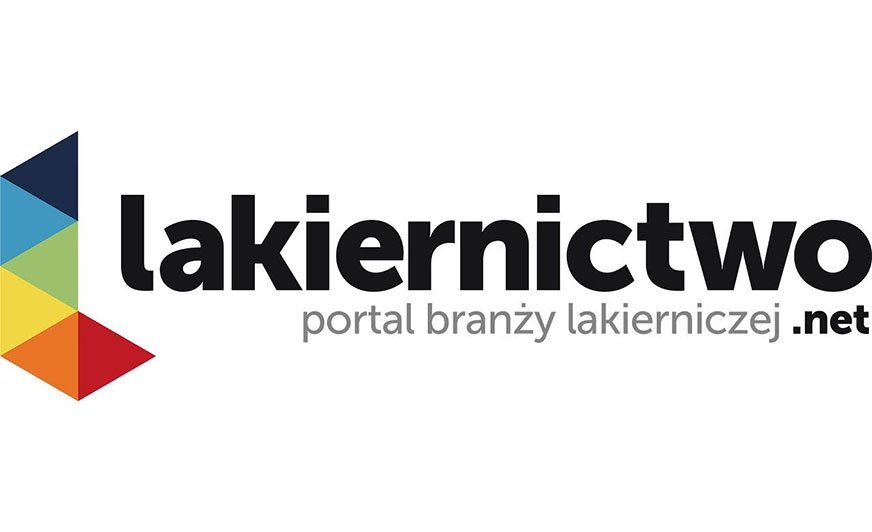
Specjalna szczotka obrotowa Bristle Blaster i szczotka wymienna firmy Monti.
Urządzenia do obróbki strumieniowo--ściernej powierzchni
Obróbka strumieniowo-ścierna pneumatyczna i wirnikowa jest metodą najważniejszą, gdyż tylko ona pozwala uzyskiwać najwyższy stopień przygotowania powierzchni Sa 3 wg PN EN ISO 8501-1, uzyskiwać poziom parametru chropowatości RZ i RY w szerokim zakresie, od 20 do 120 μm z wydajnością od 0,5 m2/h (warsztatowe oczyszczarki bezpyłowe) do 1000 m2/h (linie wirnikowe do czyszczenia blach i kształtowników).
Do urządzeń służących do obróbki strumieniowo-ściernej należą:
- oczyszczarki pneumatyczne z otwartym obiegiem ścierniwa (terenowe) i z zamkniętym obiegiem (komory pneumatyczne, oczyszczarki wirnikowe do wyrobów hutniczych, odlewów: ze stołem obrotowym, taśmowe, hakowe, zawieszkowe, bębnowe, rynnowe) do rur, drutów i konstrukcji
- oczyszczarki bezpyłowe chroniące środowisko naturalne (z głowicami umożliwiającymi odsysanie ścierniwa i powrót do wewnętrznego obiegu)
- oczyszczarki ze zwilżonym strumieniem ścierniwa (dysze zraszające), oczyszczarki mokrym ścierniwem (TORBO)
- oczyszczarki z zawiesiną ścierniwa w wodzie (Quill, SandBot)
- monitory wytwarzające strumienie wody ze ścierniwem pod wysokim i ultrawysokim ciśnieniem (30 do 300 MPa)
- hydromonitory czyszczące samą wodą pod ciśnieniem nawet wyższym od 300 MPa do usuwania starych powłok lakierniczych, bez możliwości chropowacenia powierzchni, głównie w stoczniach remontowych.
Oczyszczarki pneumatyczne
Najprostszą oczyszczarką pneumatyczną jest „piaskarka” z otwartym obiegiem ścierniwa. Rozróżnia się oczyszczarki ciśnieniowe, które czerpią ścierniwo ze zbiornika znajdującego się pod ciśnieniem sprężonego powietrza, oraz inżektorowe, które zasysają ścierniwo ze zbiornika pozbawionego ciśnienia, skąd strumień powietrza zlokalizowany poniżej zaworu zsypowego zasysa je do węża zawierającego sprężone powietrze. Taki rodzaj oczyszczarki jest dwukrotnie mniej wydajny niż ciśnieniowej. Oczyszczarki inżektorowe stosowane są w kabinach rękawowych do oczyszczania drobnych detali. Oczyszczarki ciśnieniowe stosowane są najczęściej przy pracach w terenie otwartym, pod wiatami w wytwórni konstrukcji, pod namiotem lub w pomieszczeniu wentylowanym. Stosuje się wtedy ścierniwa jednokrotnego użytku, najczęściej żużel pomiedziowy (produkt odpadowy z huty miedzi) oraz z gorszym skutkiem żużel wielkopiecowy, konwerterowy, paleniskowy, a w krajach posiadających huty niklu – żużel poniklowy.
W naszym kraju niezwykle popularny był piasek kwarcowy, którego stosowanie w krajach Europy Zachodniej i Ameryce było zakazane od wczesnych lat pięćdziesiątych ubiegłego wieku. W Polsce został wydany zakaz stosowania piasku na sucho z chwilą naszego wejścia do Unii Europejskiej (od 1 maja 2004 r.). Piasek kwarcowy, piaski rzeczne i żwiry zawierają od 80 do 99% wolnej krystalicznej krzemionki, wywołującej po kilkunastu latach piaskowania, mimo stosowania kasków przewietrzanych, chorobę zawodową zwaną krzemicą oraz znajduje się w wielu krajach na liście substancji prawdopodobnie wywołujących raka.
