym śrutem próbek stalowych wykazało wpływ odległości oddalenia wylotu ścierniwa z dyszy od podłoża na skutki zmian chropowatości docelowego materiału. Szorstkość (Rz) była wyższa dla podłoży aluminiowych w porównaniu do podłoży miedzianych przy niskich odległościach dyszy od podłoża, tendencja była zaś odwrotna w przypadku większych odległości.
Wykres 2. Zmiany mikrotwardości z powodu obróbki strumieniowej. 1 - stal nierdzewna 430, 2 - stal nierdzewna 304, 3 - stal nierdzewna kortenowska, 4 - mosiądz, 5 - aluminium 6063 Al.