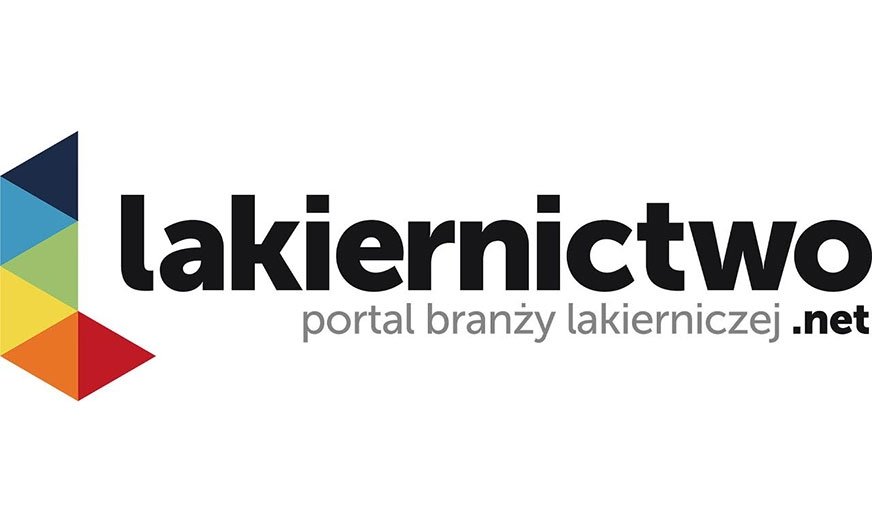
zabezpieczenie miejsc, gdzie usunięta lub zniszczona została powłoka cynkowa
- czyszczenia powierzchni po montażu
czyszczenie elementów cienkościennych
czyszczenie elementów ze stali nierdzewnych [3].
* Oczekiwane trwałości powłok i kategorie korozyjności podano w kontekście EN ISO 12944
Załącznik „F” do EN 1090–2 precyzuje wymagania i wytyczne dotyczące wykonania zabezpieczeń antykorozyjnych konstrukcji stalowych (bez uwzględnienia stali nierdzewnych). Omawia sposoby przygotowania i zabezpieczenia powierzchni za pomocą powłok malarskich oraz powłok metalowych (natryskiwanych cieplnie lub uzyskiwanych poprzez cynkowanie ogniowe). Znajdujemy w nim wyraźne zalecenie, by wymagania związane z zabezpieczeniem antykorozyjnym określone były w specyfikacji wykonawczej, w formie specyfikacji eksploatacyjnej lub w formie wymagań technologicznych dla zastosowanego systemu ochrony. W zakresie specyfikacji odnosi się do norm: EN ISO 12944–8 dla zabezpieczenia poprzez powłoki malarskie; EN ISO 1461, EN ISO 14713–1, –2 dla zabezpieczeń poprzez cynkowanie ogniowe; EN 13438 i EN 15773 w zakresie malowania proszkowego stali ocynkowanych ogniowo [3].
W zakresie warunków prowadzenia prac wymaganiem jest, by zabezpieczenie antykorozyjne było wykonane zgodnie z opracowanymi instrukcjami roboczymi. Instrukcje te powinny jednoznacznie odnosić się do działań, które należy wykonać przed i po zakończeniu procesu wytwarzania. W działaniach tych należy uwzględnić między innymi: stosowanie wyrobów do zabezpieczenia antykorozyjnego zgodnie z zaleceniami ich producenta; procedury przechowywania i wydawania materiałów zapewniające stosowanie materiałów w okresie ich ważności oraz w okresie ich przydatności po otwarciu pojemnika lub zmiksowaniu; sposoby postępowania zapobiegające powstawaniu uszkodzeń podczas przenoszenia, składowania i transportu; warunki środowiskowe zapewniające właściwe schnięcie powłok malarskich oraz pozwalające uniknąć korozji powłok metalowych; procedury naprawy uszkodzeń zabezpieczeń antykorozyjnych.
