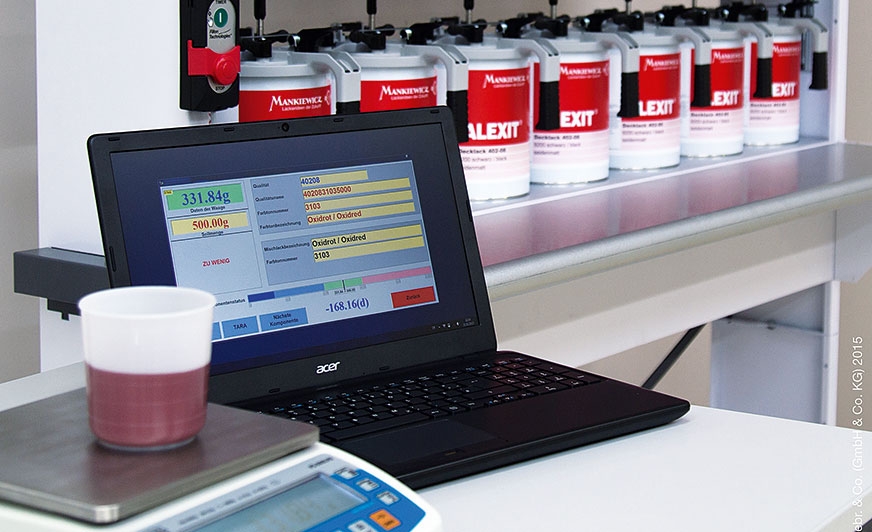
System mieszania i dozowania farb na miejscu z zakładzie produkcyjnym przynosi wiele korzyści i jest prosty w obsłudze.
Dotychczas dość rzadko spotykano mieszalniki barw w zakładach produkcyjnych – użytkownicy przemysłowi nie mieli odpowiednich kompetencji oraz czasu na mieszanie kolorów samodzielnie. To zadanie wykonywali zazwyczaj lokalni dystrybutorzy produktów lakierniczych. Teraz może się to zmienić! Firma Mankiewicz z Hamburga ma nowatorskie rozwiązanie.
Firma Sauer Compressors produkuje sprężarki powietrzne lub chłodzone wodą używane w żegludze, przemyśle i marynarce. Przedsiębiorstwo wykonuje obecnie osiem różnych serii produkcyjnych dla 46 typów sprężarek i dostosowuje je do indywidulanych potrzeb swoich klientów. Przede wszystkim produkcja obejmuje wielkość partii - jeden a czasem też trzy modele tego samego typu. Jak informuje kierownik zakładu Bernhard Ahlke, rocznie produkuje się tutaj 3000 sprężarek.
Ponieważ klienci często zamawiają sprężarki w specjalnych kolorach, lakiernia Sauer i Synowie w Kilonii musi dużo czasu poświęcić planowaniu. Również magazyn lakierni nie był w stanie pomieścić wszystkich pojemników z resztkami lakierów. Dzięki mieszalni farb każdy może w ciągu kilku minut stworzyć samemu prawie każdy odcień farb – i to w potrzebnej ilości.
Nieużywanie pieca – oszczędność kosztów
Nic więc dziwnego, że panowie Ahlke i Janas poszukali innej metody i przestawili się na system ALEXIT Topcoat 402-08 firmy Mankiewicz. Od tego momentu elementy do obróbki po lakierowaniu suszone są w warunkach naturalnych. – Po 20 minutach można je dotknąć ręką, a po maksymalnie dwóch godzinach sprężarki i cylindry poddawane są dalszej przeróbce – wyjaśnia Ahlke. – Dla nas był to olbrzymi krok w kierunku przyspieszenia cyklu produkcyjnego. Poza tym oszczędzamy na kosztach energii od 35 tys. do 40 tys. euro rocznie przez to, że nie używamy pieców – jest to znaczna suma, którą można zainwestować znacznie lepiej. Inny pozytywny efekt uboczny: można było zdemontować piec, tak że zyskano więcej miejsca w lakierni.
W kwestii jakości lakiery spod znaku ALEXIT także przekonały kilończyków. – Nowy typ lakieru ma wyraźnie wyższą odporność niż nasz poprzedni system lakierniczy – uważa Janas.