W krajach pozaeuropejskich, gdzie występują pokłady skalne i piasków granatu almandynowego, zwanego garnetem, spotyka się najczęściej to uniwersalne ścierniwo niezawierające wolnej krzemionki, nadające się, tak jak elektrokorund, do czyszczenia wszystkich materiałów z wyższą wydajnością od piasków i żużli odpadowych.
Ścierniwo to pozwala na kilkakrotne jego użycie. Ten fakt spowodował, że skonstruowano separatory zanieczyszczeń garnetu działające okresowo. Po pracy zbiera się użyte ścierniwo, np. ssawą pneumatyczną, i zasypuje do separatora zanieczyszczeń. Pozwala to na oszczędność kosztów oczyszczania do 70%. Bogatsze kraje poszły jeszcze dalej i skonstruowały system pełnego zawracania ścierniwa do obiegu w terenie, składający się z łatwo montowalnych osłon i rynien zsypowych podłączonych do podciśnieniowego transportu ścierniwa, jego separatora, zasypnika automatycznego do oczyszczarki oraz filtra powietrza. Wszystkie te urządzenia montowane są na olbrzymiej platformie kolejowej lub samochodowej albo na podwoziach dla poszczególnych urządzeń, łącznie z napędowymi silnikami spalinowymi i sprężarkami wytwarzającymi sprężone powietrze, i do transportu pneumatycznego oraz oczyszczania powietrza. W ten sposób na budowach mostów i wysokich konstrukcji stalowych stosowany jest nawet śrut staliwny łamany.
W wielu polskich przedsiębiorstwach „piaskuje” się żużlem pomiedziowym lub śrutuje w pomieszczeniu, zawracając brudne i rozbite ścierniwo łopatą. Ten fakt powoduje mniejszą trwałość ścierniw wielokrotnego użytku oraz dodatkowe zabrudzenie powierzchni oczyszczanej, dając przeciwny skutek do zamierzonego. Niektóre firmy zawracają w ten sposób żużel pomiedziowy do dziewięciu razy! Nie zdają sobie sprawy z ogromnej rozpiętości uzyskiwanej chropowatości powierzchni po jednym zasypie i po dziewiątym. Żużel pomiedziowy określa się bowiem jako ścierniwo dopuszczone do 1,5-krotnego użycia, co oznacza, że 50 proc. ziaren ścierniwa zmniejsza swoją wielkość już po pierwszym zderzeniu się z powierzchnią oczyszczaną, a więc zdolność do chropowacenia na oczekiwanym poziomie parametru chropowatości spada gwałtownie.
Wobec ponoszenia coraz wyższych kosztów utylizacji i składowania zużytego ścierniwa oraz transportu ścierniwa i odpadu, a także wymogów ochrony środowiska mówiących, że ilość odpadów, a więc i ścierniwa, ma się zmniejszyć do 2023 roku o 2/3 w stosunku do roku 2000, warto się zastanowić nad stosowaniem ścierniw wielokrotnego użytku w komorach pneumatycznych lub wirnikowych. Albo też adaptacją pomieszczeń do stosowania ścierniw wielokrotnego użytku, takich jak śruty, elektrokorund zwykły, a nawet granatu almandynowego. Można ten cel osiągnąć etapami, zaopatrując się najpierw w separator zanieczyszczeń ścierniwa posiadający ssawkę podobną do odkurzacza przemysłowego do zbierania zużytego ścierniwa z posadzki lub w zasyp podnośnika kubełkowego sprzężonego z separatorem umiejscowionym na poziomie podłogi.
Następnym etapem jest położenie cienkiej, bo ok. 30-centymetrowej podłogi z kratkami i listwami elastycznymi, przegarniającej ścierniwo w kierunku zasypu separatora zanieczyszczeń. W ten sposób zamyka się obieg, bo separator kieruje oczyszczone ścierniwo do silosa zasypowego usytuowanego nad oczyszczarką lub zbiornika ciśnieniowego dozującego ścierniwo bez potrzeby dekompresji oczyszczarki. Potrzebne też jest podwyższenie zdolności wentylacji pomieszczenia, gdyż część powietrza będzie obsługiwać separator zanieczyszczeń i transport pneumatyczny ścierniwa do separatora, zwłaszcza w przypadku zaopatrzenia go w ssawę.
Do prac w terenie, oprócz tradycyjnych „piaskarek”, stosuje się przewoźne przemysłowe oczyszczarki bezpyłowe o wydajności oczyszczania tylko o 20 proc. niższych niż zwykłe piaskarki. Głowica czyszcząca posiada wymienne szczotki przylgowe dostosowane do kształtu oczyszczanej powierzchni (płaskie, narożnikowe wewnętrzne i zewnętrzne). Zastosowanie natomiast jako ścierniwa elektrokorundu zwykłego zamiast śrutu pozwala zniwelować tę różnicę.
Lansuje się od pewnego czasu czyszczenie przy podwyższonym ciśnieniu rzędu 1 MPa, uzyskując wzrost wydajności czyszczenia, ale przy ok. 50 proc. mniejszej trwałości ścierniwa, większym zapyleniu, większym wysiłku operatora i podwyższeniu hałasu ponad 96 dB.