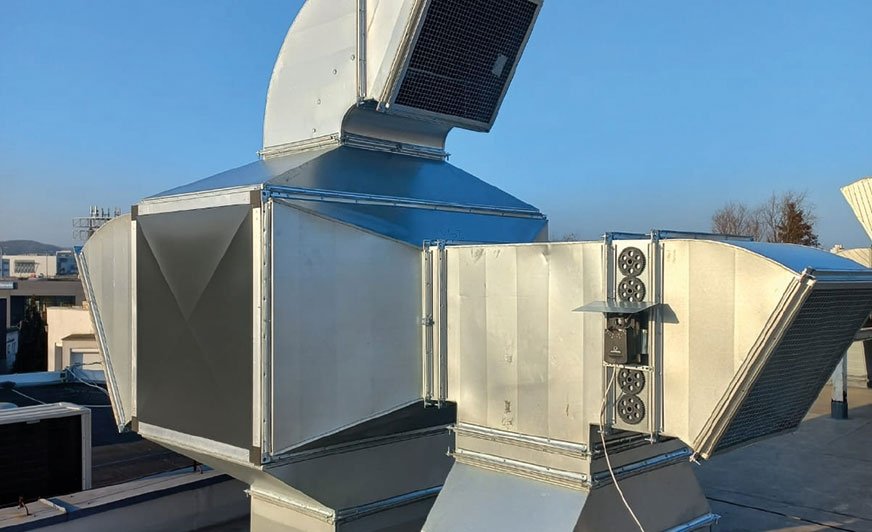
Rekuperacja − firma RAFKO
Rozwiązania mogące pomóc zaoszczędzić energię
Postęp technologiczny ostatnich dekad ma swoje odzwierciedlenie także w obecnie produkowanych lakierniach. Można powiedzieć, że kabiny „urosły”, a ich wentylacja jest bardziej wydajna. Mamy też nową normę z wytycznymi dla producentów takich urządzeń (PN-EN 16985:2019-02), sugerującą opad powietrza w lakierni na poziomie 0,3 m/s.
Możemy też zauważyć, że w okresie ostatnich 30–40 lat moce wentylatorów się podwoiły, dodano dodatkowe agregaty wyciągowe wspomagające pracę kabiny, a także umożliwiające instalację dodatkowych filtrów na wylocie z nich. W latach osiemdziesiątych XX wieku podstawowy model kabiny miał wymiary 6 metrów długości, 4 metry szerokości i 2,5 metra wysokości, zasilał go pojedynczy agregat grzewczo-nawiewowy z silnikiem 4 lub 5,5 kilowata. Wydajność wentylacji była na poziomie 15 tysięcy metrów sześciennych na godzinę. Do ogrzania takiego wolumenu powietrza wystarczał palnik o mocy 100–120 kilowatów. W porównaniu do dzisiejszych standardów urządzenia z przełomu lat siedemdziesiątych i osiemdziesiątych nie były bardzo energochłonne i na ogół były wyposażone w jeden generator. Dzisiejsze kabiny są większe, standardem stało się 7–8 metrów długości , 4–5 szerokości i do 3 metrów wysokości. Dzisiejsze pojazdy malowane w nich są większe niż kiedyś, stąd lakiernie także musiały się do nich dostosować. Z czasem zwiększyły się także wymogi bezpieczeństwa dotyczące prędkości przepływu powietrza – kolejne normy zalecały producentom coraz większe wartości. Aktualna norma PN-EN 16985:2019-02 sugeruje opad powietrza na poziomie 0,3 m/s. Aby sprostać tym wyzwaniom producenci zaczęli stosować dużo większe jednostki wentylacyjne – standardem stały się silniki w przedziale 7,5 kW do nawet 15 kW. Także normą w dzisiejszej dobie są lakiernie wyposażone w dwa generatory, jeden grzewczo-nawiewowy, a drugi filtrująco-wyciągowy. Można powiedzieć, że w ostatnich kilku dekadach zapotrzebowanie energetyczne lakierni wzrosło kilkukrotnie. Silniki kilkukilowatowe zastąpiono kilkunastokilowatowymi, a moc grzewcza wzrosła ze 100 do 250 kilowatów. Parametry te w znacznym stopniu podnoszą koszty pracy lakierni, dlatego też producenci wdrażają nowe rozwiązania technologiczne, które pozwalają na zmniejszenie zapotrzebowania na energię.