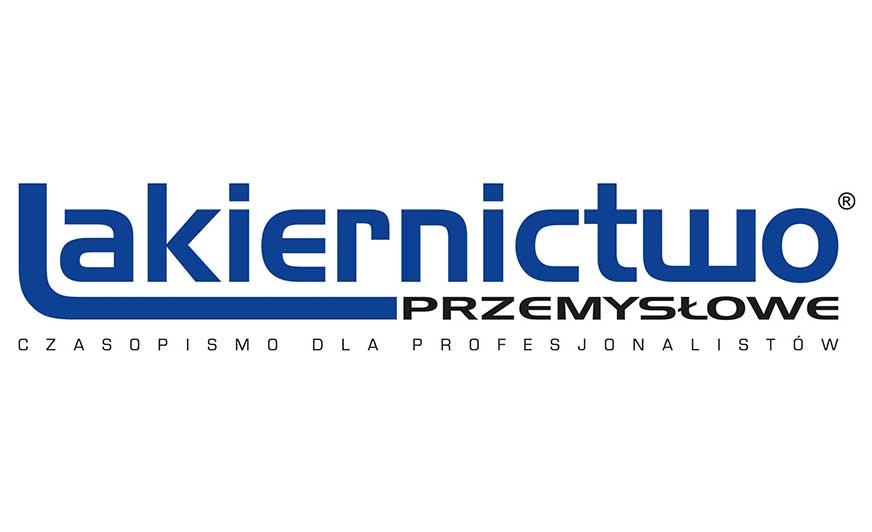
W technologii elektrostatycznego malowania proszkowego na jakość uzyskiwanej powłoki wpływa wiele czynników. Oczywiście podstawą sukcesu jest właściwa receptura produktu. Kontrola parametrów aplikacji jest elementem koniecznym dla właściwego wykorzystania własności produktu i uzyskania powtarzalnych powłok o dobrej jakości. Tylko wtedy, gdy jesteśmy w stanie ocenić przyczyny pojawiających się problemów, możemy mieć wpływ na właściwą, stabilną pracę naszej malarni. Jednym z niezwykle istotnych czynników mających bezpośredni wpływ na jakość procesu malowania proszkowego jest wielkość cząstek podawanych do napylania i ich rozkład granulometryczny (poszczególny udział procentowy cząstek o określonej wielkości). W niniejszym tekście postaram się tę sprawę możliwie przystępnie omówić.
Wpływ granulacji farb proszkowych na ich aplikację
Producenci farb proszkowych wytwarzają swoje produkty starając się dostosować je do napylania przy użyciu możliwie szerokiej gamy dostępnych na rynku urządzeń aplikacyjnych. Głównym celem przy opracowywaniu własności gotowego produktu jest uzyskanie możliwie wysokiego, procentowego współczynnika osiadania na pokrywanych elementach zmniejszającego ilość proszku kierowanego do systemu odzyskowego. Dodatkowo, wymagane jest oczywiście uzyskanie równomiernego pokrycia powlekanej powierzchni i dobrego wyglądu gotowej powłoki. Są to czynniki mające decydujący wpływ na ekonomiczny aspekt procesu malowania proszkowego. Rozkład granulometryczny cząstek jest parametrem technologicznym procesu wytwarzania, pozostającym całkowicie w gestii producenta farby dostarczającego produkt gotowy do zastosowania. Użytkownik powinien mieć jednak świadomość wpływu własności produktu na jego zachowanie podczas aplikacji.
- zachowanie się podawanego materiału w systemie zasilania
- jakość i skuteczność ładowania elektrostatycznego
- wygląd, jakość, powtarzalność uzyskanej powłoki ochronnej
Skład procentowy mieszaniny proszek-powietrze, przepływającej przez aplikator podczas napylania, zaczyna być ustalany w chwili pobierania farby z fluidyzowanego podajnika lub bezpośrednio z opakowania handlowego. Sposób transportu, procentowa zawartość proszku w mieszaninie, prędkość przepływu, wilgotność względna powietrza, temperatura na zewnątrz i wewnątrz malarni, czas i sposób magazynowania, to tylko najbardziej istotne zmienne, jakie należy brać pod uwagę. Problem właściwego podawania proszku do napylania jest szczególnie istotny w konwencjonalnych układach eżektorowych opartych na zwężkach Venturiego. To nadal najbardziej popularne rozwiązanie, obecne w ogromnej większości eksploatowanego aktualnie sprzętu aplikacyjnego, jest bardzo wrażliwe na jakość materiału powłokowego. Dla przykładu, nadmiar drobnych cząstek utrudniania fluidyzację i zwiększa skłonność farby do zbrylania się. Cząstki o małych rozmiarach wypełniają wolną przestrzeń pomiędzy większymi cząstkami, wymuszając podniesienie ciśnienia i wydatku powietrza wspomagającego aerację proszku. Z drugiej strony, zbyt duży wydatek powietrza podawanego do podajnika może prowadzić do niejednorodnej gęstości wewnątrz fluidyzowanej warstwy i pojawienia się gejzerów na jej powierzchni. Zjawisko to związane jest z tworzeniem bąbli przez powietrze napotykające na zbyt mały opór stawiany przez zgromadzony w podajniku proszek. W efekcie otrzymujemy nierównomierny/zmienny w czasie skład mieszaniny proszek-powietrze i duże różnice grubości napylonej powłoki. W granicznych przypadkach może dojść do pulsacyjnego podawania materiału, czego skutkiem jest powstawanie obszarów niedomalowań. Wyższe ciśnienie powietrza zasilającego transport jest jednak w konwencjonalnych układach eżektorowych czasem niezbędne do transportu mieszaniny proszek-powietrze o większym zagęszczeniu. W tym przypadku głównym problemem jest nasilenie ładowania trybostatycznego w przewodach proszkowych, prowadzące do spiekania się ziaren proszku, również na dyszach i wysokonapięciowych elementach aplikatorów. Wyższe ciśnienie powietrza zasilającego transport wiąże się ze wzrostem uzyskiwanej prędkości przesyłania, co w rezultacie zazwyczaj prowadzi do obniżenia efektywności osiadania. Zwiększanie energii kinetycznej podawanego proszku zmniejsza wpływ efektu pola elektrostatycznego na uzyskiwany efekt napylania. Dodatkowo, transport farby z dużą prędkością powoduje jej samoistne rozdrabnianie w wyniku kolizji ze ściankami przewodów i zderzeń pomiędzy cząstkami.