Każda sprężarka przed opuszczeniem zakładu stawiana jest na stanowisko kontrolne na 16 godzin. Tutaj przyłączane są kable, przewody ciśnieniowe oraz częściowo przewody chłodzone wodą, często elementy armatury uderzają przy tym w sprężarkę. – Obecnie stosowany lakier nie jest taki wrażliwy na uszkodzenia jak ten stosowany przedtem – tak brzmi krótkie podsumowanie ze strony firmy z Kilonii.
Znaczna redukcja procesu technologicznego
Około 65% sprężarek produkowanych dla przemysłu okrętowego w firmie Sauer pokrywanych jest standardowo zielonkawą powłoką według skali Munsella. Niektórzy klienci zamawiają sprężarki indywidualnie pod dany wygląd – czasami nawet w kolorze fioletowym. – Do tej pory musieliśmy zamawiać u producenta kompletne 12-kilogramowe opakowanie lakieru – wspomina Janas. – Na pomalowanie sprężarki zużywany jednak maksymalnie dwa kilogramy – reszta lądowała w magazynie do późniejszego ewentualnego wykorzystania.
Inna pojawiająca się trudność: w przypadku farb specjalnych mamy do czynienia z długim okresem realizacji i projektowania. Ponieważ trwałość lakierów podczas składowania jest dosyć ograniczona, dużą część resztek trzeba po prostu usunąć. Prowadzi to do zapełniania nie tylko magazynu, lecz też powstania dużych ilości odpadów.
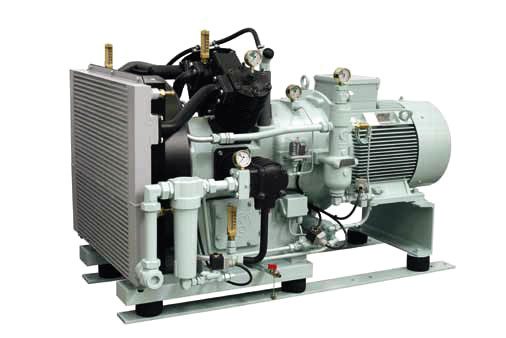
Najmniejsze ilości od 500 g
Thorsten Petersen, doradca przemysłowy w firmie Mankiewicz, poinformował producentów z Kilonii o nowym systemie mieszania i dozowania farb będącym w ofercie firmy już od roku. Dzięki niemu można wytwarzać bezpośrednio na miejscu farbę w kolorystyce wg RAL, Munsell i NCS – także w małej ilości od 500 g. Gotowe odcienie farb mieszane są z palety 14 podstawowych farb pigmentowanych pojedynczym pigmentem. – Przypomina to system mieszania stosowany w lakierniach samochodowych – wyjaśnia Petersen. – Farby otrzymane z urządzenia do mieszania mają taką samą jakość jak ALEXIT Topcoat 402-08 produkowane na linii produkcyjnej firmy Mankiewicz w zakładzie w Hamburgu.
W skład systemu wchodzą urządzenie mieszalnicze i waga podłączona do notebooka. Dzięki odpowiedniemu oprogramowaniu można ustalić precyzyjnie ilości składników. Firma Mankiewicz dostarcza sprzęt komputerowy i oprogramowanie oraz zintegrowany, autorski program do obliczeń kolorów.
Nowy odcień w 5-10 minut
W lutym w firmie Sauer Compressors zainstalowano nowe urządzenie do mieszania i dozowania farb, które działa już od marca. Zdaniem Bernharda Ahlke, obsługa urządzenia jest bardzo prosta. Wystarczyła krótka instrukcja do jego uruchomienia. Stworzenie nowego odcienia farby trwa od 5 do 10 minut, zamiast jak do tej pory kilka dni, zanim kurier dostarczył pojemnik z farbą.
Obecnie urządzenie w Kilonii używane jest trzy do czterech razy tygodniowo. – W naszym magazynie lakieru w ciągu ostatnich sześciu miesięcy zrobiło się o wiele więcej miejsca – stwierdza kierownik sekcji lakierniczej. – Mieszalnia lakierów była dla naszej firmy olbrzymim krokiem do przodu, i nie tylko dlatego, że oszczędzamy na kosztach energii, lecz także na kosztach materiału i składowania. Dzięki temu uprościliśmy nasz proces produkcyjny i przyszłościowo chcemy wykorzystać ten system w naszych innych zakładach produkcyjnych.
Mankiewicz Lakiery Przemysłowe