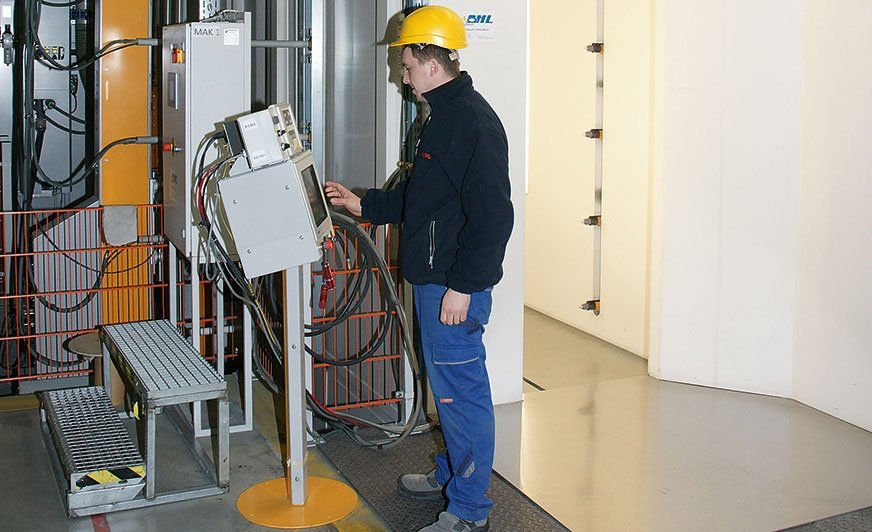
Przestrzeganie zaleceń i utrzymanie reżimu technologicznego ma ogromny wpływ na jakość otrzymanej powłoki malarskiej. Fot. Julian Ciesielski
Wpływ parametrów malowania proszkowego na jego efekty końcowe
Wynik pozytywny oceny efektu malowania proszkowego, przeprowadzenie malowania w optymalnych dla producenta warunkach techniczno-ekonomicznych i satysfakcję odbiorcy zapewnić mogą tylko monitoring i ciągłe korygowanie parametrów – uwarunkowań procesów podstawowych i związanych. Bardzo duża liczba czynników mających wpływ na jakość może spowodować, że przestrzeganie zaleceń i starania utrzymania tzw. reżimu technologicznego nie wyeliminują powstałych nieprawidłowości całkowicie – w znacznym jednak stopniu je ograniczą.
Wiadomo, iż malowanie proszkowe uprzednio odpowiednio przygotowanych powierzchni polega na napyleniu na nie specjalnej farby pod postacią sypkiego proszku, stopieniu jej i następnie utwardzeniu. Celem procesu jest uzyskanie użytkowej powłoki ochronno-dekoracyjnej o określonych, pożądanych własnościach, jak: grubość, kolor, połysk, przyczepność, odporność korozyjna, na światło, chemiczna, odporność na zarysowania, twardość, odporność na zginanie (elastyczność), na uderzenia.
Oprócz wymienionych wyżej podstawowych operacji należy wykonać również prace wstępne i zakończeniowe, jak załadunek (np. zawieszanie) przedmiotów, które będą malowane, na odpowiednie środki transportu przemieszczającego się przez poszczególne fazy procesu oraz na końcu ich rozładunek.
Dobór i ustalanie parametrów dokonywane jest w oparciu o założenia, dane wejściowe, którymi są: rodzaj materiału malowanego (stal czarna, ocynkowana, nierdzewna, inny materiał), stan powierzchni surowych (rdza, korozja, naloty, wżery, zanieczyszczenia mechaniczne, olej, tłuszcz, smar, emulsja), charakterystyka detali malowanych (płaskie, przestrzenne, mało lub wielkogabarytowe), wymiary, grubość ścianek, ciężar – waga, wielkość powierzchni, warunki pracy po pomalowaniu – wewnętrzne czy zewnętrzne oraz wyniki badań i testów własnych.