W zakresie przygotowania powierzchni w załączniku F znajdujemy odniesienie do opisanych wcześniej wymagań zawartych w punktach 10.2 oraz 12.6 EN 1090–2. Znajdujemy w nich wymaganie kontroli konstrukcji przed rozpoczęciem prac antykorozyjnych. Wszystkie powierzchnie spoiny i brzegi należy skontrolować wizualnie na zgodność z wymaganiami. Jakość powierzchni stalowych, na które będą nakładane powłoki organiczne, musi być sprawdzona pod względem czystości powierzchni. Oceny należy dokonać według EN ISO 8501–1, natomiast badania wykonać zgodnie z postanowieniami norm serii EN ISO 8502. Chropowatość powierzchni oceniać należy wg normy EN ISO 8503, natomiast stopień przygotowania spoin, krawędzi i innych obszarów z wadami powierzchni według EN ISO 8501–3.
Zakres, rodzaj i kryteria akceptacji dla przeprowadzonych badań powinny być uzgodnione i zawarte w specyfikacji. Wszelkie stwierdzone niezgodności należy usunąć, a następnie konstrukcję poddać ponownej kontroli.
Ważnym wymaganiem jest konieczność potwierdzania próbami technologicznymi skuteczności procesu czyszczenia strumieniowo-ściernego pod względem osiąganego stopnia przygotowania i profilu chropowatości powierzchni. Próby takie należy przeprowadzać okresowo w toku produkcji, a ich wyniki powinny być miarodajne z punktu widzenia procesu nakładania powłok.
Innymi wymaganiami załącznika F są: wymaganie niestosowania powłok w obszarze 150 mm od miejsca, gdzie będzie wykonywane spawanie; możliwość zastosowania tylko jednej warstwy podkładowej o maksymalnej grubości 100 µm na powierzchniach stykowych przy połączeniach sprężanych; w przypadku wykonanych połączeń śrubowych ich zabezpieczenie antykorozyjne może nastąpić dopiero po zakończeniu kontroli połączeń.
W odniesieniu do stosowanych powłok ochronnych wymaganiem jest, by w przypadku malowania stan przygotowania powierzchni był zgodny z EN ISO 12944–4, EN ISO 8501, EN ISO 8503–2 oraz zaleceniami producenta materiału powłokowego, który ma być zastosowany. Malowanie należy wykonać zgodnie z normą EN ISO 12944–7, a w przypadku systemu wielopowłokowego należy różnicować odcienie koloru poszczególnych warstw. Prace związane z malowaniem można wykonywać tylko wtedy, gdy warunki otoczenia i powierzchni spełniają wymagania producenta farb. Powierzchnie po nałożeniu powłoki muszą być chronione przez okres wymagany w specyfikacji materiału powłokowego.
Kontrola i ocena zabezpieczeń antykorozyjnych powinna być wykonana zgodnie z opracowanym planem jakości oraz postanowieniami opisanymi poniżej. Inne dodatkowe wymagania w zakresie kontroli i badań powinny być określone w specyfikacji wykonawczej.
Oczywiste jest wymaganie dotyczące dokumentowania procesu kontroli i oceny wykonanego zabezpieczenia.
Ocena rutynowa wykonanych powłok obejmuje: sprawdzenie stanu przygotowania powierzchni; pomiary grubości wykonanych powłok (malarskich wg EN ISO 19840, natryskiwanych cieplnie wg EN ISO 2063, cynkowanych zanurzeniowo wg EN ISO 1461); kontrolę wizualną powłok zgodnie z EN ISO 12944–7. O ile nie określono inaczej, zakres badań musi być następujący: dla każdych 100 m2 powierzchni należy wykonać pięć pomiarów grubości każdej warstwy powłoki na sucho (DFT – ang. dry film thickness); wartość średnia tych pomiarów nie może być mniejsza niż nominalna grubość suchej powłoki (NDFT – ang. nominal dry film thickness); najniższa wartość z tych pięciu pomiarów nie może być niższa niż 80% NDFT; największa wartość z tych pomiarów nie może być na ogół wyższa niż 2 × NDFT, dla krawędzi, spoin i obszarów z wyprawkami 3 × NDFT [3, 4].
Norma EN 1090–2 w załączniku F przywołuje również potrzebę wykonywania powierzchni referencyjnych. Powierzchnie powinny być wyznaczone w specyfikacji wykonawczej i wykonane zgodnie z EN ISO 12944–7. Jeśli nie zostanie ustalone inaczej, powierzchnie referencyjne należy wyznaczyć dla kategorii korozyjności od C3 do C5 oraz od Im1 do Im3
Norma EN 1090–2 zawiera również, nieopisane w niniejszym artykule, wymagania w zakresie powłok metalicznych: natryskiwanych termicznie i cynkowania zanurzeniowego (ogniowego).