Drobne cząstki farby proszkowej mają większą skłonność do absorbowania wilgoci z powietrza niż większe cząstki. Wynika to z faktu, że mają proporcjonalnie większą powierzchnię zewnętrzną w odniesieniu do masy. Więcej wilgoci zazwyczaj oznacza pojawienie się problemów ze zbrylaniem proszku, co w rezultacie wpływa na pogorszenie efektywności napylania. Na osiadanie farby na pokrywanym elemencie mają również wpływ rozkład granulacji i koncentracja cząstek farby podawanej do aplikatora. Mniejsze cząstki są w stanie zmagazynować większy ładunek elektrostatyczny w przeliczeniu na jednostkę masy, tworząc w wyniku cieńszą warstwę powłoki. Ze względu na wcześniejsze pojawienie się wstecznej jonizacji dochodzi w tym wypadku do szybszego samoograniczenia grubości napylonej warstwy. Przy braku odpowiedniej kontroli procesu zbyt duża koncentracja drobnych cząstek w napylanym materiale może być przyczyną powstawania wad gotowej powłoki, związanych z nasileniem efektu wstecznej jonizacji. Wspomniana wcześniej energia kinetyczna napylanej farby proszkowej może niwelować efekt pola elektrostatycznego i dzieje się tak w zależności od wielkości poszczególnych cząstek. Te mniejsze, magazynujące większy ładunek, są bardziej podatne na odchylanie toru lotu przez linie sił pola. Te większe, magazynujące więcej energii kinetycznej, są trudniejsze do kierowania i dlatego proporcjonalnie częściej opadają na podłogę kabiny proszkowej. Podana zależność w odwrotny sposób odnosi się do zdolności pokrywania zagłębień, w których mamy do czynienia z efektem klatki Faradaya. W tym przypadku podatność na działanie pola elektrostatycznego jest raczej wadą niż zaletą. Cząstki o większej masie łatwiej wnikają w przestrzenie trudne do napylenia. Linie sił pola elektrostatycznego, generowanego pomiędzy wysokonapięciowym aplikatorem a pokrywanym (uziemionym) obiektem, koncentrują się na wszelkich krawędziach i zakrzywiają, tworząc charakterystyczny efekt „otulania”. Stąd powlekane są nie tylko te powierzchnie, które widzimy, ale częściowo również te znajdujące się po niewidocznej stronie obiektu. Ze względu na większą podatność drobnych cząstek farby do podążania za liniami sił pola elektrostatycznego należy spodziewać się ich większej koncentracji w tych obszarach. W oparciu o powyższe informacje można sformułować następujący wniosek – gdy podczas powlekania pojawiają się równocześnie trudności z uzyskaniem odpowiedniej grubości napylanej warstwy oraz pogorszenie penetracji farby w obszary, gdzie występuje efekt klatki Faradaya, najprawdopodobniej w aplikowanym produkcie jest zbyt wiele drobnych cząstek.
Ze względu na największy atut technologii malowania proszkowego, czyli możliwość odzysku/ponownego użycia farby, która nie osiadła na pokrywanym elemencie, wielu użytkowników nie dba o to, by maksymalizować osiadanie podczas pierwszego napylania. Jest to bardzo duży błąd, ponieważ systemy odzysku, nawet te najbardziej nowoczesne, mają negatywny wpływ na własności materiału powłokowego. Możemy spodziewać się z różnym nasileniem następujących różnic jakościowych:
- zmiana rozkładu granulometrycznego proszku odzyskowego w stosunku do proszku pierwotnego
- obniżenie zdolności ładowania i osiadania
- pojawienie się zanieczyszczeń w napylanym materiale
- bezpowrotna utrata części materiału powłokowego