I tak zaczynając od czynności pomocniczych, jakimi są te związane z załadunkiem elementów, które mają być pomalowane – w szczególnym przypadku realizowanych np. przez zawieszanie ich na środki transportu podwieszonego, zaleca się stosowanie między innymi zasad: ze względów ekonomicznych uwzględniać konieczność maksymalnego wykorzystywania dysponowanej pod przenośnikiem przestrzeni, zapewniając jednocześnie poprawny, bezkolizyjny – bez ocierania, obijania się – przebieg wszystkich faz procesu. Wynikające z powyższego stosowane praktycznie odstępy pomiędzy detalami powinny wynosić: dla elementów płaskich ok. 100 mm, zwiększając je wraz ze wzrostem głębokości detali do wartości 500-600 mm dla elementów przestrzennych, czyli brył. Ustalenia te dotyczą transportu odbywającego się na jednym poziomie. W przypadku istnienia podjazdów i zjazdów przenośnika należy ustalić i uwzględnić wzajemne zachowanie się (kolizje) podwieszonych elementów. Zaleca się również zawieszać je w pozycji pionowej, wzdłuż dłuższych osi symetrii, małe rzędami jedne pod drugimi. Zawieszone elementy powinny zapewniać ergonomiczną pozycję pracy malarzy.
W przypadku występowania w obrabianych elementach powierzchni, które mają być niepomalowane, należy je zabezpieczyć (zamaskować) przez zakrycie, osłonięcie przy użyciu odpowiednich śrub, zaślepek lub taśm. Pomoce do tego służące można wykonać we własnym zakresie lub zakupić w specjalistycznej firmie.
W wyniku nieprawidłowości występujących podczas zabiegów zawieszania detali i ich ruchu podczas transportu powstać mogą na pomalowanych powierzchniach nieprawidłowości, takie jak: ślady po zawieszkach, ślady powstałe w wyniku wzajemnych kolizji (rysy, zadrapania), uszkodzenia mechaniczne (skrzywienia, pogięcia), niedomalowania, zacieki, sople.
Stan przygotowanych do malowania powierzchni niejednokrotnie jest czynnikiem decydującym o końcowym efekcie, pozytywnym lub nie, całego procesu malowania. Przygotowanie do malowania polega na usunięciu z powierzchni malowanych wszelkiego rodzaju zanieczyszczeń, a często wytworzeniu również warstwy konwersyjnej, która dzięki swoim własnościom hamuje procesy utleniania i zapewnia odpowiednią przyczepność farby do podłoża. Proces przygotowania powierzchni jest prowadzony najczęściej przez obróbkę mechaniczną lub chemiczną. Obróbka mechaniczna umożliwia usunięcie zanieczyszczeń, takich jak rdza, zgorzelina, stare powłoki oraz rozwija powierzchnię, nadając jej również odpowiednią chropowatość. Metody chemiczne dodatkowo usuwają zanieczyszczenia w postaci smarów, olejów, tłuszczów, soli, brudu, kurzu, pyłu, gwarantując pożądaną przyczepność oraz odporność korozyjną powierzchni tak przed, jak po malowaniu.
Ze względu na ważność tej fazy dla końcowych efektów procesu malowania proces przygotowania powierzchni powinien być omówiony priorytetowo w oddzielnym opracowaniu, w którym naturalnie będą opisane wszystkie jego parametry.
Efekt końcowy samego procesu przygotowania powierzchni ocenia się przed operacją napylania farby w zasadzie w sposób optyczny, wizualny opisując zaistniały stan i oceniając brak lub obecność zanieczyszczeń, wielkość chropowatości i stopień czystości (wg PN-EN ISO 8501.1). Po obróbce chemicznej również wygląd powierzchni: równomierność filmu wodnego, występowanie skroplin, wygląd powłoki (np. równomierna, intensywna, zamknięta) pylistość, występowanie osadów, barwę.
Wadami wynikającymi z powodu źle przygotowanej powierzchni, z których niestety większość ujawnia się dopiero po ostatniej fazie procesu, tj. po utwardzeniu, mogą być: wtrącenia i zanieczyszczenia, zła przyczepność powłoki, pęcherze, plamy, kratery, rybie oczka, dołkowatość, pęknięcia, odstawanie, podnoszenie powłoki, niezadowalające własności mechaniczne lub chemiczne.
Dwie kolejne fazy procesu malowania, które określić można mianem podstawowych, zasadniczych, to: nałożenie na powierzchnie obrabiane farby proszkowej i jej utwardzenie. Nakładanie farby realizowane jest najczęściej poprzez napylenie elektrostatyczne, tarciowe (tribo) lub metodami zanurzeniowymi.
Napylanie elektrostatyczne to nanoszenie, z wykorzystaniem aplikacji, na malowane podłoże odpowiednio przygotowanej przez fluidyzację, jonizację, polaryzację farby proszkowej. W rezultacie powoduje to jej ładowanie, tj. uzyskanie ładunku elektrycznego i w konsekwencji zjawisko przyczepności i krycia. Napylanie może odbywać się ręcznie lub w sposób automatyczny, np. przy ciągłym ruchu przenośnika.
Podstawowymi parametrami przy metodzie elektrostatycznego ładowania farby, której nośnikiem jest sprężone powietrze są nastawy elektryczne – napięcie ładowania do około 90 kV, ciśnienie oraz odległość dysz napylających pistoletów od malowanych powierzchni, standardowo dla płaszczyzn wynosząca ok. 250 mm.
W procesie automatycznego napylania farb wielkości napięciowo-ciśnieniowe są niejako poza strefą oddziaływania obsługi. Przy malowaniu ręcznym zależą generalnie od operatorów. W związku z tym należy tutaj podkreślić, że zawyżanie szczególnie dwóch pierwszych parametrów jest nieekonomiczne – nie zwiększając wydajności powoduje zwiększenie zużycia farby i źle wpływa na jakość wymalowań.
W przypadku malowania ręcznego bardzo istotnymi czynnikami są kwalifikacje i wprawa malarzy. Brak takowych jest powodem występowania możliwości całego szeregu wad, które wymienię poniżej.
Przy malowaniu automatycznym przy ciągłym ruchu transportu detali bardzo ważnymi parametrami są odpowiednio dobrana prędkość przenośnika, liczba i ustawienie pistoletów oraz koordynacja wzajemnych ruchów przenośnika i aplikacji. Zastosowanie oscylacyjnych manipulatorów i/lub robotów malarskich redukuje koszty pracy, zapewnia utrzymanie na stałym poziomie podstawowych parametrów, a tym samym powtarzalność wyników malowania i jakości, eliminując jednocześnie związane z tym wady. Wadami związanymi z omówionymi wyżej parametrami są: zbyt mała lub zbyt duża grubość powłoki, nierównomierność powłoki, niedomalowania, zacieki, sople, skórka pomarańczowa, falistość, pomarszczenia, pofałdowania, morka.
Na końcowy uzyskiwany efekt malowania oprócz opisanych do tej chwili parametrów – czynników ma również nie mniejszy wpływ zastosowana farba oraz jej stan. Rodzaj farby, jej kolor (barwa), połysk (wybłyszczenie) zależą po części od odbiorcy (klienta), czyli warunków odbioru, jak i od projektanta malowanej konstrukcji. Wynikają też z warunków eksploatacji w jakich elementy pomalowane będą pracować (wymalowania wewnętrzne czy zewnętrzne). Na etapie stosowania farby w praktyce istotna jest kontrola jej stanu, który musi być zgodny z przyjętymi założeniami i wymaganiami. Informacje o farbie zawarte są w dostarczanym przez producenta do każdej jej partii certyfikacie – świadectwie jakości, a te podstawowe na etykiecie opakowań. Informacje zaś o zagrożeniach, niebezpiecznych właściwościach oraz zasadach i zaleceniach ich bezpiecznego stosowania podane są w tzw. kartach charakterystyki danych substancji niebezpiecznych.
Istotne dane związane z farbami to: dane producenta, rodzaj farby, nazwa, oznaczenie, kolor, numer partii produkcyjnej, data produkcji, data ważności, zalecana aplikacja, np. corona lub tribo, zalecane zakresy temperatur i czasów utwardzania, ciężar właściwy, stopień wybłyszczenia (połysku), warunki przechowywania. Na żądanie dostawca poda wskaźniki charakteryzujące kolor, przyczepność, dane granulometryczne, wybrane własności mechaniczne i chemiczne finalnych powłok.
Przykładowe, orientacyjne, bardzo ogólne i zalecane dane techniczne większości farb termoutwardzalnych: ciężar właściwy 1,4-1,8 g/cm³, wydajność 9-12 m²/kg, pożądana przyczepność Gt0 wg PN-EN ISO 2409, wielkość ziaren 15-100 µm i np. ilość cząstek mniejszych niż 15 µm poniżej 10%, zaś ziaren o grubości 120 µm nie więcej niż 20%. Temperatura przechowywania poniżej 25°C przy wilgotności powietrza w pomieszczeniu do 60%.
Wady jakie mogą powstać z powodu złego stanu farb to: niezadowalająca przyczepność, wtrącenia, zanieczyszczenia, niezgodny kolor i połysk, igłowanie, warzenie się farby, kredowanie, żółknięcie, niezadowalające własności mechaniczne i/lub chemiczne.
Powietrze służące do transportu napylanej farby powinno być suche, bezolejowe i wolne od zanieczyszczeń – sprężone w kompresorze (zaleca się śrubowy). Stopień oczyszczenia (filtracji) powietrza, przy zastosowaniu osuszacza np. chłodniczego wg normy PN-EN ISO 8573.1, powinien być zgodny z punktem 1.4.1, co oznacza: maks. wielkość cząstek stałych 0,1 µm, maks. gęstość cząstek stałych w powietrzu 0,1 mg/m³, ciśnieniowy punkt rosy < +3°C (5,9 g pary wodnej w m³), łączna zawartość oleju < 0,01 mg/m³.
Możliwe wady spowodowane niezgodną jakością powietrza to w szczególności: wtrącenia i zanieczyszczenia, igłowanie, dziurkowatość, nakłucia, pęcherze, plamy, przebarwienia.
Ostatnią fazą procesu malowania proszkowego jest utwardzanie napylonej farby polegające na jej stopieniu – upłynnieniu, sieciowaniu, zżelowaniu i w rezultacie uzyskaniu stałej i trwałej powłoki. Dla standardowego, konwekcyjnego utwardzania farb uniwersalnych typu mix, tj. epoksydowo-poliestrowych, główne parametry tego procesu są rzędu: temperatura pracy 180-200°C w czasie 10-20 minut przy zaznaczeniu, że jest to czas przebywania w określonej temperaturze już uzyskanej przez wygrzewany przedmiot. Wielkości szczegółowe, dokładne tych parametrów, o czym była już wzmianka, ustala się w oparciu o warunki wejściowe, takie jak charakterystyka elementów obrabianych, rodzaj dobranej farby, masę wsadu pieca, grubość ścianek detali oraz na podstawie ewentualnie przeprowadzonych prób i testów wstępnych.
W odniesieniu do urządzeń grzewczych, np. dla standardowych pieców konwekcyjnych, przyjmuje się, że w celu uzyskania prawidłowych, jednorodnych powłok różnica temperatur pomiędzy strefą górną (sufitem) a dolną (podłoga) nie powinna przekraczać 10-15°C, zaś po nagrzaniu pomiędzy poszczególnymi punktami przedmiotu 5-10°C.
W rezultacie źle dobranych lub stosowanych parametrów utwardzania możliwe jest wystąpienie wad, takich jak: nieprawidłowa przyczepność powłoki, zacieki, sople, niezgodność połysku, igłowanie, żółknięcie, niezadowalające własności mechaniczne i/lub chemiczne powłok, niezgodna lub nierównomierna twardość.